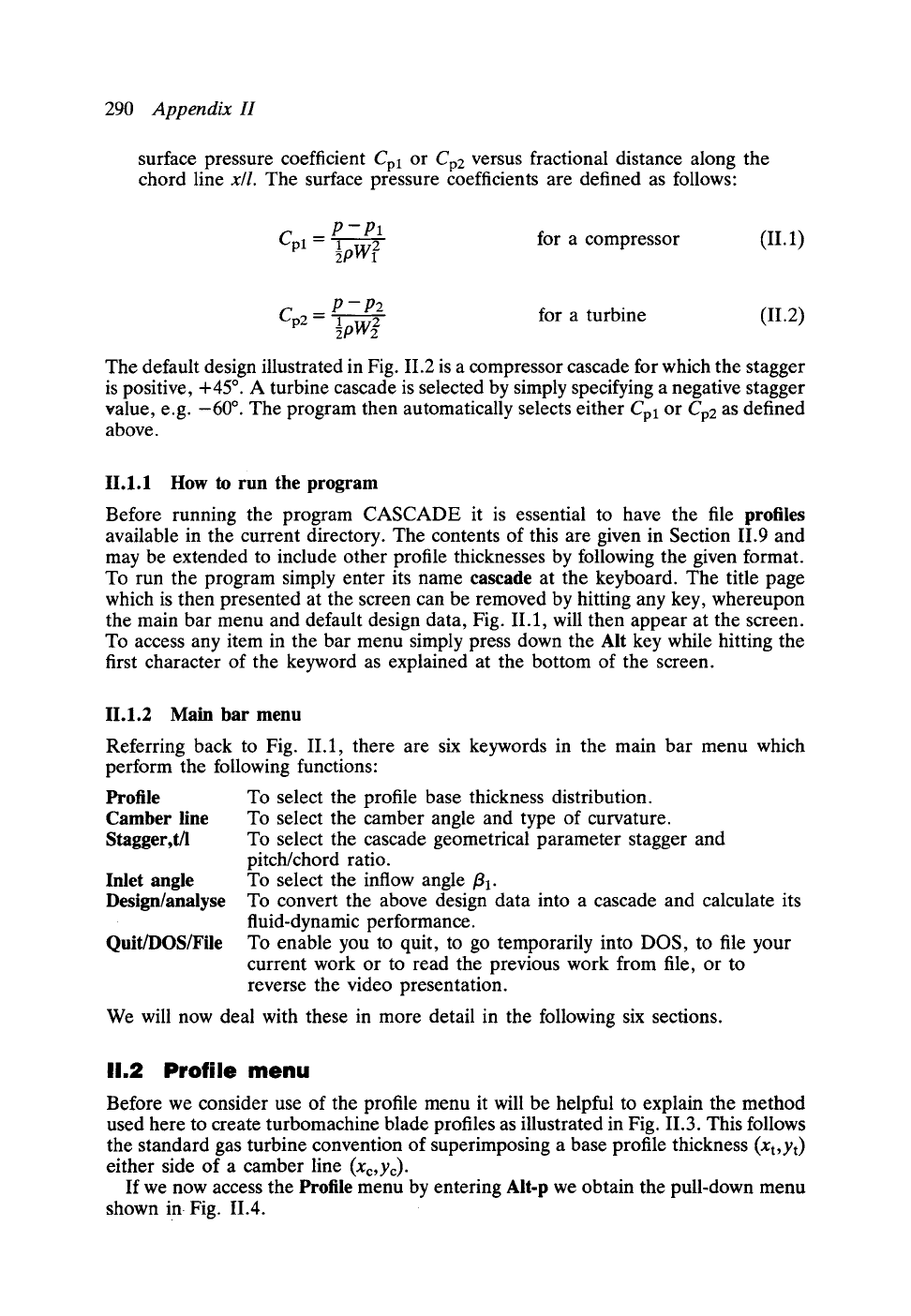
290
Appendix H
surface pressure coefficient
Cpl or
Cp2 versus fractional distance along the
chord line
x/l.
The surface pressure coefficients are defined as follows:
' P
-Pl
Up1 --
1 2 for a compressor (II. 1)
~pW1
Cp2 = Pl - P22 for a turbine (11.2)
~pW~
The default design illustrated in Fig. 11.2 is a compressor cascade for which the stagger
is positive, +45 ~ A turbine cascade is selected by simply specifying a negative stagger
value, e.g. -60 ~ The program then automatically selects either Cpl or Cp2 as defined
above.
II.1.1 How to run the program
Before running the program CASCADE it is essential to have the file
profiles
available in the current directory. The contents of this are given in Section 11.9 and
may be extended to include other profile thicknesses by following the given format.
To run the program simply enter its name cascade at the keyboard. The title page
which is then presented at the screen can be removed by hitting any key, whereupon
the main bar menu and default design data, Fig. II.1, will then appear at the screen.
To access any item in the bar menu simply press down the Alt key while hitting the
first character of the keyword as explained at the bottom of the screen.
11.1.2 Main bar menu
Referring back to Fig. II.1, there are six keywords in the main bar menu which
perform the following functions:
Profile To select the profile base thickness distribution.
Camber line
To select the camber angle and type of curvature.
Stagger, t/l To select the cascade geometrical parameter stagger and
pitch/chord ratio.
Inlet
angle To select the inflow angle/31.
Design/analyse To convert the above design data into a cascade and calculate its
fluid-dynamic performance.
Quit/DOS/File To enable you to quit, to go temporarily into DOS, to file your
current work or to read the previous work from file, or to
reverse the video presentation.
We will now deal with these in more detail in the following six sections.
11.2 Profile menu
Before we consider use of the profile menu it will be helpful to explain the method
used here to create turbomachine blade profiles as illustrated in Fig. 11.3. This follows
the standard gas turbine convention of superimposing a base profile thickness
(xt,Yt)
either side of a camber line (xe,yc).
If we now access the Profile menu by entering Alt-p we obtain the pull-down menu
shown in Fig. 11.4.