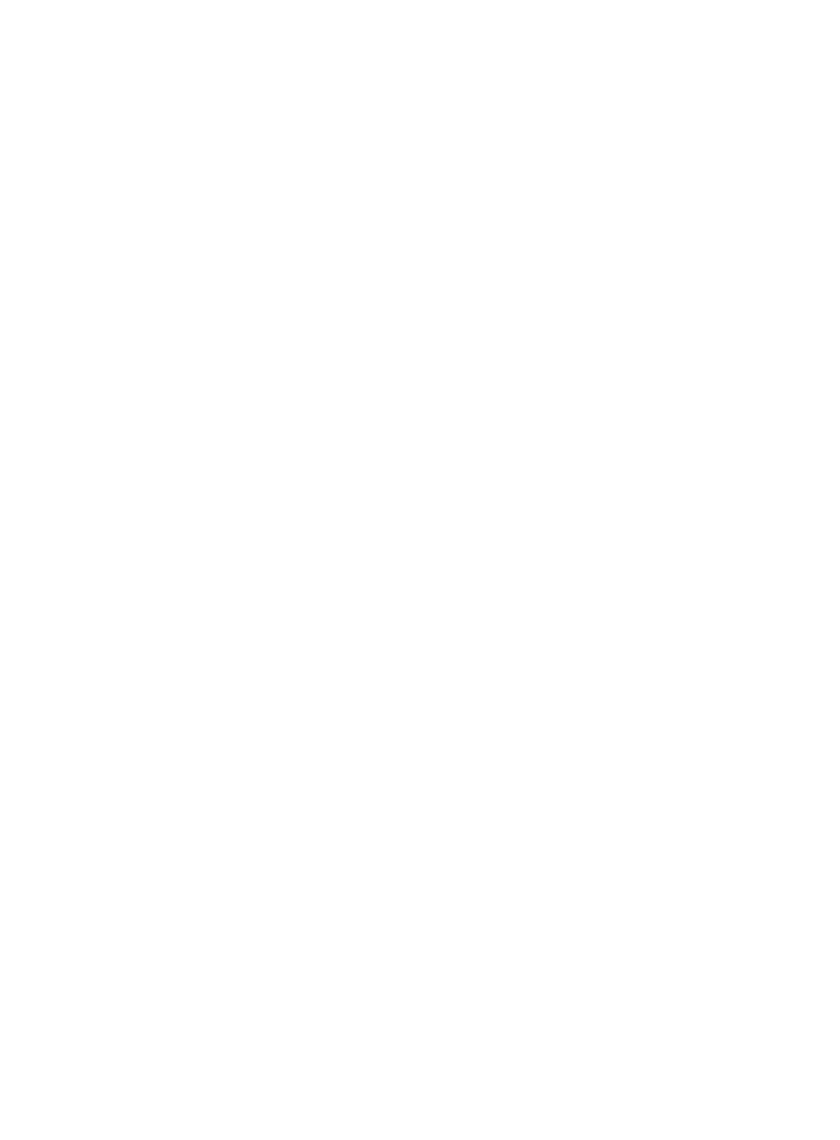
30.26 CHAPTER THIRTY
30.9.5 Cycle Life
Cycle life for industrial NiMH batteries has both similarities and differences to those of
small portable NiMH batteries. Cycle life for small portable NiMH batteries can vary from
manufacturer to manufacturer, but usually falls in the range of 500 to 1000 cycles (100%
DOD under 2 hour charge/ discharge). Design and chemistry factors affecting cycle life that
are common to both large and small NiMH batteries include:
1. Metal hydride electrode
•
Alloy formula (oxidation /corrosion properties)
•
Alloy processing effect on microstructure (particle disintegration)
•
Electrode construction (swelling in x-y-z direction, stability of conduction pathways)
2. Nickel hydroxide electrode
•
Active material formula (swelling and poisoning resistance)
•
Conductive network stability (amount and type of cobalt oxides)
•
Substrate (pore size, strength and resistance to fracture)
3. Cell design
•
N/ P ratio (amount of excess negative electrode capacity to influence cell pressure, MH
corrosion, disintegration)
•
MH discharge reserve (overdischarge protection)
•
Separator (stability to corrosion, electrolyte absorption and retention, thickness and re-
sistance to short circuit)
•
Electrolyte (composition, amount, and fill fraction)
•
Vent pressure (weight loss, charge imbalance)
•
Electrode stack design (compression, electrode thickness, aspect ratio of height to
width)
Factors affecting cycle life which are different from small portable applications for large
industrial NiMH applications include:
•
Significantly higher typical battery voltages (42 to 320 V vs. 12 V) increases risk of abusive
overcharge and overdischarge due to capacity or state-of-charge mismatch.
•
Overall higher energy (0.1 kWh vs. 33 kWh) increases heat generation and criticality of
thermal management, which can be further influenced by battery pack enclosure heat trans-
fer limitations.
•
Typically higher operating temperature. Air cooled and water cooled vehicle batteries are
usually operating at a temperature of 35
⬚C or higher whereas operating temperatures for
small portable batteries may experience transient high temperatures, but on average are at
or near room temperature.
•
Series/ parallel strings. In small portable batteries, there are a large number of cell sizes
available, ranging from 100 mAh button cells to 7 to 12 Ah D and F cells. There are many
fewer cell sizes for HEV and EV NiMH batteries. Consequently, vehicle applications may
be required to use series /parallel combinations of NiMH cells to meet the required pack
voltage and energy demands, and thereby increase the risk of pack imbalances.
•
End of life definition for small portable batteries is usually based on capacity loss. In
contrast, NiMH for EV and HEV applications find end of life is due to power limitations.
•
Qualification and operation testing. The emphasis on power greatly influences testing and
methodology. In small portable battery cycle life testing, it is most common to use 1 or 2
hour constant current charge and discharge, usually to 100% DOD each cycle. For EV
cycle life testing, discharge is usually a variable current /time profile to simulate driving
conditions—the so-called DST driving profile. The significance of pulsed discharge cycle
life testing is that the high current pulse dominates the test. On the other hand, most EV