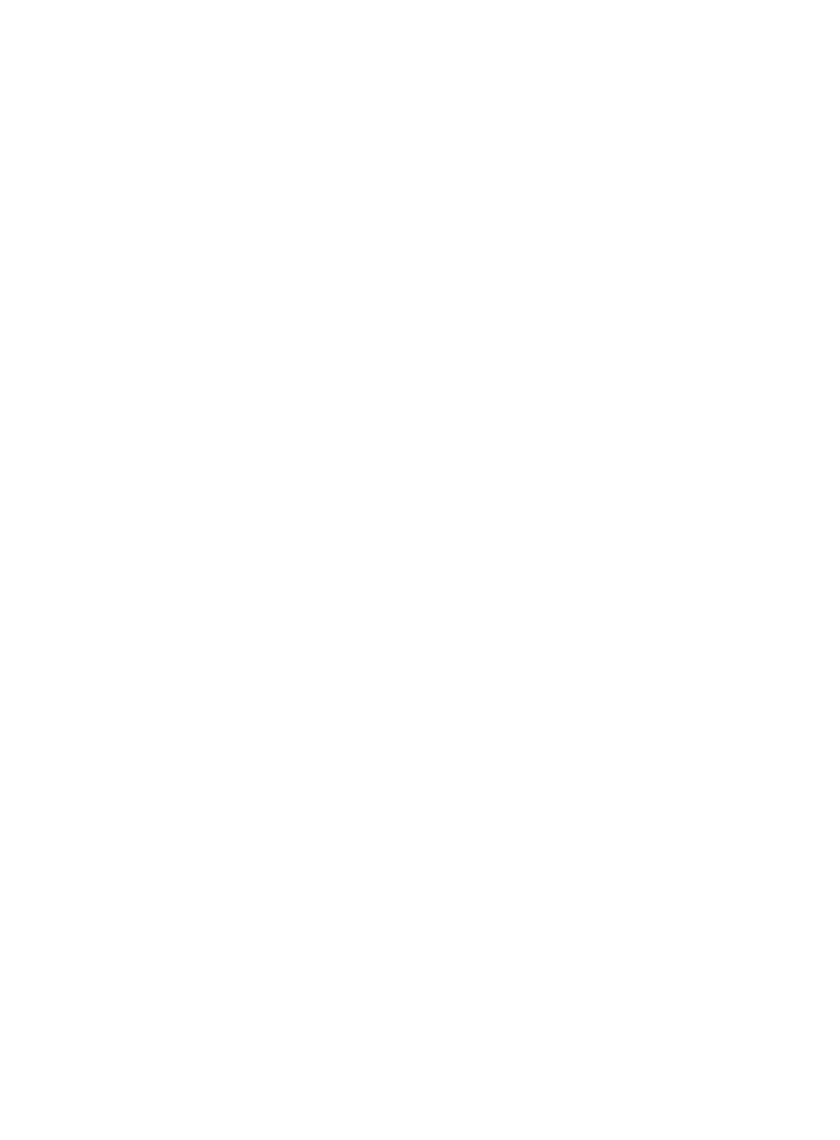
SILVER OXIDE BATTERIES 33.5
The mechanical strength of these cells is usually excellent. The electrodes are generally
strong and are fitted tightly into the containers. The cell containers are made of high-impact
plastics. Specific designs of these cells, when properly packaged, have met the high-shock,
vibration, and acceleration requirements of missiles and torpedoes with no degradation.
33.3.1 Silver Electrodes
The most common fabrication technique for silver electrodes is by sintering silver powder
onto a supporting silver grid. The electrodes are manufactured either in molds (as individual
plates or as master plates which are later cut to size) or by continuous rolling techniques.
They are then sintered in a furnace at approximately 700
⬚C.
Alternate techniques include dry processing and pressing, as well as slurry pasting with
a binder of AgO or Ag
2
O onto a grid. If pasted, the plates are often sintered, converting the
silver oxide into metallic silver and burning off the organic additives. The grid may be a
woven or expanded metal form of silver, or silver-plated copper.
After being cut to size and having wires or tabs hot-forged onto an appropriately coined
(compressed) area to carry current to the cell terminals, the electrodes are either electro-
formed (charged in tanks against inert counterelectrodes) before assembly into cells or as-
sembled into the cells in the metallic state and later charged in the cell.
Grid material, density, and thickness, electrical lead type and size; and final electrode
size, thickness, and density are all design variables which depend on the intended application
for the cells. The silver powder particle size may be varied, with the finer powders ap-
proaching the theoretical silver utilization of 2.0 g/ Ah. The use of very fine powder, however,
results in an initial voltage dip (typically less than 120 mS) at medium (C) to high discharge
rates.
33.3.2 Zinc Electrodes
Zinc electrodes are most widely made by dry pressing, by a slurry or paste method, or by
electrodeposition. In the dry-pressing method, a mixture of metallic zinc or zinc oxide,
binder, and additives is compressed around a metal grid; this is normally done in a mold.
The grid usually has the current-carrying leads prewelded in place. As the unformed powder
electrodes have little strength, one component of the separator system, the negative interse-
parator, is usually assembled around the electrode as part of the fabricating operation. Rolling
techniques have also been developed to permit continuous fabrication of dry-powder elec-
trodes.
6
In the paste or slurry method, a mixture of zinc oxide, binder, and additives is combined
with water and applied continuously to a carrier paper or directly to an appropriate metal
grid. Again, the negative interseparator is usually integral to provide needed physical
strength. After drying, multiple layers of these pasted slabs may be pressed together about
a pretabbed grid to form the final electrode. These plates may be assembled unformed into
the cell, or they may be electroformed in a tank against inert counterelectrodes.
Electrodeposited negative electrodes are manufactured by plating zinc in tanks onto me-
tallic grids. The plates must then be amalgamated and pressed or rolled to the desired thick-
ness and density, followed by drying.
The zinc electrode is acknowledged as the life-limiting component in both the silver-zinc
and the nickel-zinc systems. Accordingly, much work has been done in the area of additives
for these electrodes, both to reduce hydrogen evolution and to improve cycle life. The com-
mon additive to reduce hydrogen evolution has traditionally been mercury (1 to 4% of the
total mix), but this is being replaced, for personnel safety and enviromental reasons, by small