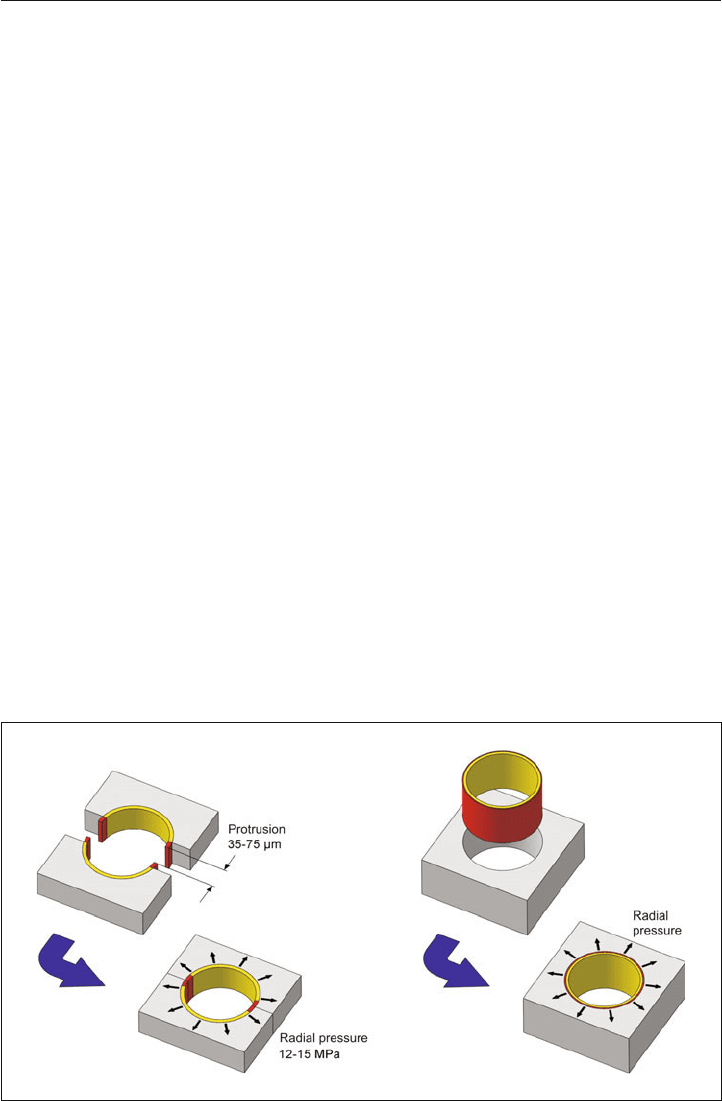
3.3 Bearing geometry 57
lower clearances also generate more heat, which reduces the oil viscosity. The maximum oil
film pressure increases more or less proportionately with greater clearance (Figure 3.13), and
the minimum oil film thickness decreases (Figure 3.14). The recommended starting value for
diametric clearance is 0.1% of the bearing diameter.
3.3.4 Bearing and bushing fit
A properly designed fit of the bearing in its housing ensures a reliable seat and good heat
transfer due to radial tension. This is achieved through correct design of the bearing overlap.
For bearings, this overlap results from the protrusion of the parting line height beyond the
housing radius, (Figure 3.15). For bushings, it is the difference in diameter between the hous-
ing ID and the bushing OD.
Computation of the overlap allows optimization of the assembly conditions. The calculated
radial pressures should be greater than 10 MPa, and the stresses in the bearing should not
exceed 450 MPa.
3.3.4.1 Eccentricity
Bearing eccentricity is the difference between the vertical and the horizontal diameter. The
eccentricity helps in generating adequate oil film thicknesses, but also avoiding any heavier
contact of the journal on the sliding surface when the connecting rod closes in towards the
par
ting line region due to dynamic distortion. A simulation of the elasto-hydrodynamic lubri-
cation (EHL), using a special analysis program, allows the selection of the optimal eccentric-
ity for each application.
Figure 3.15: Development of radial pressure