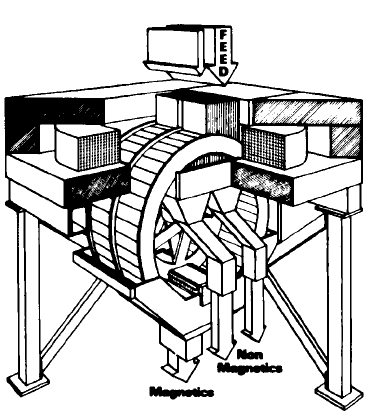
2.4. WET HIGH-INTENSITY MAGNETIC SEPARATORS 121
Figure 2.68: An isometric view of VMS.
a rotating drum, which carries separation chambers filled with matrix. The
non-magnetic and the middling fractions are collected in launders underneath
the magnet. Magnetizable particles are attracted to the matrix, placed in com-
partments along the periphery of the vertical wheel. When the matrix leaves
the region of the magnetic field during the rotation of the wheel, the captured
particles are flushed from the matrix. The magnetic product is thus washed o
from the matrix at the flush station in a direction opposite to that of the feed
and is collected in the trough at the bottom of the separator.
The maximum background magnetic induction generated by the magnet is
1.7 T, while stray magnetic induction outside the magnet is less than 5 mT.
Mild steel rods of 3 mm and 5 mm in diameter, with spacing of between 1.5
mm and 2.5 mm, are used as a matrix. Woven wire mesh has also been used in
some applications.
In order to increase the capacity of a magnetic separator, the width of the
working space must be increased. The VMS concept allows this very simply by
increasing the width of the wheel. Taking into account that the magnetic field in
the VMS separator is oriented vertically, perpendicularly to the increase of the
wheel width, the basic characteristics of the magnetic circuit remain unchanged,
i.e. the vertical length of the air gap, which determines the magnetomotive
force, or the number of ampere-turns needed to achieve the required magnetic
induction, is the same for any width of the wheel. Because of the increase in
the length of the conductor, energy consumption increases only linearly with
the wheel width. A throughput of up to 150 t/h was specified for the largest
separators VMS 100.