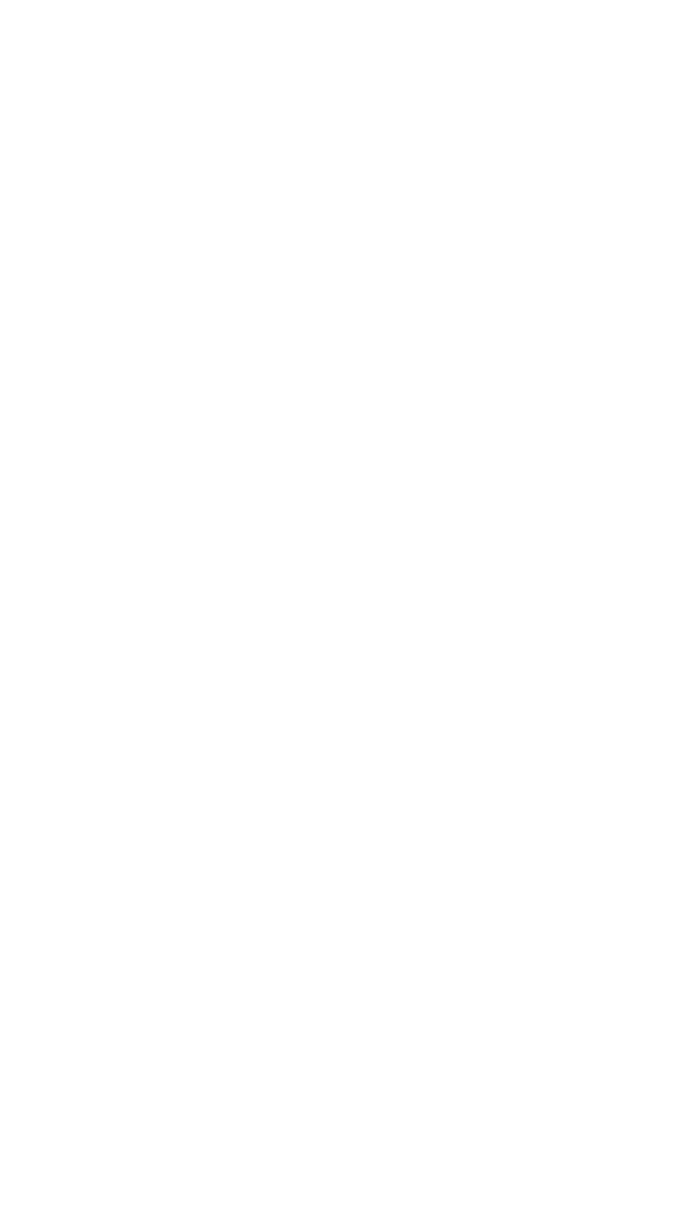
7 DETAIL DESIGN 1357
which require segmented tooling; (2) molded-in stiffness perpendicular to the
direction that a part is removed from a mold, except on the bottom of a box;
(3) lack of an adequate taper (draft); and (4) surface buildups, which tend to
‘‘hang up’’ on a mold during part removal.
These principles are illustrated by a press-molded junction box used with
buried telephone lines. Flanges to which the access door is attached project
beyond the box. The box is molded with the flanges up, so the stiffeners on the
opposite face are half-rounds. They are configured to be horizontal to provide
maximum support to the vertically positioned terminal strips inside the box. The
stiffeners on the remaining four faces of the box are blade configuration, tapering
in both width and height away from the flange. The design is tailored to simplify
removing the part from the tool. The part is molded in 2 min, then is popped
out of the tool quickly.
Five of the eight fabrication schemes involve lay-up of plies on mold, re-
gardless of how the part is cured. In many cases, this operation represents the
majority of labor costs. To become more efficient, both the number of plies and
the design of individual plies must be optimized. First, the number of plies must
be reduced, if possible, by using thicker materials, if they are available. A side
issue is weight penalty. In aircraft fiberglass parts, net sections are usually less
than 0.1 in. thick, and often are 0.05 inch thick, especially in sandwich construc-
tion. For these applications, the preferred dry glass fabric is style 181, which
weighs 8.9 oz per yd
2
and yields a composite thickness of 0.01 in. Boat hulls,
chemical storage tanks, and swimming pools require thicker laminates and are
less weight critical. So woven roving fabrics ranging up to 52 oz per yd
2
, with
a ply thickness of 0.05 in., are used for these applications. The weight of
chopped fiber mat varies from 0.75 to 3.0 oz per yd
2
. In addition to reduced
labor cost, thicker materials cost less per pound because throughput is increased
at the material supplier’s facility.
A second issue involves tailoring plies to simple shapes, which can be nested
in a cutting pattern, which reduces materials usage. Often, edge plies are used
at the edge of panels for bearing strength. They should be cut as strips. For
high-rate production, automated ply generation should be considered. Die cutting
is applicable for repetitive shapes. In plants producing large numbers of com-
posite parts repetitively, N/C cutting machines are used to cut and identify the
plies or ply segments. Then the plies are kitted and sent to the lay-up floor.
These N/C ply cutters come from the garment industry. A roll of material up
to 60
ⴖ wide is unrolled on a 20⬘ long table. A computer controlled cutter cuts
out individual plies of any shape. A second head uses ink to identify each piece.
The trick is to locate the pieces close together to avoid wasting material.
A good method to reduce the number of plies is to convert from a monolithic
panel to sandwich construction. Several low-cost methods are available.
Flat panels can be laid up and cured in a multicavity press. A widely used
system for movable interior partitions used fiberboard skins, paper honeycomb,
and film adhesive that cured rapidly. The boat building industry is licensing the
patented SCRIMP process developed by Seaman Composites. The process has
been used to make individual flat sandwich panels 18 ft
⫻ 40 ft, which are
sequentially co-cured into a multisided assembly. The skins are polyester-
impregnated rovings, and the core is foam slabs prespliced with room temper-
ature curing adhesive. The resin is injected into both skins while the assembly