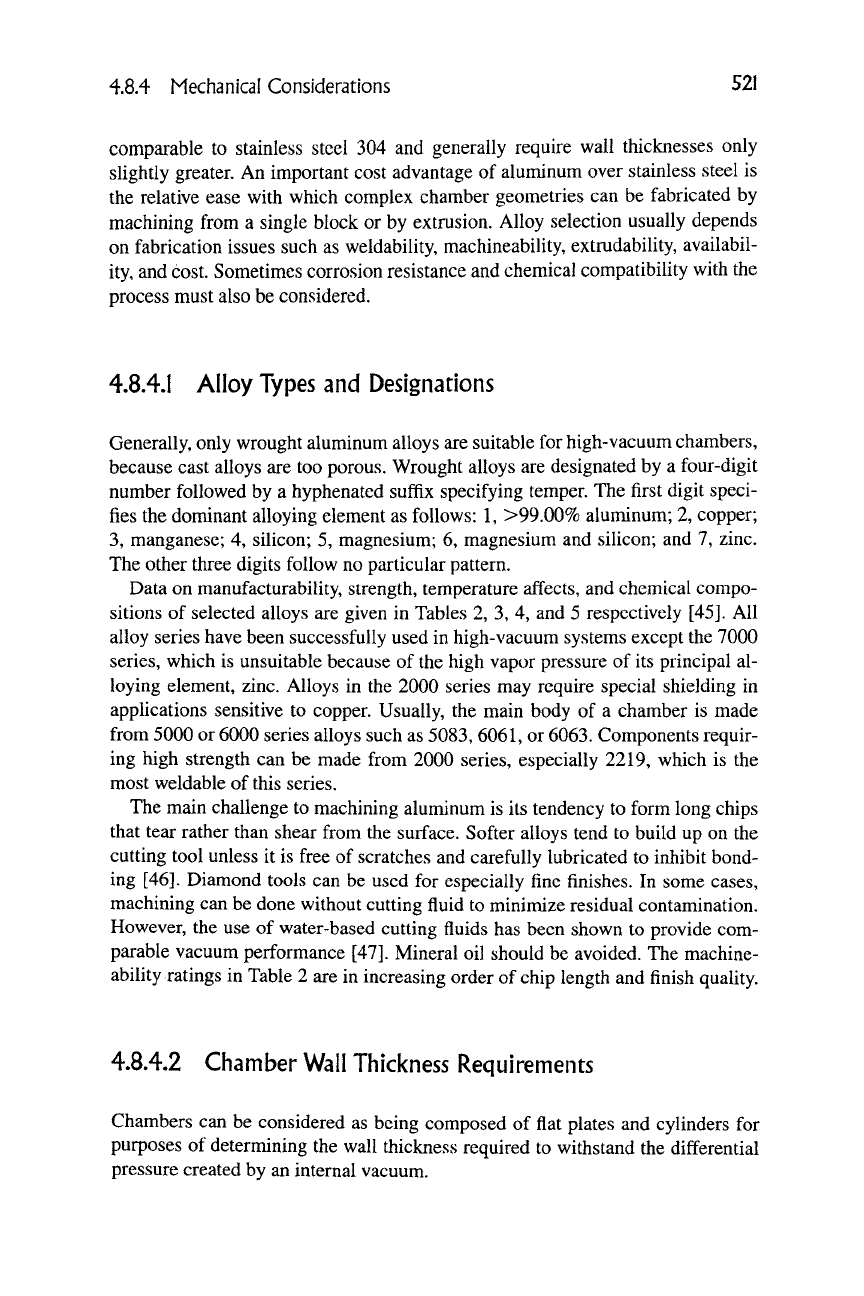
4.8.4 Mechanical Considerations 521
compai'able to stainless steel 304 and generally require wall thicknesses only
slightly greater. An important cost advantage of aluminum over stainless steel is
the relative ease with which complex chamber geometries can be fabricated by
machining from a single block or by extrusion. Alloy selection usually depends
on fabrication issues such as weldability, machineability, extrudability, availabil-
ity, and cost. Sometimes corrosion resistance and chemical compatibility with the
process must also be considered.
4.8.4.1 Alloy Types and Designations
Generally, only wrought aluminum alloys are suitable for high-vacuum chambers,
because cast alloys are too porous. Wrought alloys are designated by a four-digit
number followed by a hyphenated suffix specifying temper. The first digit speci-
fies the dominant alloying element as follows: 1, >99.00% aluminum; 2, copper;
3,
manganese; 4, silicon; 5, magnesium; 6, magnesium and silicon; and 7, zinc.
The other three digits follow no particular pattern.
Data on manufacturability, strength, temperature affects, and chemical compo-
sitions of selected alloys are given in Tables 2, 3, 4, and 5 respectively [45]. All
alloy series have been successfully used in high-vacuum systems except the 7000
series,
which is unsuitable because of the high vapor pressure of its principal al-
loying element, zinc. Alloys in the 2000 series may require special shielding in
applications sensitive to copper. Usually, the main body of a chamber is made
from 5000 or 6000 series alloys such as
5083,
6061, or
6063.
Components requir-
ing high strength can be made from 2000 series, especially 2219, which is the
most weldable of this series.
The main challenge to machining aluminum is its tendency to form long chips
that tear rather than shear from the surface. Softer alloys tend to build up on the
cutting tool unless it is free of scratches and carefully lubricated to inhibit bond-
ing [46]. Diamond tools can be used for especially fine finishes. In some cases,
machining can be done without cutting fluid to minimize residual contamination.
However, the use of water-based cutting fluids has been shown to provide com-
parable vacuum performance [47]. Mineral oil should be avoided. The machine-
ability ratings in Table 2 are in increasing order of chip length and finish quality.
4.8.4.2 Chamber Wall Thicicness Requirements
Chambers can be considered as being composed of flat plates and cylinders for
purposes of determining the wall thickness required to withstand the differential
pressure created by an internal vacuum.