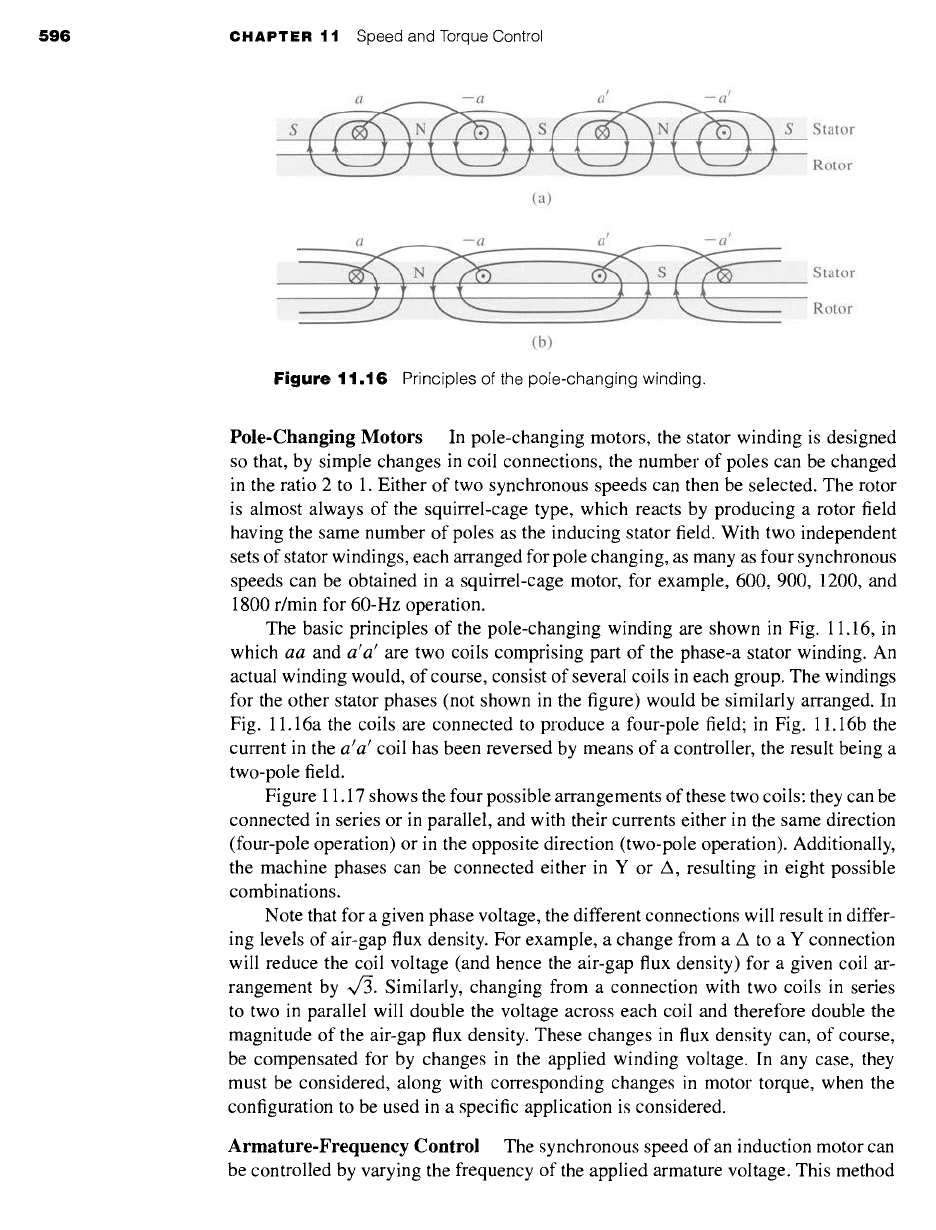
596 CHAPTER 11 Speed and Torque Control
Stator
Rotor
(a)
(b)
Figure
11.16 Principles of the pole-changing winding.
Stator
Rotor
Pole-Changing Motors
In pole-changing motors, the stator winding is designed
so that, by simple changes in coil connections, the number of poles can be changed
in the ratio 2 to 1. Either of two synchronous speeds can then be selected. The rotor
is almost always of the squirrel-cage type, which reacts by producing a rotor field
having the same number of poles as the inducing stator field. With two independent
sets of stator windings, each arranged for pole changing, as many as four synchronous
speeds can be obtained in a squirrel-cage motor, for example, 600, 900, 1200, and
1800 r/min for 60-Hz operation.
The basic principles of the pole-changing winding are shown in Fig. 11.16, in
which
aa
and
a'a'
are two coils comprising part of the phase-a stator winding. An
actual winding would, of course, consist of several coils in each group. The windings
for the other stator phases (not shown in the figure) would be similarly arranged. In
Fig. 11.16a the coils are connected to produce a four-pole field; in Fig. 11.16b the
current in the a'a' coil has been reversed by means of a controller, the result being a
two-pole field.
Figure 11.17 shows the four possible arrangements of these two coils: they can be
connected in series or in parallel, and with their currents either in the same direction
(four-pole operation) or in the opposite direction (two-pole operation). Additionally,
the machine phases can be connected either in Y or A, resulting in eight possible
combinations.
Note that for a given phase voltage, the different connections will result in differ-
ing levels of air-gap flux density. For example, a change from a A to a Y connection
will reduce the coil voltage (and hence the air-gap flux density) for a given coil ar-
rangement by ~. Similarly, changing from a connection with two coils in series
to two in parallel will double the voltage across each coil and therefore double the
magnitude of the air-gap flux density. These changes in flux density can, of course,
be compensated for by changes in the applied winding voltage. In any case, they
must be considered, along with corresponding changes in motor torque, when the
configuration to be used in a specific application is considered.
Armature-Frequency Control The synchronous speed of an induction motor can
be controlled by varying the frequency of the applied armature voltage. This method