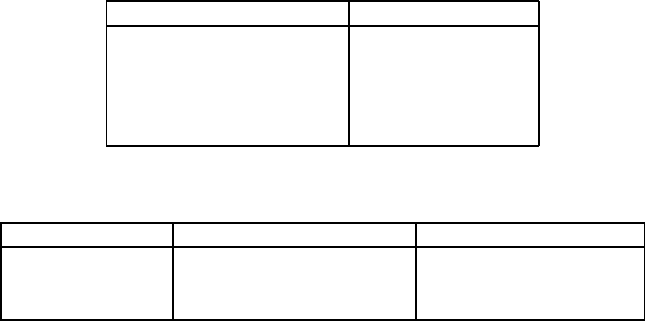
72 CHAPTER 2. REVIEW OF MAGNETIC SEPARATORS
Table 2.1: Standard belt speed for magnetic pulley operation.
Pulley diameter [mm] Belt speed [m/s]
500 1.1
630 1.45
800 1.7
1000 2.0
1250 2.2
Table 2.2: Recommended diameters of magnetic pulleys.
Feed size [mm] Pulley diameter [mm] Throughput [t/h/m]
50 - 100 750 - 900 250 - 400
25 - 50 450 - 600 165 - 250
6-25 300 - 450 75 -135
Magnetic pulleys of special design are used in the concentration of magnetite
and other ferromagnetic minerals. For the best results, the feed should be
screened into sized fractions and each fraction treated on a separate pulley.
Typical feed sizes would be - 100 mm + 50 mm, - 50 mm + 25 mm and -
25 mm + 6 mm. The magnetic pulley is not suited for the treatment of - 6
mm material. Pulley diameters recommended for various feed sizes are given in
Table 2.2 [M7].
2.1.2 Plate magnets
Where the amount of tramp iron contained in a product is reasonably small
and where automatic removal is not required, plate and grate magnets can be
incorporated in chutes and ducts to remove both tramp iron and iron of abrasion.
Such a plate magnet is shown in Fig. 2.5.
The plate consists of a series of alternating poles, uniform across the chute
width and alternating along the chute length. As the material passes over the
magnet face, tramp iron is trapped on the magnet face while the remaining non-
magnetic material proceeds down the chute. The plate magnets must be cleaned
and inspected daily since they are not eective if the accumulated tramp iron
is allowed to remain on the face.
The magnetized plates are usually of permanent magnet type, either ferrite
or rare earth. The eective depth of the magnetic field can be as high as 200 mm,
depending on the type of the magnetic material and on the shape of particles
to be removed. A chute angle not exceeding 45
0
is recommended [M7].
2.1.3 Grate magnets
The grate magnet shown in Figs. 2.6 and 2.7, consists of a series of magnetic
tubes, which have poles alternating between one another and along their length.