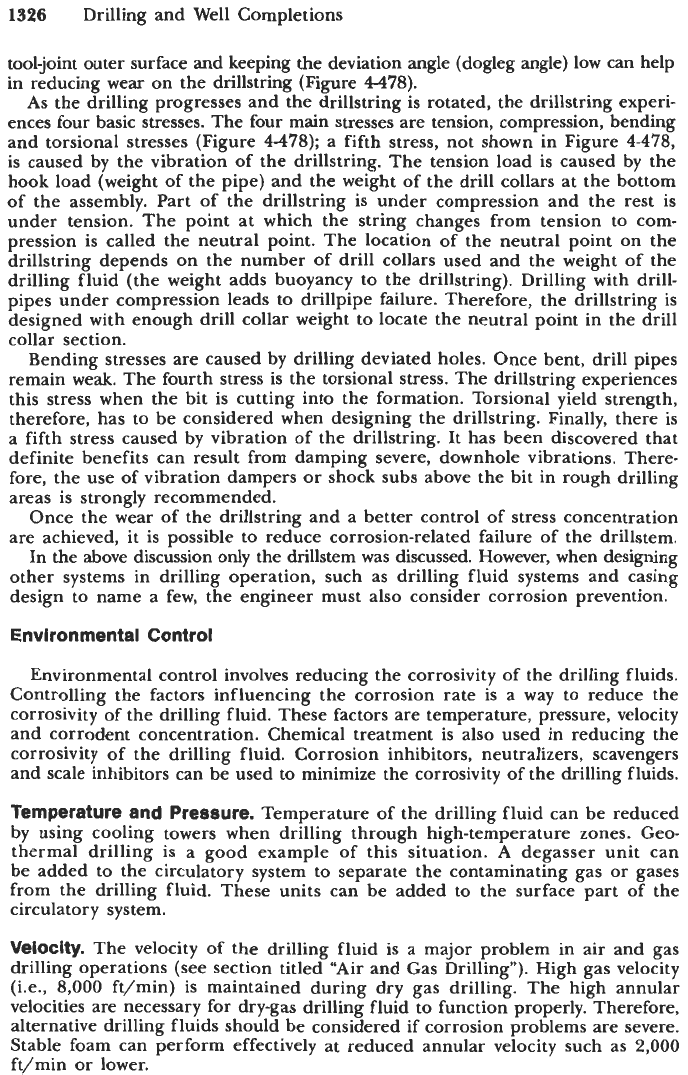
1326
Drilling and Well Completions
tool-joint outer surface and keeping the deviation angle (dogleg angle) low can help
in reducing wear on the drillstring (Figure
4478).
As
the drilling progresses and the drillstring is rotated, the drillstring experi-
ences four basic stresses. The four main stresses are tension, compression, bending
and torsional stresses (Figure
4-478);
a fifth stress, not shown in Figure
4-478,
is caused by the vibration of the drillstring. The tension load is caused by the
hook load (weight of the pipe) and the weight of the drill collars at the bottom
of the assembly. Part of the drillstring is under compression and the rest is
under tension. The point at which the string changes from tension to com-
pression is called the neutral point. The location
of
the neutral point on the
drillstring depends on the number of drill collars used and the weight of the
drilling fluid (the weight adds buoyancy to the drillstring). Drilling with drill-
pipes under compression leads to drillpipe failure. Therefore, the drillstring is
designed with enough drill collar weight to locate the neutral point in the drill
collar section.
Bending stresses are caused by drilling deviated holes. Once bent, drill pipes
remain weak. The fourth stress is the torsional stress. The drillstring experiences
this stress when the bit is cutting into the formation. Torsional yield strength,
therefore, has to be considered when designing the drillstring. Finally, there is
a fifth stress caused by vibration of the drillstring. It has been discovered that
definite benefits can result from damping severe, downhole vibrations. There-
fore, the use of vibration dampers
or
shock subs above the bit in rough drilling
areas is strongly recommended.
Once the wear of the drillstring and a better control of stress concentration
are achieved, it
is
possible to reduce corrosion-related failure
of
the drillstem.
In the above discussion
only
the drillstem
was
discussed. However, when designing
other systems in drilling operation, such as drilling fluid systems and casing
design to name a few, the engineer must also consider corrosion prevention.
Environmental Control
Environmental control involves reducing the corrosivity of the drilling fluids.
Controlling the factors influencing the corrosion rate is a way to reduce the
corrosivity of the drilling fluid. These factors are temperature, pressure, velocity
and corrodent concentration. Chemical treatment
is
also used in reducing the
corrosivity of the drilling fluid. Corrosion inhibitors, neutralizers, scavengers
and scale inhibitors can be used to minimize the corrosivity
of
the drilling fluids.
Temperature and Pressure.
Temperature of the drilling fluid can be reduced
by using cooling towers when drilling through high-temperature zones. Geo-
thermal drilling
is
a good example of this situation.
A
degasser unit can
be added
to
the circulatory system
to
separate the contaminating gas or gases
from the drilling fluid. These units can be added to the surface part of the
circulatory system.
Velocity.
The velocity of the drilling fluid
is
a major problem in air and gas
drilling operations (see section titled “Air and Gas Drilling”). High gas velocity
(i.e.,
8,000
ft/min) is maintained during dry gas drilling. The high annular
velocities are necessary for dry-gas drilling f hid
to
function properly. Therefore,
alternative drilling fluids should be considered if corrosion problems are severe.
Stable foam can perform effectively at reduced annular velocity such as
2,000
ft/min or lower.