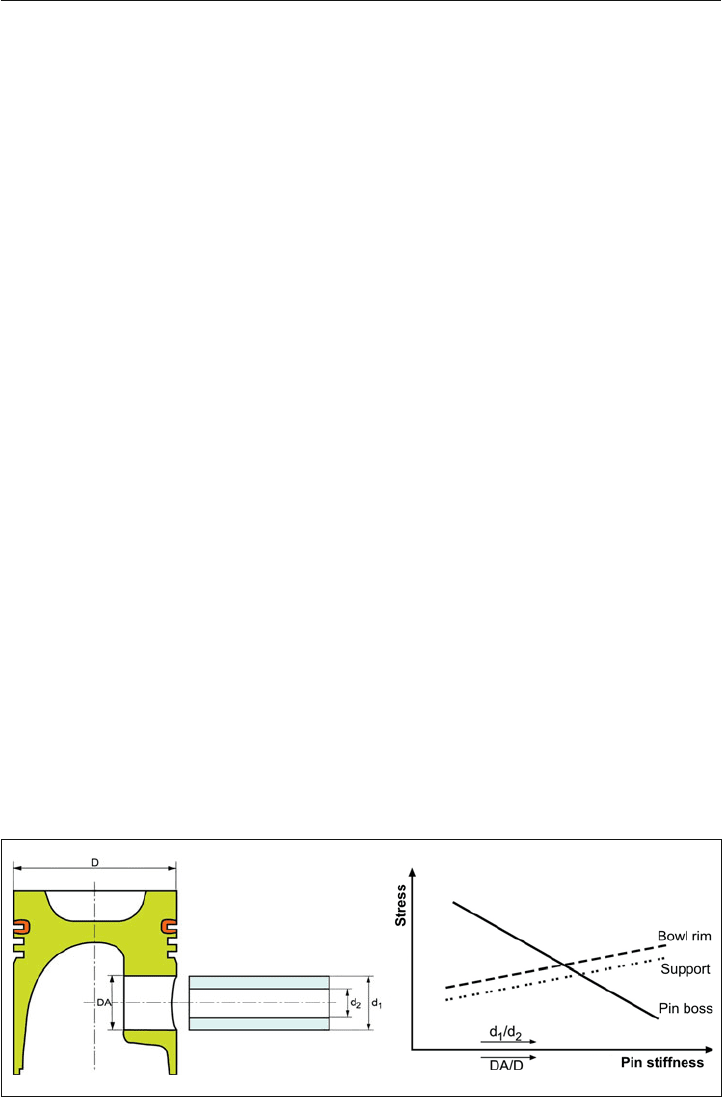
2.2 Requirements 31
The pin loads are evaluated using a fatigue strength map, e.g., according to Smith. Such a
fatigue strength map must be determined for each material in use. Its limit lines correspond
to the safety factor S = 1. The permissible minimum safety factor is determined according to
the requirements and expected loads for each area of application, such as passenger cars,
commercial vehicles, or motorsport.
Clearance between the piston pin and the pin boss or connecting rod small end should be
selected such that scuffing cannot occur between the contact areas with the piston and the
connecting rod. The clearance should be checked carefully, especially under warm operating
conditions, due to different thermal expansion coefficients of the materials used.
In order to avoid pin boss cracks, limits of the temperature-dependent material and load fac-
tors, such as surface pressure in the boss, must not be exceeded.
2.2.3 Deformation
Another requirement is that the piston pin must be light, in addition to having sufficient rigid-
ity and strength. Rigidity relative to bending can be increased greatly, as the fourth power
of the increase in diameter. Bending also increases approximately as the third power of the
support span of the piston pin, i.e., with the pin boss spacing. A reduction in this value thus
causes a significant reduction in bending and thus increases rigidity. If a shorter piston pin
can be used, then mass reduction is also possible.
An increase in rigidity relative to ovalization can be achieved only with a greater wall thick-
ness and thus always increases mass. The stiffness of the piston pin has a significant effect
on the loads on the pin bore, pin boss, support, and bowl rim, as shown in Figure 2.7.
The susceptibility of the piston to pin boss cracks is shown in Figure 2.8 as a function of
the piston pin geometry, as a result of engine testing. Due to higher peak cylinder pres-
Figure 2.7: Piston stress as a function of piston pin stiffness