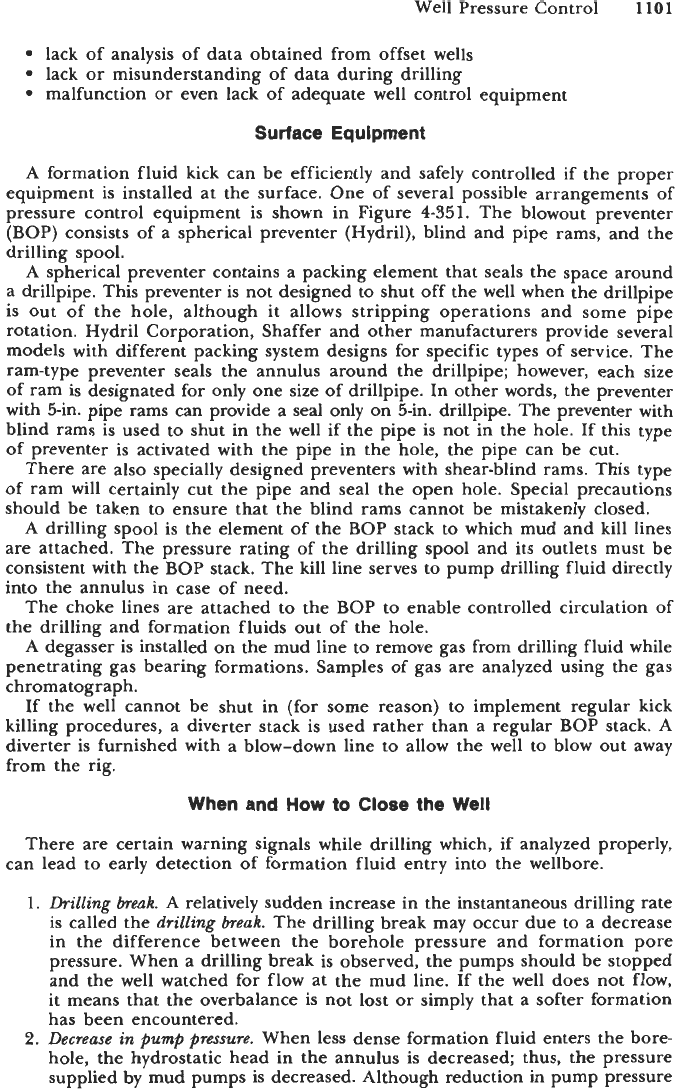
Well Pressure Control
1101
lack of analysis of data obtained from offset wells
lack
or
misunderstanding of data during drilling
malfunction
or
even lack of adequate well control equipment
Surface Equipment
A
formation fluid kick can be efficiently and safely controlled
if
the proper
equipment is installed at the surface. One of several possible arrangements of
pressure control equipment is shown in Figure 4-351. The blowout preventer
(BOP) consists of a spherical preventer (Hydril), blind and pipe rams, and the
drilling spool.
A
spherical preventer contains a packing element that seals the space around
a drillpipe. This preventer is not designed to shut off the well when the drillpipe
is out of the hole, although it allows stripping operations and some pipe
rotation. Hydril Corporation, Shaffer and other manufacturers provide several
models with different packing system designs for specific types of service. The
ram-type preventer seals the annulus around the drillpipe; however, each size
of ram is designated for only one size of drillpipe. In other words, the preventer
with
Sin. pipe rams
can
provide a seal
only
on 5-in. drillpipe. The preventer with
blind rams is used to shut in the well if the pipe is not in the hole. If this type
of preventer is activated with the pipe in the hole, the pipe can be cut.
There are also specially designed preventers with shear-blind rams. This type
of ram will certainly cut the pipe and seal the open hole. Special precautions
should be taken to ensure that the blind rams cannot be mistakenly closed.
A
drilling spool is the element
of
the BOP stack to which mud and kill lines
are attached. The pressure rating of the drilling spool and its outlets must be
consistent with the BOP stack. The kill line serves to pump drilling fluid directly
into the annulus in case of need.
The choke lines are attached to the BOP to enable controlled circulation of
the drilling
and
formation fluids out of the hole.
A
degasser is installed on the mud line to remove gas from drilling fluid while
penetrating gas bearing formations. Samples
of
gas are analyzed using the gas
chromatograph.
If the well cannot be shut in (for some reason) to implement regular kick
killing procedures, a diverter stack is used rather than a regular BOP stack.
A
diverter is furnished with a blow-down line to allow the well to blow out away
from the rig.
When and How
to
Close the Well
There are certain warning signals while drilling which, if analyzed properly,
can lead to early detection of formation fluid entry into the wellbore.
1.
Drilling
bwak.
A
relatively sudden increase in the instantaneous drilling rate
is
called the
drilling
break.
The drilling break may occur due to a decrease
in the difference between the borehole pressure and formation
pore
pressure. When a drilling break is observed, the pumps should be stopped
and the well watched for flow at the mud line. If the well does not flow,
it means that the overbalance is not lost or simply that
a
softer formation
has been encountered.
2.
Decrease
in
pump
pressure.
When less dense formation fluid enters the bore-
hole, the hydrostatic head in the annulus is decreased; thus, the pressure
supplied by mud pumps is decreased. Although reduction in pump pressure