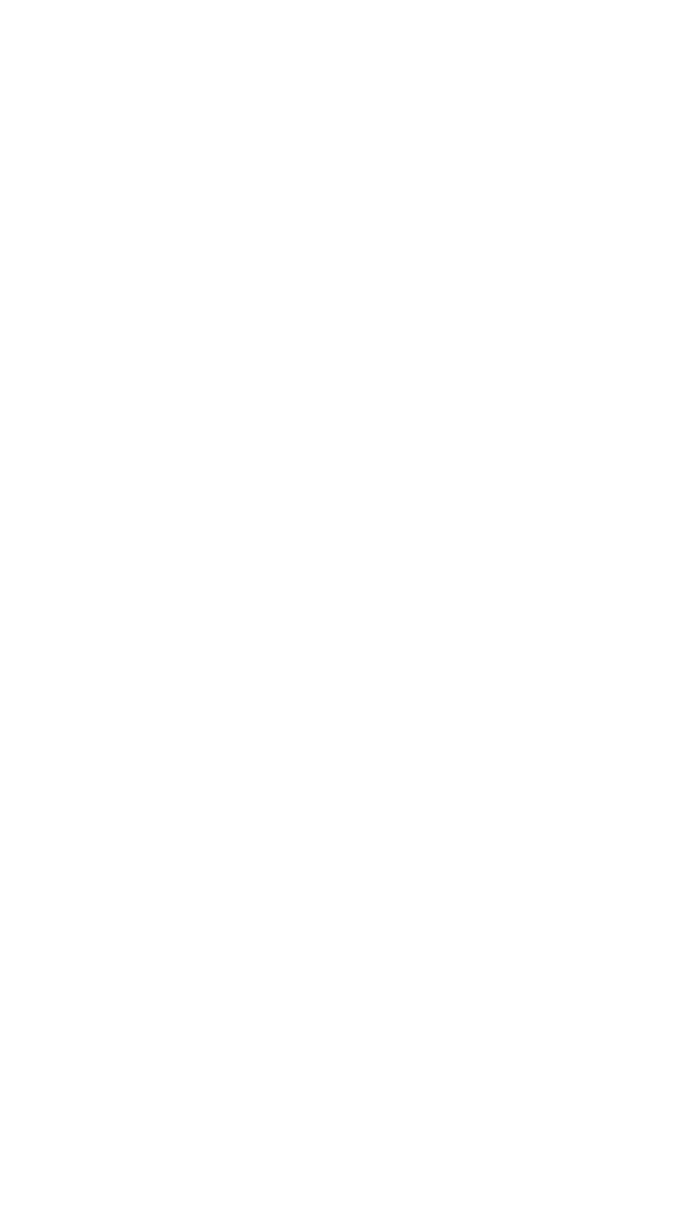
10 ENVIRONMENTAL CONCERNS 1367
This concept also applies to other industries. While evaluating the processing
of large fiberglass boat hulls, for example, I have observed mechanics making
repairs based on the engineering department’s sketches and instructions. Other
flaws were left as is.
In the case of press-molded parts, a visual examination of the part surface
and tap testing for porosity may be sufficient.
In summary, every product requires a quality control plan suited to the prod-
uct’s function and its value. As structural requirements and costs increase, the
engineering design effort must address defects. Parts with unacceptable discrep-
ancies or inadequate repairs must not be placed in service. Conversely, usable
parts should not be scrapped unnecessarily.
For lightly loaded consumer products, the engineering department can relax
as the manufacturing department struggles to always make the product look
pretty and keep defects within tolerable limits.
10 ENVIRONMENTAL CONCERNS
A composite manufacturing plant inherently has many environmental problems
simply due to the nature of the materials and processes used. Under prodding
by the Environmental Protection Agency (EPA), industrial hygiene has improved
significantly since the mid-1980s. Even so, profits from a well-conceived pro-
duction effort can be lost due to EPA penalties. So environmental concerns must
be a part of the materials selection and design effort, as well as a requirement
for manufacturing facilities. There are four problem areas: airborne vapors, skin
contact with allergens, dust, and disposal of waste.
Many resins contain ingredients with low boiling points. Polyester and vinyl
ester contain styrene whose odor permeates even well-ventilated facilities. Phe-
nolic resins have the sweet odor of unreacted phenol and give off formaldehyde.
A group of mechanics working on a highly classified project were awarded
compensation for medical problems because, reportedly, they were working in
an inadequately ventilated area and absorbed some chemicals.
An early curative for epoxy resin mixes prepared on the shop floor required
melting prior to use. Brown fumes were produced. I experienced them. They
stained our clothes (I was wearing ‘‘epoxy’’ workpants) and anything else
nearby. The first curative for polyurethane castings also required melting and
was a carcinogen. Both compounds where withdrawn after years of use.
Epoxy resins produce dermatitis once the body becomes sensitized. My best
technician did not develop a rash until 17 years of exposure, but I have seen
new employees develop rashes in several months. The only cure seems to be to
avoid contact with epoxy materials prior to cure and with dust from cured panels.
Material suppliers are required to provide materials safety data sheets listing the
ingredients in generic terms. These sheets should be carefully reviewed by the
safety team before new materials are introduced to production. In well-ventilated
areas, in my opinion, problems, except for dermatitis, are not significant as long
as normal precautions are taken. Food and drinks, for example, are no longer
allowed in lay-up areas.
Chips are produced when metals are drilled or cut. Composite machining, on
the other hand, produces dust. Recently, water jet cutting of composites, which
does not produce dust, has been introduced into production. Also, water-cooled
drills produce a gritty slurry instead of dust. Maximizing the use of water-cooled