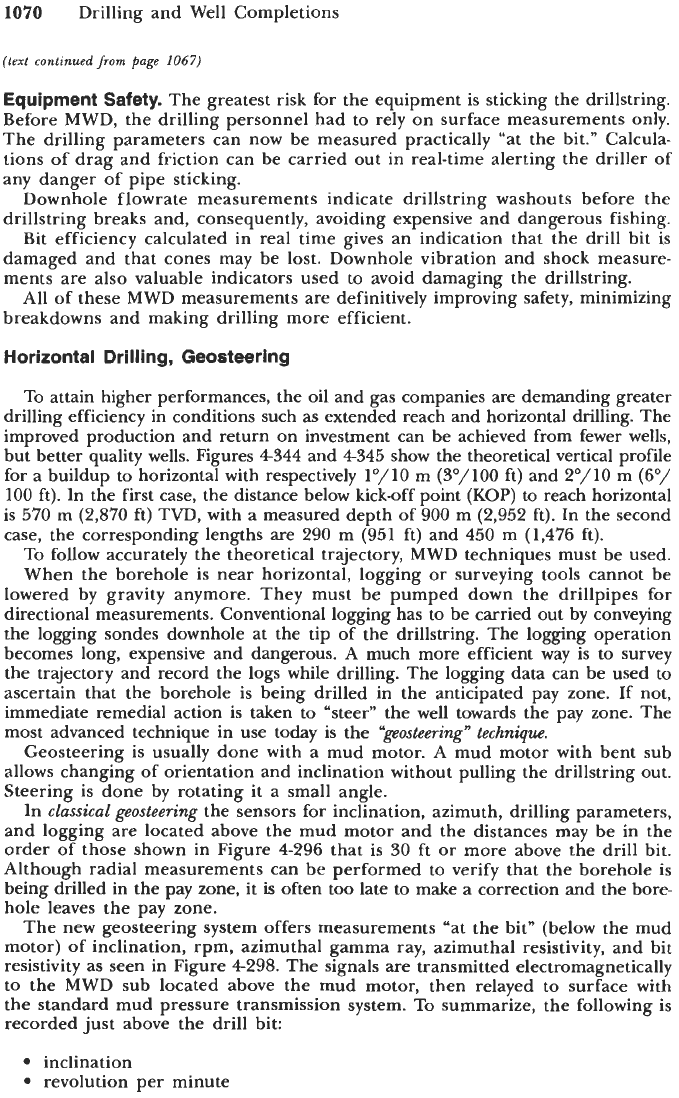
1070
Drilling and Well Completions
(text
continued
from
page
1067)
Equipment Safety.
The greatest risk for the equipment is sticking the drillstring.
Before MWD, the drilling personnel had to rely on surface measurements only.
The drilling parameters can now be measured practically “at the bit.” Calcula-
tions
of
drag and friction can be carried out in real-time alerting the driller
of
any danger of pipe sticking.
Downhole flowrate measurements indicate drillstring washouts before the
drillstring breaks and, consequently, avoiding expensive and dangerous fishing.
Bit efficiency calculated in real time gives an indication that the drill bit is
damaged and that cones may be lost. Downhole vibration and shock measure-
ments are also valuable indicators used to avoid damaging the drillstring.
All of these MWD measurements are definitively improving safety, minimizing
breakdowns and making drilling more efficient.
Horizontal Drilling, Geosteering
To
attain higher performances, the oil and gas companies are demanding greater
drilling efficiency in conditions such as extended reach and horizontal drilling. The
improved production and return on investment can be achieved from fewer wells,
but better quality wells. Figures
4344
and
4345
show the theoretical vertical profile
for a buildup to horizontal with respectively
lo/10
m
(3O/lOO
ft) and
2”/10
m
(So/
100
ft). In the first case, the distance below kick-off point
(KOP)
to reach horizontal
is
570
m
(2,870
ft)
TVD,
with
a
measured depth of
900
m
(2,952
ft). In the second
case, the corresponding lengths are
290
m
(951
ft)
and
450
m
(1,476
ft).
To follow accurately the theoretical trajectory, MWD techniques must be used.
When the borehole is near horizontal, logging
or
surveying tools cannot be
lowered by gravity anymore. They must be pumped down the drillpipes
for
directional measurements. Conventional logging has to be carried out by conveying
the logging sondes downhole at the tip of the drillstring. The logging operation
becomes long, expensive and dangerous. A much more efficient way is to survey
the trajectory and record the logs while drilling. The logging data can be used to
ascertain that the borehole is being drilled in the anticipated pay zone. If not,
immediate remedial action is taken to %teer” the well towards the pay zone. The
most advanced technique in use today is the
“geosteering” technique.
Geosteering is usually done with a mud motor.
A
mud motor with bent sub
allows changing of orientation and inclination without pulling the drillstring out.
Steering is done by rotating it a small angle.
In
classical geosteering
the sensors for inclination, azimuth, drilling parameters,
and logging are located above the mud motor and the distances may be in the
order of those shown in Figure
4-296
that is
30
ft or more above the drill bit.
Although radial measurements can be performed to verify that the borehole is
being drilled in the pay zone, it is often too late to make a correction and the bore-
hole leaves the pay zone.
The new geosteering system offers measurements “at the bit” (below the mud
motor) of inclination, rpm, azimuthal gamma ray, azimuthal resistivity, and bit
resistivity as seen in Figure
4298.
The signals are transmitted electromagnetically
to the MWD sub located above the mud motor, then relayed to surface with
the standard mud pressure transmission system. To summarize, the following is
recorded just above the drill bit:
inclination
revolution per minute