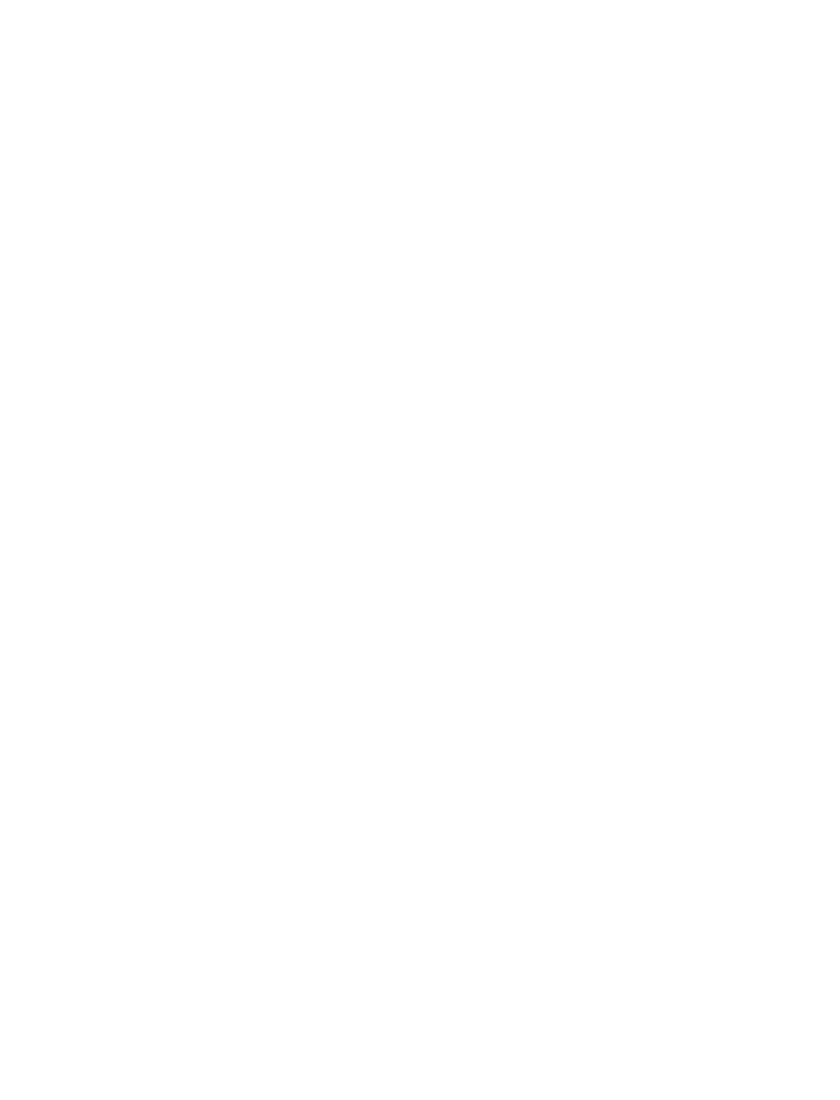
RECHARGEABLE LITHIUM BATTERIES (AMBIENT TEMPERATURE) 34.45
The solid polymer electrolyte technology provides flexibility in battery design as the cell
can be fabricated in a variety of shapes, configurations, and sizes. The estimated specific
energy and the energy density are very attractive. Major interest is in using this battery
system for applications requiring high voltages and capacity such as electric and hybrid
electric vehicles and for stand-by power applications such as large uninterruptible power
supplies.
34.4.5 Inorganic Electrolyte Batteries
Since the introduction of lithium/SO
2
primary batteries, significant research efforts have been
directed to the development of rechargeable lithium /SO
2
batteries. Among the different elec-
trolyte salts investigated, LiAlCl
4
, LiGaCl
4
, and Li
2
B
10
Cl
10
are noteworthy because of their
good ionic conductivity and lithium cycling efficiency. High-surface-area carbon such as
Ketjen black
11,19,57–61
or CuCl
2
26,60,62,63
are used as cathode materials. Microporous Tefzel
separator was found to be compatible in these electrolytes. This material is no longer avail-
able commercially, however.
Inorganic electrolyte batteries offer several advantages, including high-rate capability, ex-
cellent shelf life, and the ability to accept limited overcharge through a shuttle mechanism.
The major disadvantages of these batteries are safety issues, capacity fade on cycling,
significantly low capacity at low temperature, and high toxicity of electrolytes.
Lithium/ Carbon Batteries. These batteries are made in an hermetically sealed stainless-
steel container with a metallic lithium anode, a Ketjen black carbon cathode, and a
LiAlCl
4
䡠 6SO
2
electrolyte. The cathode composition is 96% Ketjen black and 4% Teflon.
58
Teflon-rich carbon-coated nickel exmet is used as the cathode substrate. These batteries are
made cathode-limited with the anode capacity at least twice the cathode capacity. Batteries
are vacuum filled with the electrolyte. The open-circuit voltage of the system is about 3.3
V. The average discharge voltage is 3.1 V at 1 mA/ cm
2
. It is believed that high-surface-area
carbon forms a complex with the electrolyte, and this complex takes part in the cell reaction.
Typical discharge-charge curves of lithium/carbon batteries of 3 Ah capacity using a
LiAlCl
4
䡠 6SO
2
electrolyte are shown in Fig. 34.32a for selected cycles. The change in voltage
with time for the cell and the cathode versus the lithium reference are almost identical,
indicating little anode polarization at the 1 mA/ cm
2
discharge and charge rate. The gradual
loss of capacity and the increased charge plateau on cycling are related to cathode polari-
zation. Scanning electron microscopy and X-ray diffraction analyses of discharged cathodes
confirm that the polarization is caused by irreversible deposition of a nonconductive dis-
charge product (LiCl).
The lithium /carbon system in SO
2
-based LiAlCl
4
electrolyte has excellent shelf life (⬍1%
capacity loss per month) and insignificant voltage delay, even after 3 years of storage at
room temperature.
59
The cell delivers significantly lower capacity at low temperature. Figure
34.32c shows the discharge characteristics of a lithium/carbon cell at
⫺20⬚C. The system is
particularly suitable for high-rate pulse power applications. Figure 34.32b shows the pulse
discharge behavior of a lithium/carbon battery in LiAlCl
4
䡠 6SO
2
at 20 mA/ cm
2
.
61
Lithium/ Copper Chloride Battery. In this system, the copper chloride cathode is directly
reduced and oxidized and no lithium intercalation-deintercalation occurs during the dis-
charge-charge process. The use of CuCl
2
as the active cathode material provides a higher
discharge voltage (3.3 V) for the reduction of Cu
2
⫹
to Cu
⫹
. Figure 34.33 shows the discharge-
charge behavior of a prismatic D-size Li /CuCl
2
battery at 1 mA /cm
2
. If the discharge is
limited to a single-electron process, high cycle life (
⬎200) with good capacity (0.9e /CuCl
2
)
can be achieved. This system shows excellent coulombic efficiency (see Fig. 34.33b).