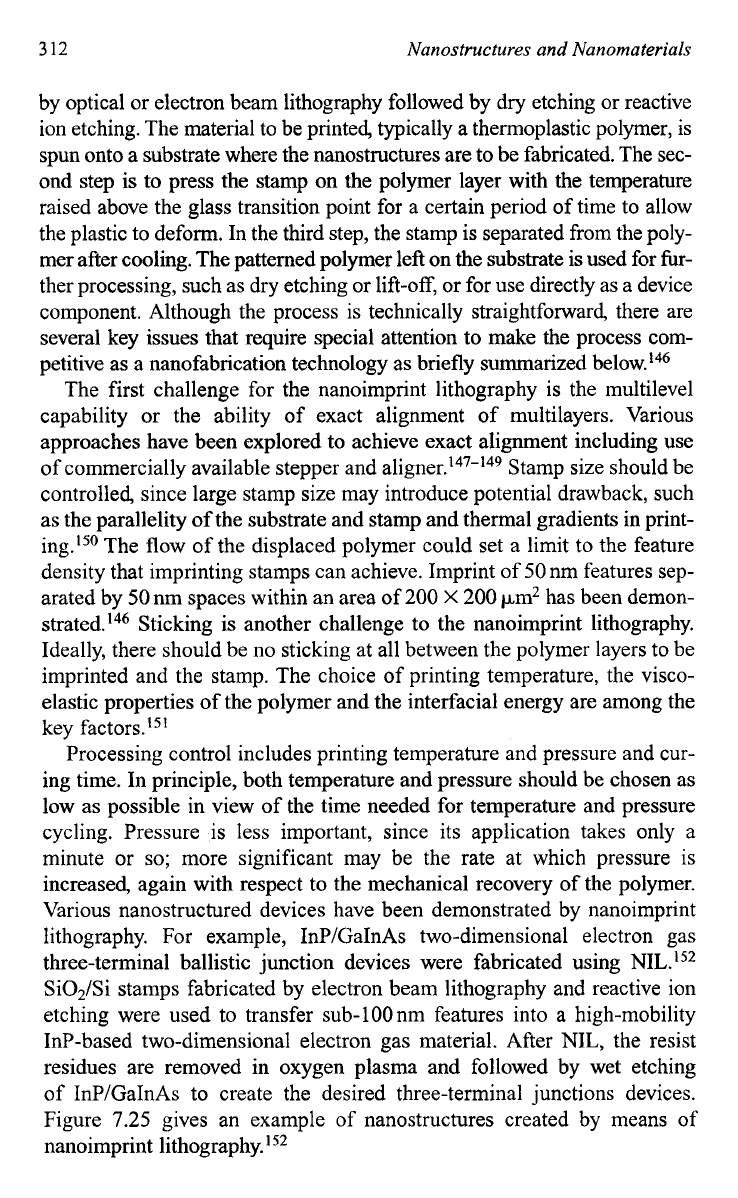
3
12 Nanostructures and Nanomaterials
by optical or electron beam lithography followed by
dry
etching or reactive
ion etching. The material to be printed, typically a thermoplastic polymer, is
spun onto a substrate where the nanostructures are to be fabricated, The sec-
ond step is to press the stamp on the polymer layer with the temperature
raised above the glass transition point for a certain period of time to allow
the plastic to deform. In the third step, the stamp is separated from the poly-
mer after cooling. The patterned polymer left on the substrate is used for
fur-
ther processing, such as dry etching or lift-off, or for use directly as a device
component. Although the process is technically straightforward, there are
several key issues that require special attention to make the process com-
petitive as a nanofabrication technology as briefly summarized below.
146
The first challenge for the nanoimprint lithography is the multilevel
capability or the ability of exact alignment of multilayers. Various
approaches have been explored to achieve exact alignment including use
of commercially available stepper and aligner.'47-149 Stamp size should be
controlled, since large stamp size may introduce potential drawback, such
as the parallelity of the substrate and stamp and thermal gradients in print-
ing.I5O The
flow
of the displaced polymer could set a limit to the feature
density that imprinting stamps can achieve. Imprint of
50
nm features sep-
arated by
50
nm spaces within an area
of
200
X
200
Fm2 has been demon-
~trated.'~~ Sticking is another challenge to the nanoimprint lithography.
Ideally, there should be no sticking at all between the polymer layers to be
imprinted and the stamp. The choice of printing temperature, the visco-
elastic properties of the polymer and the interfacial energy are among the
key fa~t0rs.I~~
Processing control includes printing temperature and pressure and cur-
ing time. In principle, both temperature and pressure should be chosen as
low as possible in view of the time needed for temperature and pressure
cycling. Pressure is less important, since its application takes only a
minute or
so;
more significant may be the rate at which pressure is
increased, again with respect to the mechanical recovery of the polymer.
Various nanostructured devices have been demonstrated by nanoimprint
lithography. For example, InP/GaInAs two-dimensional electron gas
three-terminal ballistic junction devices were fabricated using NIL.
152
Si02/Si stamps fabricated by electron beam lithography and reactive ion
etching were used to transfer sub-
100
nm features into a high-mobility
InP-based two-dimensional electron gas material. After NIL, the resist
residues are removed in oxygen plasma and followed by wet etching
of InP/GaInAs to create the desired three-terminal junctions devices.
Figure
7.25
gives an example of nanostructures created by means of
nanoimprint lithography.
152