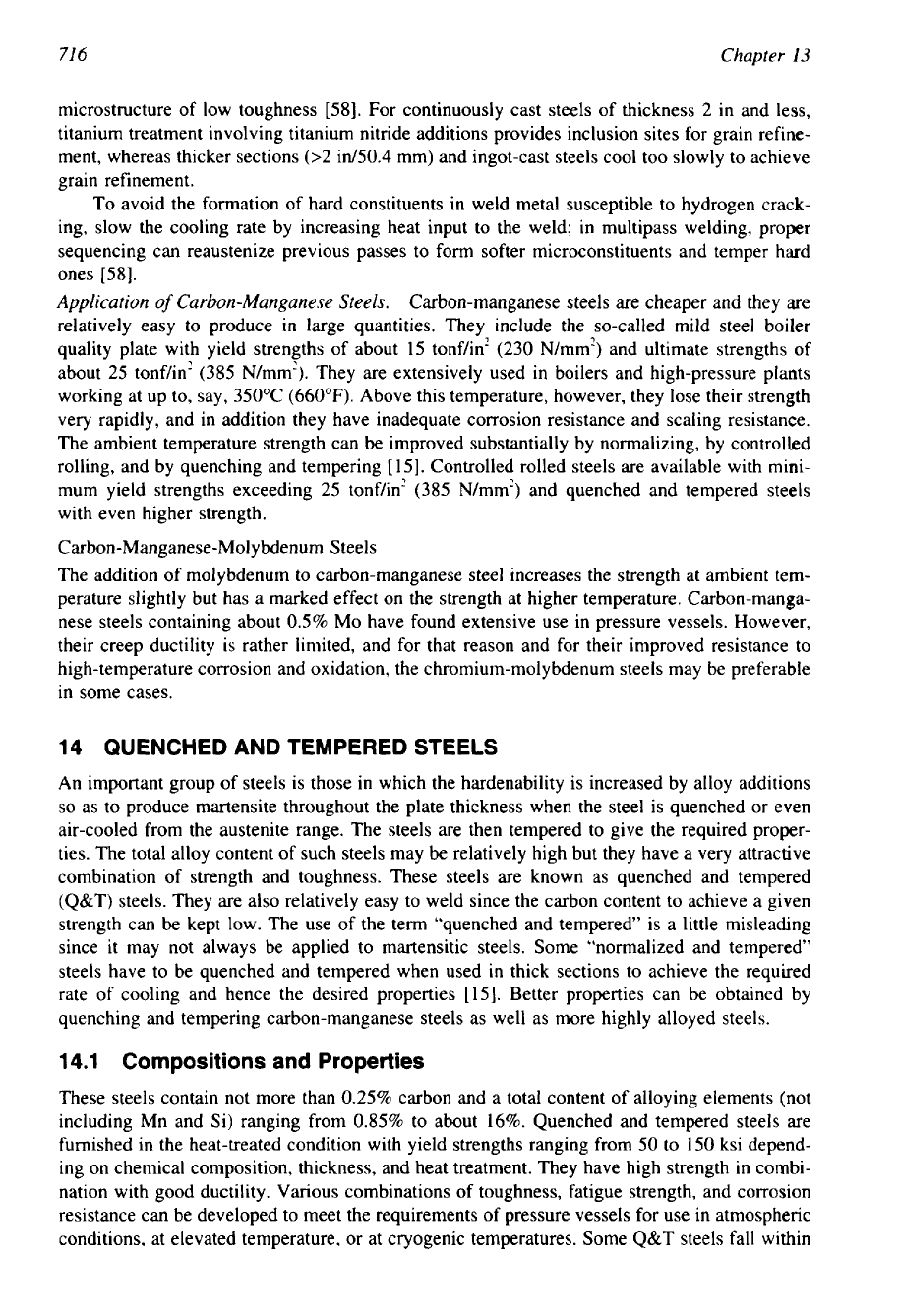
71
6
Chapter
13
microstructure of low toughness [58]. For continuously cast steels of thickness
2
in
and less,
titanium treatment involving titanium nitride additions provides inclusion sites for grain refine-
ment, whereas thicker sections
(>2
in/50.4 mm) and ingot-cast steels cool too slowly to achieve
grain refinement.
To avoid the formation of hard constituents in weld metal susceptible to hydrogen crack-
ing, slow the cooling rate by increasing heat input to the weld; in multipass welding, proper
sequencing can reaustenize previous passes to form softer microconstituents and temper hard
ones [58].
Application
of
Carbon-Manganese Steels.
Carbon-manganese steels are cheaper and they are
relatively easy to produce in large quantities. They include the so-called mild steel boiler
quality plate with yield strengths of about
15
tonf/in2
(230
N/mmz) and ultimate strengths of
about
25
tonf/in‘
(385
N/mm’). They are extensively used in boilers and high-pressure plants
working at up to, say, 350°C
(660°F).
Above this temperature, however, they lose their strength
very rapidly, and in addition they have inadequate corrosion resistance and scaling resistance.
The ambient temperature strength can be improved substantially by normalizing, by controlled
rolling, and by quenching and tempering
[15].
Controlled rolled steels are available with mini-
mum yield strengths exceeding
25
tonf/in‘ (385 N/mm‘) and quenched and tempered steels
with even higher strength.
Carbon-Manganese-Molybdenum Steels
The addition of molybdenum to carbon-manganese steel increases the strength at ambient tem-
perature slightly but has a marked effect on the strength at higher temperature. Carbon-manga-
nese steels containing about
0.5%
MO have found extensive use in pressure vessels. However,
their creep ductility is rather limited, and for that reason and for their improved resistance to
high-temperature corrosion and oxidation, the chromium-molybdenum steels may be preferable
in some cases.
14
QUENCHED AND TEMPERED STEELS
An important group of steels is those in which the hardenability is increased by alloy additions
so
as to produce martensite throughout the plate thickness when the steel is quenched or even
air-cooled from the austenite range. The steels are then tempered to give the required proper-
ties. The total alloy content of such steels may be relatively high but they have
a
very attractive
combination of strength and toughness. These steels are known as quenched and tempered
(Q&T) steels. They are also relatively easy to weld since the carbon content to achieve a given
strength can be kept low. The use of the term “quenched and tempered” is a little misleading
since it may not always be applied to martensitic steels. Some “normalized and tempered”
steels have to be quenched and tempered when used in thick sections to achieve the required
rate of cooling and hence the desired properties [15]. Better properties can be obtained by
quenching and tempering carbon-manganese steels as well as more highly alloyed steels.
14.1
Compositions and Properties
These steels contain not more than
0.25%
carbon and a total content of alloying elements (not
including Mn and Si) ranging from 0.85% to about
16%.
Quenched and tempered steels are
furnished in the heat-treated condition with yield strengths ranging from
50
to
150
ksi depend-
ing on chemical composition, thickness, and heat treatment. They have high strength in combi-
nation with good ductility. Various combinations of toughness, fatigue strength, and corrosion
resistance can be developed to meet the requirements of pressure vessels for use in atmospheric
conditions, at elevated temperature, or at cryogenic temperatures. Some
Q&T
steels fall within