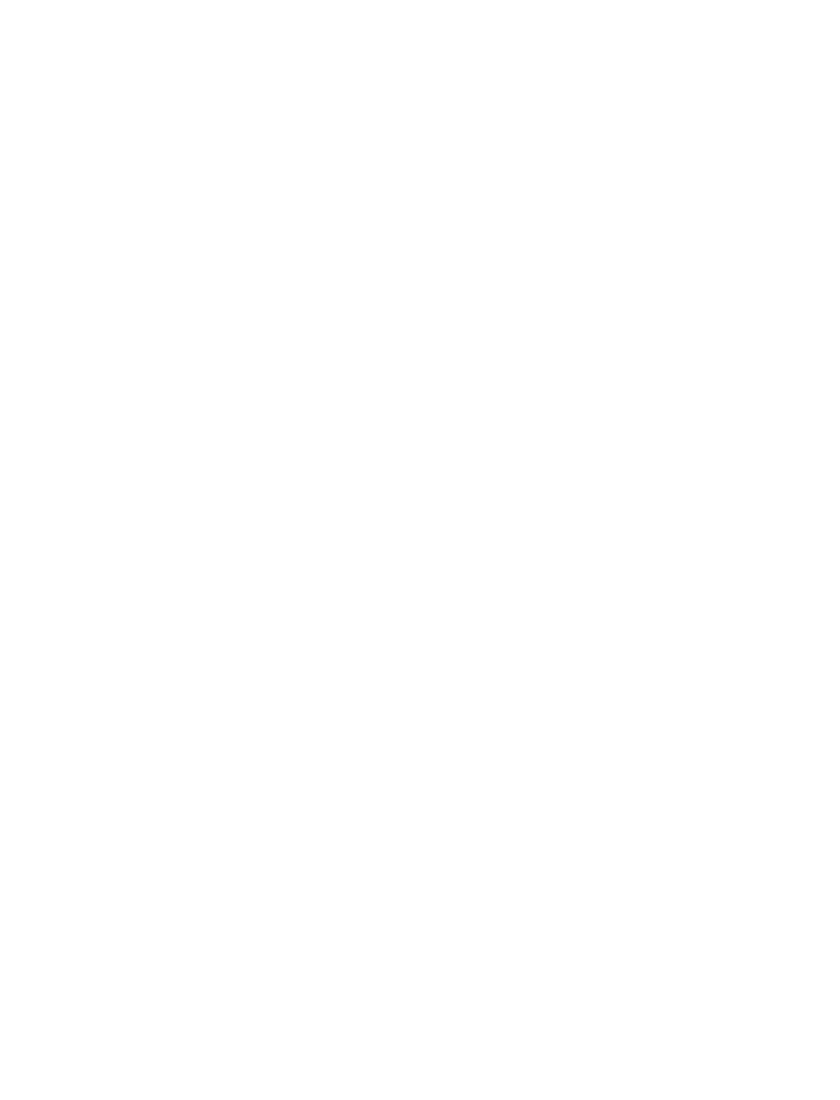
RECHARGEABLE LITHIUM BATTERIES (AMBIENT TEMPERATURE) 34.37
polymer component may be gelled by the addition of low molecular weight (liquid) solvents
to enhance its ionic conductivity. Such a battery system shows two major advantages with
respect to standard batteries that use inert porous separators:
1. The electrode and electrolyte layers are laminated (usually by heating and pressing the
layers), thus allowing various battery shapes without loss of contact.
2. Even if a low molecular weight (liquid) plasticizer is added to obtain high conductivity
at ambient and sub-ambient temperatures, there is no free liquid present in the battery
thus preventing any leakage problems.
Examples of the battery systems under development or available on the marketplace are
indicated in Table 34.16. They can be conveniently classified into three categories:
1. Positive and negative intercalation electrodes (lithium-ion) with a gelled polymer electro-
lyte (PEO-based).
2. Positive and negative intercalation electrodes (lithium-ion) with a porous polymer sepa-
rator layer filled with a liquid electrolyte (PVDF-based).
3. Positive intercalation electrode-lithium anode (lithium-metal) with a dry polymer electro-
lyte layer.
The first and the second categories, the latter of which (PVDF-based systems) does not
properly belong to the class of polymer electrolyte batteries, are covered in Chap. 35. In this
chapter, the attention is focused on the lithium metal, dry polymer electrolyte systems.
The search for high energy density batteries, especially for electric vehicle applications,
has led to the consideration of the use of lithium metal anodes. No other anode can attain
the same electrochemical performance in terms of specific energy as metallic lithium. How-
ever, safety issues as well as poor cycle life performance have prevented the commercial
success of lithium-metal batteries with the exception of primary batteries. At the present
time, there are three major programs aimed at the development of lithium-anode, dry-polymer
electrolyte batteries for electric vehicles (Table 34.17). Within these R&D programs, sub-
stantial successes have been obtained in terms of cyclability of the lithium-polymer electro-
lyte interface
51
as well as the whole battery system.
50
However, Argotech’s battery NPS-
24V80 (Table 34.18) appears to be the only system close to commercialization. This battery,
designed for telecommunication applications (especially for outside plants), is a fall-out of
the EV battery module developed within the USABC program.
Figure 34.21 illustrates the internal design of the lithium polymer cell. The cell is made
by laminating five thin layers including an insulating layer, a lithium foil anode, a solid
polymeric electrolyte, a transition metal oxide cathode (VO
x
) and a current collector. The
unit cell is made by winding the laminated film into a jelly roll (as in Fig. 34.21) or a flat
roll (preferred for multiple cell battery assembly) structure. These cells are then assembled
in series and in parallel arrangements to form modules of different sizes and shapes for
numerous applications. As an example, Fig. 34.22 illustrates the design of a lithium-polymer
battery module for electric vehicle applications. Unit laminated cells are packaged into a
stack of flat cells to create a module. The cells can be connected in parallel and /or series
arrays within a single container to build the desired module capacity and voltage. The pack-
aging also provides the mechanical, electrical, and thermal controls required for operation.
Each module is a fully functional battery system, including intelligent control and monitoring
electronics that interface with the battery pack controller.