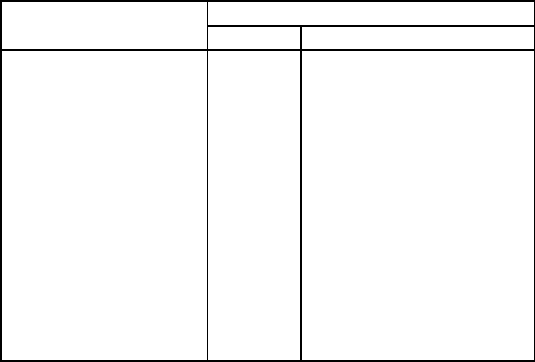
1.7. SOURCES OF MAGNETIC FIELD 65
Table 1.20: Typical values of the gradient of the magnetic field in magnetic
separators.
Separator Gradient of the magnetic field
T/m kG/cm
Suspended magnet 0.8 0.08
Nd magnetic roll 200 20
Nd drum separator 80 8
Davis tube 10 1
Frantz isodynamic 20 2
Belt separator 1-10 0.1 - 1
Steel wool (HGMS) 2.5×10
4
2.5×10
3
Steel balls (WHIMS) 1×10
3
100
Expanded metal 4×10
3
400
Grooved plates 2×10
3
200
Split pair OGMS 40 - 100 4-10
FHS 2 0.2
Magstream 30 3
In matrix (polygradient) magnetic separators, the gradient of the
magnetic field is generated by means of induced magnetic moment in the ferro-
magnetic bodies (called the matrix) and placed in the external magnetic field.
Strong magnetic field gradient is generated in the close vicinity of these bodies
and its magnitude depends on the size and the shape of the matrix elements.
Ferromagnetic bodies of various shapes have been used in high-intensity mag-
netic separators (such as balls, grooved plates, mesh, expanded metal, steel wool,
rods etc.) and a proper choice of the matrix is one of the crucial prerequisites
for successful separation.
Since the field gradient is inversely proportional to radius d of the matrix
element, i.e. uE M@d, the magnetic force acting on the magnetizable particles
is maximized by using as fine a matrix as possible. On the other hand, the
dimensions of the matrix elements must be selected taking into account particle
size of the material to avoid straining and to ensure the selectivity of separation.
At the same time, the dimensions of the matrix bodies must be chosen in such
a way that the magnetic force is su!ciently strong to recover the magnetic
fraction. On the other hand, the magnetic force must not be too strong to
cause the matrix blockage and retention of the ”non-magnetic” component.
In order to magnetize a fine matrix, su!ciently strong external magnetic
field is required. This is because the filling factor of the matrix is often low
and the matrix does not conduct magnetic flux very well. Typically, the filling
factor ranges from 0.04 (4%) for steel wool matrix to about 0.20 (20%) for
expanded metal. The exception is the ball matrix where the filling factor can
be as high 0.50, and grooved plates with the filling factor up to 0.80. Figure
1.49 illustrates that a background magnetic induction of at least 0.7 T is needed
to saturate the steel wool matrix, compared to about 0.2 T that is necessary to