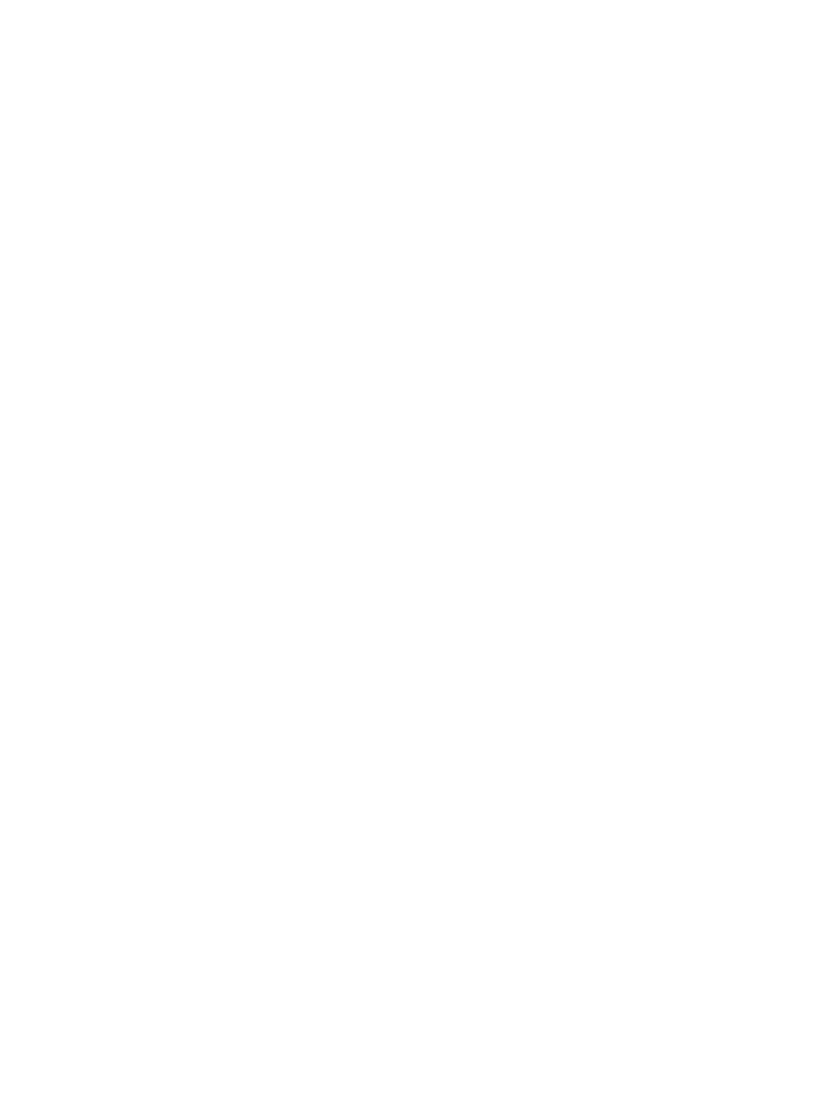
PROPULSION AND INDUSTRIAL NICKEL-METAL HYDRIDE BATTERIES 30.11
30.4.6 Nickel Hydroxide
Nickel hydroxide for use in NiMH batteries is fundamentally the same as that used in nickel
cadmium and nickel-iron batteries, and from a simple viewpoint, the basic compound is the
same as that used by Thomas Edison 100 years ago. Today’s high performance nickel hy-
droxide is much more complicated and continues to improve in capacity and utilization,
power and discharge rate capability, cycle life, high temperature charging efficiency, simpli-
fied manufacturing processes and cost.
As mentioned previously, one type of nickel hydroxide is by far the most common—a
high density spherical type for use in pasted electrodes which became commercial around
1990.
23,24
High density spherical nickel hydroxide is made in a precipitation process where
metal salts such as nickel sulfate are reacted with caustic such as NaOH in the presence of
ammonia. The nickel source may have additives such as cobalt and zinc to enhance per-
formance. The important physical parameters within this type of nickel hydroxide are:
•
Chemical formula. Common compositions are Ni
94
Co
3
Zn
3
(wt%) where cobalt is copre-
cipitated for the purpose of conductivity enhancement and both cobalt and zinc have the
function of oxygen overvoltage adjustment and microstructure refinement.
•
Tap density. Usually around 2.2 g/ cc, tap density is a measure of the dry nickel hydroxide
powder packing efficiency and influences the amount of active material which can be
loaded into the pores of the nickel foam current collector.
•
Particle size, usually having an average particle size of about 10 microns.
•
Surface area. Measured by the BET method, surface area refers not to the geometric area
of each nickel hydroxide sphere, but rather to the total surface area of each particle which
contribute to the charge/ discharge reactions and can thus affect utilization and high rate
discharge capability. A typical BET surface area for high-density spherical nickel hydrox-
ide is about 10 m
2
/g.
•
Crystallinity. Each nickel hydroxide sphere has an extremely high surface area correspond-
ing to the nickel hydroxide crystallites themselves. Crystallinity is measured by X-ray
diffraction, where the full width at half maximum (FWHM) of a reflection such as the
⬍101⬎ plane may yield a typical crystallite size of about 110 angstroms.
A variety of other factors contribute to performance, including impurities from processing
such as residual sulfates, nitrates, sodium sulfate, etc.
The nickel hydroxide active material and electrode formula can be formulated for specific
applications. For operation at 65
⬚C, some manufacturers may add Ca(OH)
2
, CaF
2
,orY
2
O
3
to the paste formula to inhibit premature oxygen evolution on charge.
25
Other paste formula
modifications may be an adjustment in the type and quantity of conductive network additives
such as cobalt metal and cobalt monoxide.
26,27,28
When long-term storage over several years
is required, it is common to increase the levels of cobalt additives to combat breakdown of
the conductive network and isolation of the active material. For ultra-high power discharge,
it is also possible to add metallic nickel fibers to the paste formula to enhance conductivity.
In the case of calcium additives, the additive may cause a loss in power and/ or cycle life.
Cobalt metal and cobalt monoxide are relatively expensive materials, and increased use has
cost implications. Addition of metallic nickel fibers lowers the amount of active material
and consequently capacity and specific energy are reduced.
The nickel hydroxide active material itself is most commonly a NiCoZn triprecipitate.
However, the amounts of cobalt and zinc which are usually about 1 to 5% each can be
adjusted for conductivity and oxygen overvoltage with some tradeoffs in terms of active
material capacity and cost. Other more complicated multi-element precipitates such as
NiCoZnCaMg offer higher capacity, cycle life and high temperature performance, but cannot
be manufactured by conventional precipitation processes. Another common active material
choice is ‘‘cobalt-coated nickel hydroxide.’’ Usually, the paste additives are finely divided