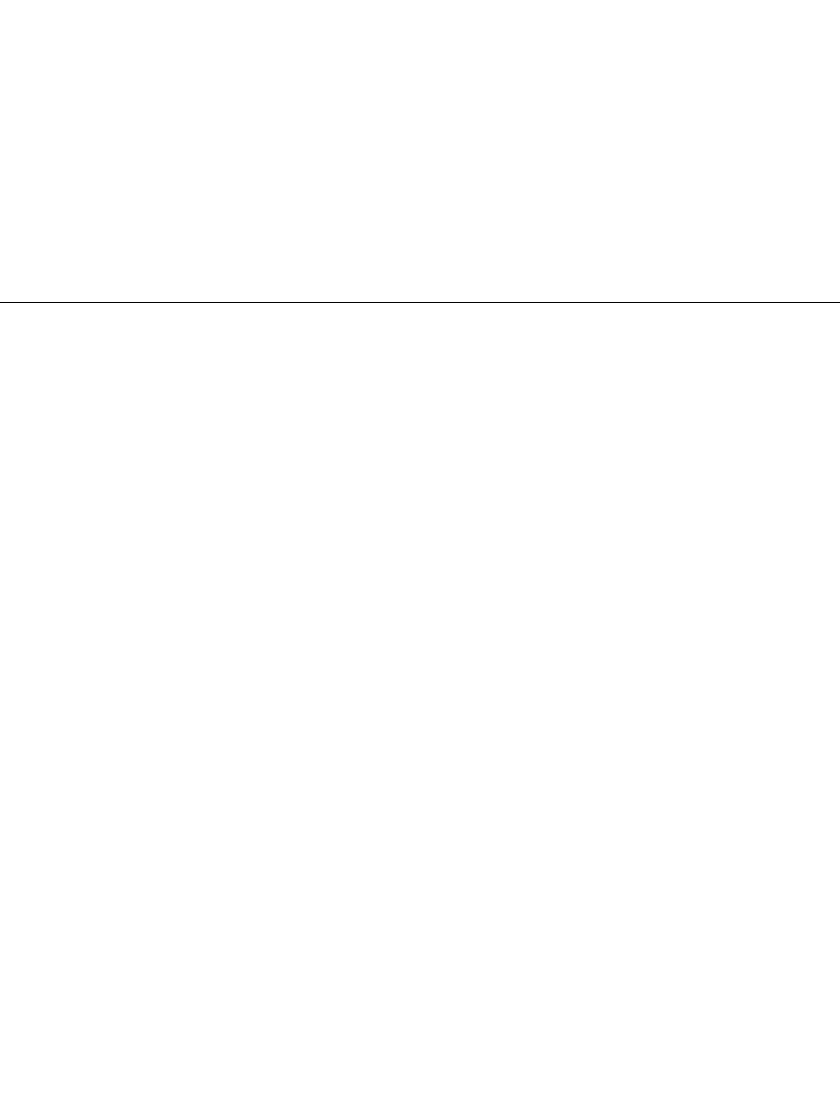
30.4 CHAPTER THIRTY
The electrolyte is also similar to small portable NiMH batteries, predominantly 6 Molar
KOHinH
2
O with a LiOH additive. Practically all NiMH batteries are sealed and use the
‘‘starved electrolyte’’ design, allowing for fast gas transport through the separator that is vital
for gas recombination. The separator itself is usually a highly porous permanently wettable
polypropylene, or it may be a polypropylene/ polyethylene composite made by either wet
laying of the fibers or by the ‘‘melt blown’’ process. In either case, the separator is usually
made wettable by a grafting process that bonds a material such as acrylic acid to the base
fibers by an energetic process such as radiation grafting. There are many variations within
the separators used by manufacturers and the processing details are proprietary.
30.4 CONSTRUCTION
30.4.1 Cylindrical Versus Prismatic Configuration
NiMH batteries are versatile in that both cylindrical and prismatic constructions can be
utilized. Each type of construction has advantages and disadvantages, and a particular end
use can determine which configuration is used. For NiMH applications below about 10 Ah,
cylindrical construction dominates due to low cost and high speed of manufacture. Above
20 Ah, cylindrical construction is extremely difficult and the prismatic configuration domi-
nates. In the 10 to 20 Ah cell size range, manufacturers are offering both cylindrical and
prismatic designs although prismatic designs are more common.
Cylindrical cells for industrial and propulsion applications are similar to high volume
production consumer batteries in that the well-known ‘‘jelly roll’’ construction is used. How-
ever, most small portable cylindrical cells require only low to moderate discharge rate ca-
pability and electrode terminal connections are usually quite simple. Conversely, since in-
dustrial and propulsion NiMH applications require high to ultra-high discharge rate capability
and low internal resistance, multiple tab current collection is used. This type of construction
is termed edge welding and requires each electrode to have a current collecting strip on one
side of the electrode. The current collecting strip for the positive and negative electrodes are
on opposite sides of the jellyroll. After coil winding of the jellyroll, the edge current collector
is welded in multiple locations to each electrode. Other aspects of cell assembly are virtually
identical to small consumer batteries. The net result of the enhanced current collection is a
reduction in cell specific energy and an increase in specific power due to decreased cell AC
impedance (usually around 8 to 12 m
⍀ for small portable batteries and around 1 to 2 m⍀
for industrial cylindrical cells). For industrial applications such as HEV, motorcycle and
electric bicycle applications, the most popular cylindrical cell sizes are standard C and D
sizes, although a multitude of height changes within those diameters are also used. Some
work on larger size cells such as the F size has also been reported.
5
Prismatic construction is conventional in that electrode stacks of alternating positive and
negative electrodes with intermediate separators are used (Fig. 30.2). The main design al-
ternatives involve the thickness and number of each electrode and the aspect ratio (relative
proportions of cell height to width to thickness). Key design variations include the ratio of
active materials to inactive components such as the cell can and terminal, and current col-
lectors. In all cases, the cell designer has the objective of emphasizing one or more properties
of performance such as energy vs. power, while maintaining a minimum threshold of other
performance factors such as cycle life. One example is that for EV NiMH prismatic cells,
6
a specific power of about 200 W/kg is acceptable for most vehicles and consequently,
relatively thick positive and negative electrodes can be used to increase the ratio of active
material to inactive cell components, allowing specific energy in the 63 to 80 Wh /kg range.
Alternately, HEV prismatic NiMH batteries typically must deliver greater than 500 W /kg
specific power and therefore electrode thickness must be lower than that for EV use. NiMH
batteries for HEV use have a typical specific energy ranging from about 42 to 68 Wh /kg.