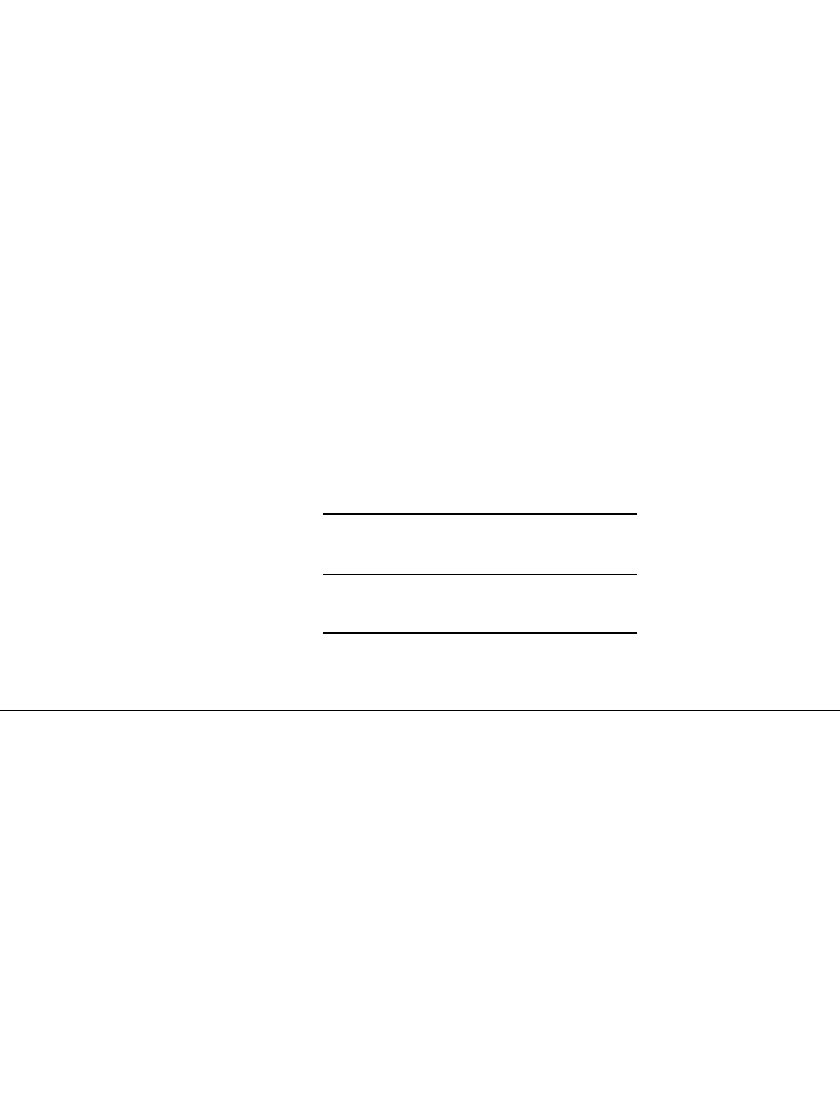
29.4 CHAPTER TWENTY-NINE
In the case of the AB
2
class of alloys, substitutions have improved the alloy as follows:
3
1. V, Ti, and Zr improve hydrogen storage.
2. Ni and Cr are major constituents which suppress corrosion and provide longer cycle life.
3. Al, Ti, Zr and Si are minor constituents which also suppress corrosion and provide longer
cycle life.
The AB
2
alloy has a higher capacity per unit weight and volume over a moderate oper-
ating range of temperature and discharge rate than the AB
5
alloy as shown in Table 29.2.
However, over a very broad and demanding operating range of temperature and discharge
rate, the lower capacity AB
5
alloys are favored. AB
5
alloys have advantages and better
performance
4
under a number of conditions, including high discharge rates, high rate charge
acceptance, low and high discharge temperatures and superior high temperature stability.
4
To
compensate for some of these advantages of the batteries made with AB
5
alloy, batteries
made with the AB
2
alloy have been constructed with larger conductors, more surface area
and electrolyte, leaving less room for the active material. As a result, the overall energy
density of batteries made with AB
2
alloy may actually be the same or even lower than those
made with AB
5
alloy. Therefore, the use of the AB
5
alloy dominates in portable sealed nickel-
metal hydride batteries because of their overall advantages. (See discussion of metal hydride
alloys in Chap. 30.)
TABLE 29.2 Comparison of Metal Hydride
Alloys—Electrochemical Equivalents
Alloy
Gravimetric
Ah/kg
Volumetric
Ah/L
AB
5
AB
2
270–290
360–400
2200–2400
2500–2800
29.3 CONSTRUCTION
Sealed nickel-metal hydride cells and batteries are constructed in cylindrical, button, and
prismatic configurations, similar to those used for the sealed nickel-cadmium battery.
The electrodes are designed with highly porous structures having a large surface area to
provide a low internal resistance and a capability for high-rate performance. The positive
electrode in the cylindrical nickel-metal hydride cell is a highly porous sintered, or felt nickel
substrate into which the nickel compounds are impregnated or pasted and converted into the
active material by electrodeposition. Felts and foams have generally replaced sintered plaque
electrodes. Expanded metals and perforated sheets are cheaper, but they have poor high rate
capability. Sintered structures are much more expensive. The negative electrode, similarly,
is a highly porous structure using a perforated nickel foil or grid onto which the plastic-
bonded active hydrogen storage alloy is coated. The electrodes are separated with a synthetic
nonwoven material, which serves as an insulator between the two electrodes and as a medium
for absorbing the electrolyte.
29.3.1 Cylindrical Configuration
The assembly of the cylindrical unit is shown in Fig. 29.2a. The electrodes are spirally
wound and the assembly is inserted into a cylindrical nickel-plated steel can. The electrolyte
is added and contained within the pores of the electrodes and separator.