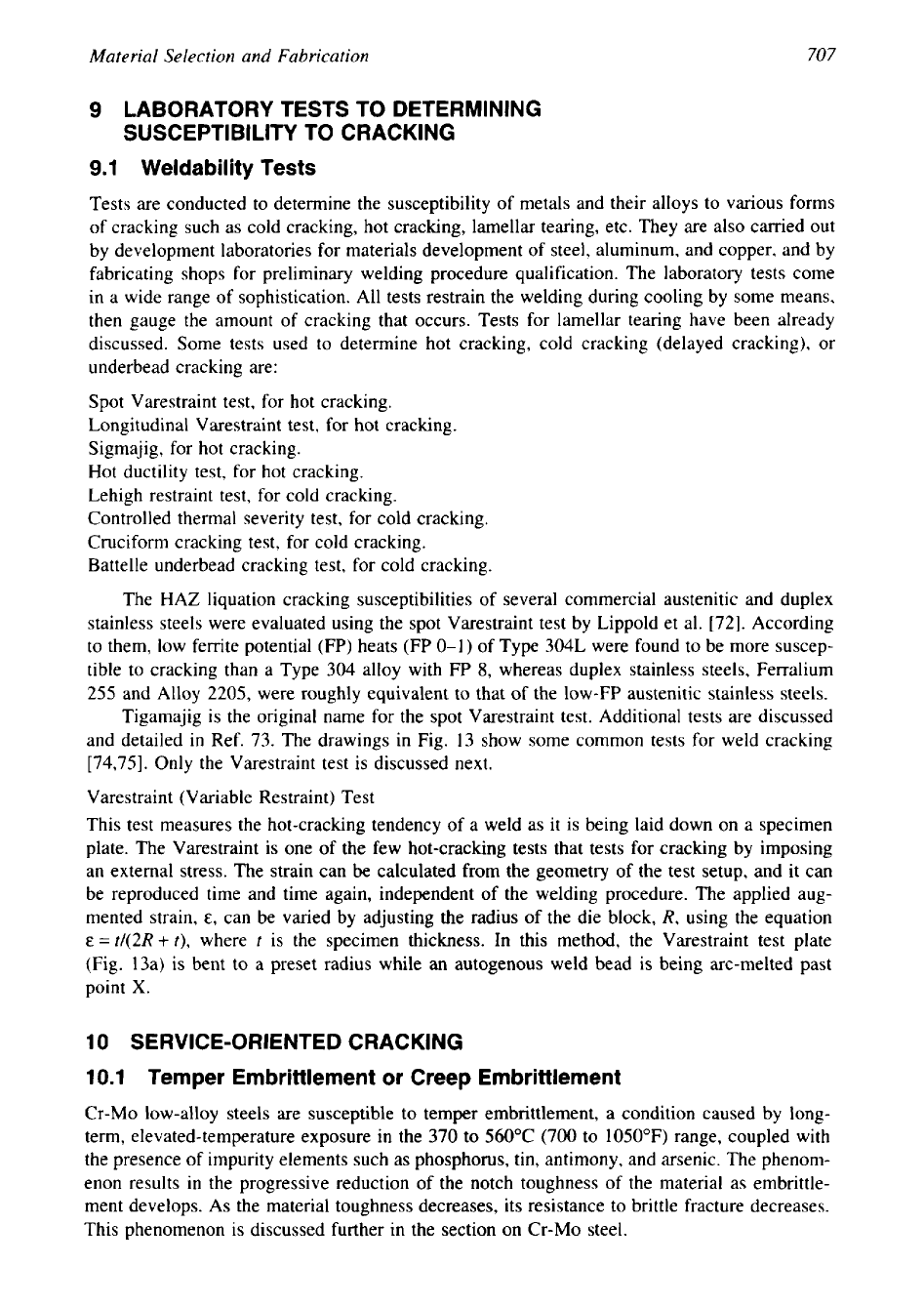
Material Selection and Fabrication
707
9
LABORATORY TESTS TO DETERMINING
SUSCEPTIBILITY TO CRACKING
9.1
Welda bility Tests
Tests are conducted to determine the susceptibility of metals and their alloys to various forms
of cracking such as cold cracking, hot cracking, lamellar tearing, etc. They are also carried out
by development laboratories for materials development of steel, aluminum, and copper, and by
fabricating shops for preliminary welding procedure qualification. The laboratory tests come
in a wide range
of
sophistication. All tests restrain the welding during cooling by some means,
then gauge the amount of cracking that occurs. Tests for lamellar tearing have been already
discussed. Some tests used to determine hot cracking, cold cracking (delayed cracking), or
underbead cracking are:
Spot Varestraint test, for hot cracking.
Longitudinal Varestraint test, for hot cracking.
Sigmajig, for hot cracking.
Hot ductility test, for hot cracking.
Lehigh restraint test, for cold cracking.
Controlled thermal severity test, for cold cracking.
Cruciform cracking test, for cold cracking.
Battelle underbead cracking test, for cold cracking.
The HAZ liquation cracking susceptibilities of several commercial austenitic and duplex
stainless steels were evaluated using the spot Varestraint test by Lippold et al. [72]. According
to them, low ferrite potential (FP) heats (FP 0-1) of Type 304L were found to be more suscep-
tible to cracking than a Type 304 alloy with FP
8,
whereas duplex stainless steels, Ferralium
255 and Alloy 2205, were roughly equivalent to that of the low-FP austenitic stainless steels.
Tigamajig is the original name for the spot Varestraint test. Additional tests are discussed
and detailed in Ref. 73. The drawings in Fig. 13 show some common tests for weld cracking
[74,75]. Only the Varestraint test is discussed next.
Varestraint (Variable Restraint) Test
This test measures the hot-cracking tendency of a weld as it is being laid down on a specimen
plate. The Varestraint is one of the few hot-cracking tests that tests for cracking by imposing
an external stress. The strain can be calculated
from
the geometry of the test setup, and it can
be reproduced time and time again, independent
of
the welding procedure. The applied aug-
mented strain,
E,
can be varied by adjusting the radius of the die block,
R,
using the equation
E
=
t/(2R+ t),
where
t
is the specimen thickness. In this method, the Varestraint test plate
(Fig. 13a) is bent to a preset radius while
an
autogenous weld bead is being arc-melted past
point
X.
10
SERVICE-ORIENTED CRACKING
10.1
Temper Embrittlement or Creep Embrittlement
Cr-Mo low-alloy steels are susceptible to temper embrittlement, a condition caused by long-
term, elevated-temperature exposure in the
370
to
560°C
(700 to 1050°F) range, coupled with
the presence
of
impurity elements such as phosphorus, tin, antimony, and arsenic. The phenom-
enon results in the progressive reduction of the notch toughness of the material as embrittle-
ment develops. As the material toughness decreases, its resistance to brittle fracture decreases.
This phenomenon is discussed further in the section on Cr-Mo steel.
Material Selection and Fabrication
707
9
LABORATORY TESTS TO DETERMINING
SUSCEPTIBILITY TO CRACKING
9.1
Welda bility Tests
Tests are conducted to determine the susceptibility of metals and their alloys to various forms
of cracking such as cold cracking, hot cracking, lamellar tearing, etc. They are also carried out
by development laboratories for materials development of steel, aluminum, and copper, and by
fabricating shops for preliminary welding procedure qualification. The laboratory tests come
in a wide range
of
sophistication. All tests restrain the welding during cooling by some means,
then gauge the amount of cracking that occurs. Tests for lamellar tearing have been already
discussed. Some tests used to determine hot cracking, cold cracking (delayed cracking), or
underbead cracking are:
Spot Varestraint test, for hot cracking.
Longitudinal Varestraint test, for hot cracking.
Sigmajig, for hot cracking.
Hot ductility test, for hot cracking.
Lehigh restraint test, for cold cracking.
Controlled thermal severity test, for cold cracking.
Cruciform cracking test, for cold cracking.
Battelle underbead cracking test, for cold cracking.
The HAZ liquation cracking susceptibilities of several commercial austenitic and duplex
stainless steels were evaluated using the spot Varestraint test by Lippold et al. [72]. According
to them, low ferrite potential (FP) heats (FP 0-1) of Type 304L were found to be more suscep-
tible to cracking than a Type 304 alloy with FP
8,
whereas duplex stainless steels, Ferralium
255 and Alloy 2205, were roughly equivalent to that of the low-FP austenitic stainless steels.
Tigamajig is the original name for the spot Varestraint test. Additional tests are discussed
and detailed in Ref. 73. The drawings in Fig. 13 show some common tests for weld cracking
[74,75]. Only the Varestraint test is discussed next.
Varestraint (Variable Restraint) Test
This test measures the hot-cracking tendency of a weld as it is being laid down on a specimen
plate. The Varestraint is one of the few hot-cracking tests that tests for cracking by imposing
an external stress. The strain can be calculated
from
the geometry of the test setup, and it can
be reproduced time and time again, independent
of
the welding procedure. The applied aug-
mented strain,
E,
can be varied by adjusting the radius of the die block,
R,
using the equation
E
=
t/(2R+ t),
where
t
is the specimen thickness. In this method, the Varestraint test plate
(Fig. 13a) is bent to a preset radius while
an
autogenous weld bead is being arc-melted past
point
X.
10
SERVICE-ORIENTED CRACKING
10.1
Temper Embrittlement or Creep Embrittlement
Cr-Mo low-alloy steels are susceptible to temper embrittlement, a condition caused by long-
term, elevated-temperature exposure in the
370
to
560°C
(700
to 1050°F) range, coupled with
the presence
of
impurity elements such as phosphorus, tin, antimony, and arsenic. The phenom-
enon results in the progressive reduction of the notch toughness of the material as embrittle-
ment develops. As the material toughness decreases, its resistance to brittle fracture decreases.
This phenomenon is discussed further in the section on Cr-Mo steel.