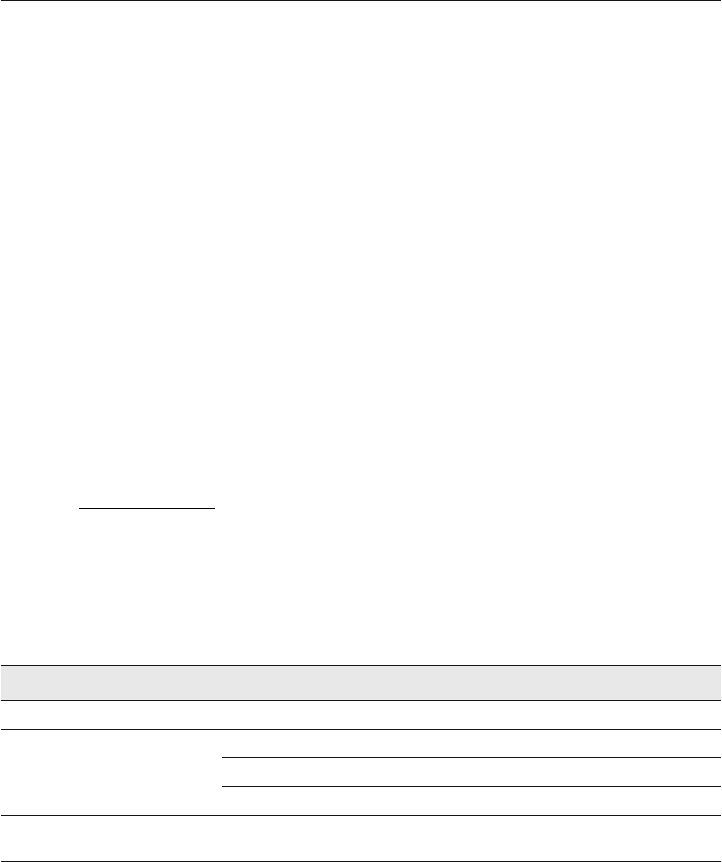
124 5 Crankcase and cylinder liners
5.5.4 Cylinders for four-stroke engines
New, more stringent exhaust regulations are forcing engine manufacturers to introduce the
four-stroke principle, even in small engines. Currently, various developments are underway
with the goal of providing designs that are high-revving, independent of orientation, and as
small and light as possible.
5.5.5 Bore coatings for light-alloy cylinders
Depending on the required service life and operational reliability, various running surface
coatings are available to the user of light-alloy cylinders. In any case, light-alloy cylinders
without or with thin bore coatings made of other metals are nearly equal in terms of heat dis-
sipation and weight as well as less expensive compared to cast iron cylinder liners.
Table 5.6 shows the ratings of light-alloy cylinders with various cylinder surface coatings in
comparison with gray cast iron cylinders. According to the relationship
W
o
o
T
T
Gray cast iron
Light metal
the temperatures at the base of the fin, near the combustion chamber floor, are compared
for gray cast iron and light-alloy cylinders.
Table 5.6: Ratings of various cylinder surface coatings, relative to gray cast iron cylinders
Cylinder Cylinder surface coating Rating of heat transfer T
Gray cast iron cylinder – 1
Light-alloy cylinder with
surface coating
NIKASIL
®
1.16 – 1.19
CROMAL
®
1.16 – 1.19
FE R R AL 1.16 – 1.19
Light-alloy cylinders without
reinforcement
– 1.17 – 1.2 0
The following coatings have been proven in day-to-day use:
NIKASIL
®
The running surface of light-alloy cylinders coated with NIKASIL
®
consists of a nickel disper-
sion, developed by MAHLE (Figure 5.28), which is about 0.05 mm thick in its finish-honed
state.
This galvanically applied nickel layer, with an even inclusion of hard silicon carbide particles
( < 2.5
μm edge length), results in a relatively “smooth” cylinder surface after honing.