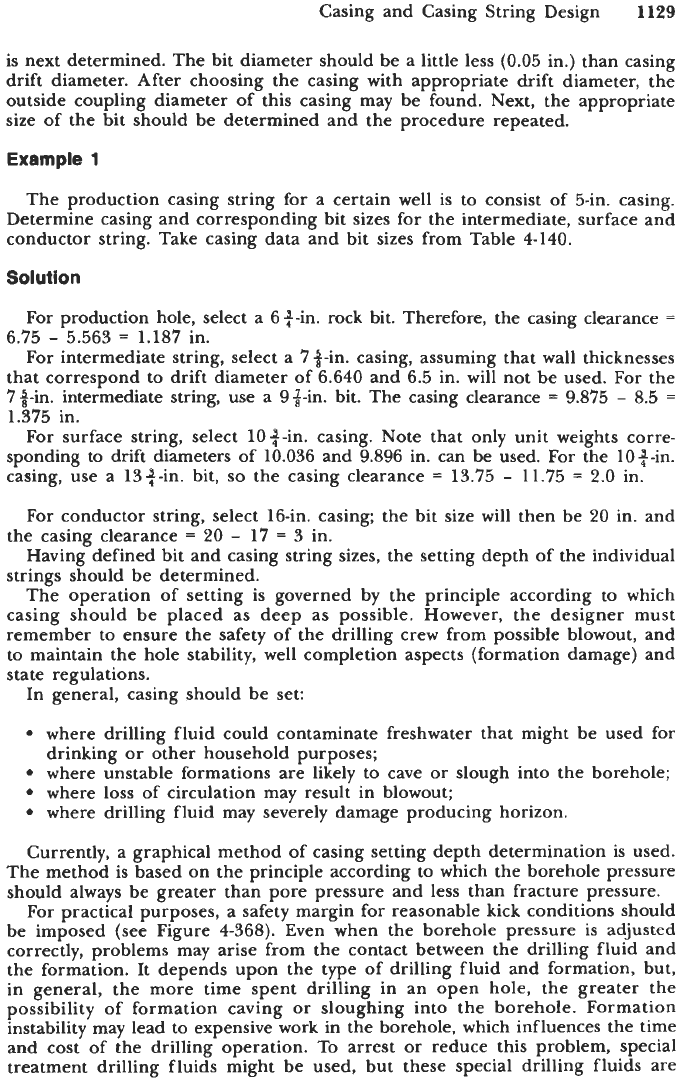
Casing and Casing String Design
1129
is next determined. The bit diameter should be a little less (0.05 in.) than casing
drift diameter. After choosing the casing with appropriate drift diameter, the
outside coupling diameter of this casing may be found. Next, the appropriate
size
of
the bit should be determined
and
the procedure repeated.
Example
1
The production casing string for a certain well is to consist of 5-in. casing.
Determine casing and corresponding bit sizes for the intermediate, surface and
conductor string. Take casing data and bit sizes from Table 4-140.
Solution
For production hole, select a 6+-in. rock bit. Therefore, the casing clearance
=
6.75
-
5.563
=
1.187 in.
For intermediate string, select
a
7 +-in. casing, assuming that wall thicknesses
that correspond to drift diameter of 6.640 and 6.5 in. will not be used.
For
the
73n. inteimediate string, use
a
9%-in. bit. The casing clearance
=
9.875
-
8.5
=
1.375 in.
For surface string, select lo*-in. casing. Note that only unit weights corre-
sponding to drift diameters of 10.036 and 9.896 in. can be used. For the loq-in.
casing, use a 13th. bit,
so
the casing clearance
=
13.75
-
11.75
=
2.0
in.
For
conductor string, select 16-in. casing; the bit size will then be
20
in. and
the casing clearance
=
20
-
17
=
3
in.
Having defined bit and casing string sizes, the setting depth of the individual
strings should be determined.
The operation of setting is governed
by
the principle according
to
which
casing should be placed as deep as possible. However, the designer must
remember
to
ensure the safety
of
the drilling crew from possible blowout, and
to maintain the hole stability, well completion aspects (formation damage) and
state regulations.
In general, casing should be set:
where drilling fluid could contaminate freshwater that might be used for
drinking
or
other household purposes;
where unstable formations
are
likely
to
cave
or
slough into the borehole;
9
where loss of circulation may result in blowout;
where drilling fluid may severely damage producing horizon.
Currently, a graphical method
of
casing setting depth determination is used.
The method is based on the principle according to which the borehole pressure
should always be greater than pore pressure and less than fracture pressure.
For practical purposes, a safety margin for reasonable kick conditions should
be imposed (see Figure 4-368). Even when the borehole pressure is adjusted
correctly, problems may arise from the contact between the drilling fluid and
the formation. It depends upon the type of drilling fluid and formation, but,
in general, the more time spent drilling in an open hole, the greater the
possibility of formation caving
or
sloughing into the borehole. Formation
instability may lead to expensive work in the borehole, which influences the time
and cost
of
the drilling operation. To arrest
or
reduce this problem, special
treatment drilling fluids might be used, but these special drilling fluids are