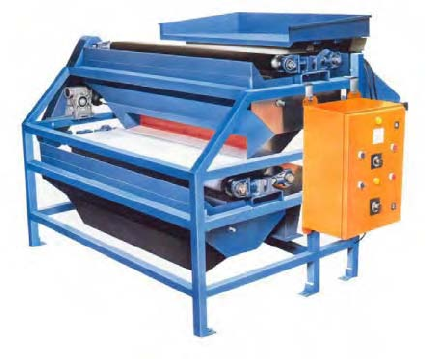
2.3. DRY HIGH-INTENSITY MAGNETIC SEPARATORS 93
Figure 2.31: Permanent magnetic roll separator Permroll
c
°
(courtesy of E.L.
Bateman Ltd.).
configuration is determined mainly by the magnetic properties and particle size
distribution of the material to be treated.
Operation of permanent magnetic roll separators is schematically shown in
Fig. 2.30. For easy removal of magnetic particles, the roll is covered by a belt,
which can be as thin as 0.12 mm, to allow the feed material to be as close to the
magnet as possible. The belt is supported by an idler roll. Below the conveyor
is a hopper which collects the discharging material, while adjustable splitters
divert the dierent fractions into collection bins placed beneath the hopper.
The most common diameter of the roll used to be 72 mm or 76 mm, while
rolls 100 mm and 300 mm in diameter have now become commonly available
from several manufacturers. The latter design is based on magnet segments
rather than rings. With increasing roll diameter, the residence time of particles
in the magnetic field, the field depth and the e!ciency of separation increase.
Alternatively, by increasing the speed of rotation, to maintain the same residence
time as with a smaller roll, a higher throughput could be achieved with the roll
of a larger diameter.
For production-scale applications, the width of the magnetic zone of the roll
is either 1000 mm or 1500 mm, although for smaller scale applications 250 mm
and 500 mm wide rolls are available. Throughput of roll separators is aected
by many factors, which include particle size, particle density, proportion of the
magnetic component in the feed and the desired quality of the final product.
As a guideline, a throughput of 2 to 6 t/h/m can be achieved with material
smaller than 2 mm, while larger material can be processed at a throughput up
to 15 t/h/m. A modular design enables a number of passes to be arranged into
a compact unit.