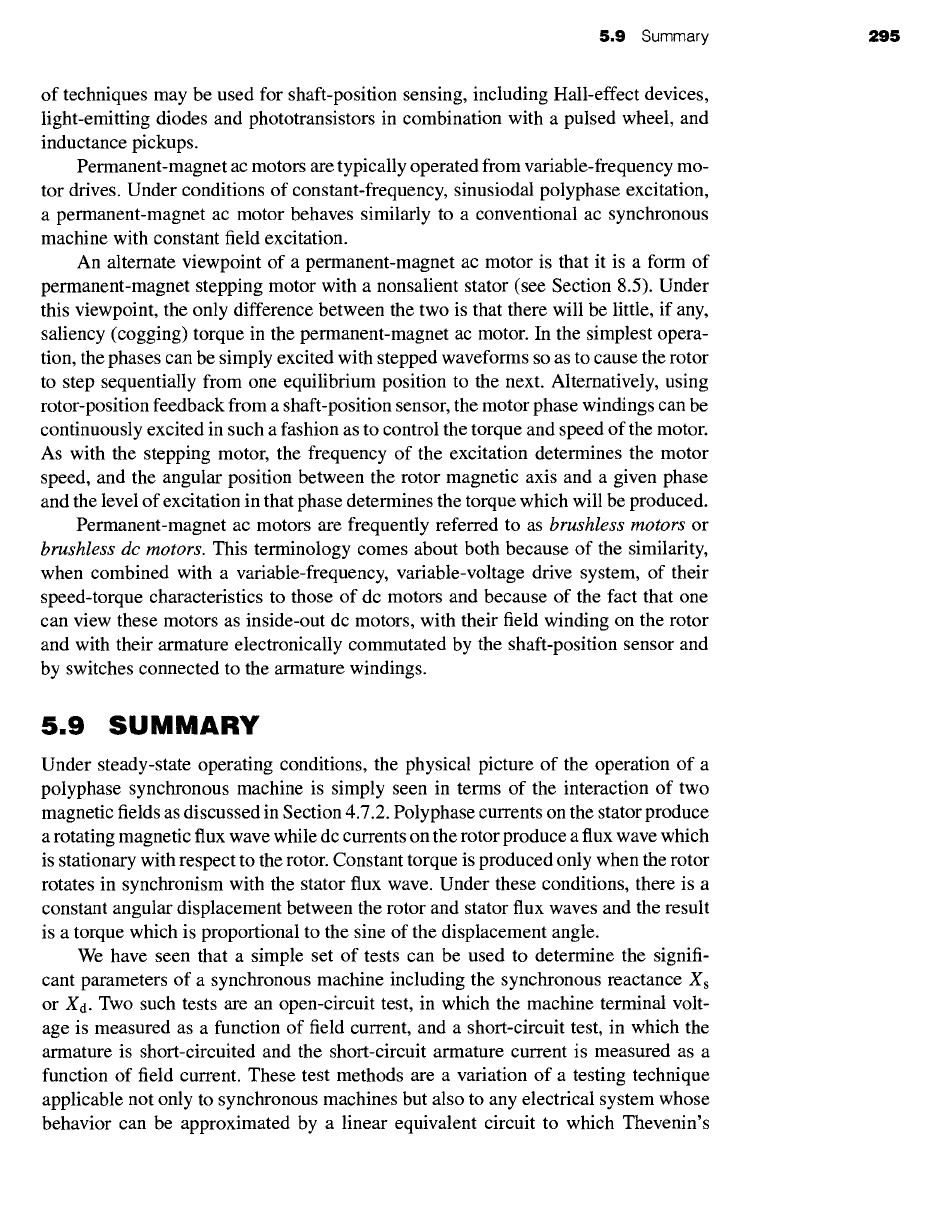
5.9 Summary 295
of techniques may be used for shaft-position sensing, including Hall-effect devices,
light-emitting diodes and phototransistors in combination with a pulsed wheel, and
inductance pickups.
Permanent-magnet ac motors are typically operated from variable-frequency mo-
tor drives. Under conditions of constant-frequency, sinusiodal polyphase excitation,
a permanent-magnet ac motor behaves similarly to a conventional ac synchronous
machine with constant field excitation.
An alternate viewpoint of a permanent-magnet ac motor is that it is a form of
permanent-magnet stepping motor with a nonsalient stator (see Section 8.5). Under
this viewpoint, the only difference between the two is that there will be little, if any,
saliency (cogging) torque in the permanent-magnet ac motor. In the simplest opera-
tion, the phases can be simply excited with stepped waveforms so as to cause the rotor
to step sequentially from one equilibrium position to the next. Alternatively, using
rotor-position feedback from a shaft-position sensor, the motor phase windings can be
continuously excited in such a fashion as to control the torque and speed of the motor.
As with the stepping motor, the frequency of the excitation determines the motor
speed, and the angular position between the rotor magnetic axis and a given phase
and the level of excitation in that phase determines the torque which will be produced.
Permanent-magnet ac motors are frequently referred to as
brushless motors
or
brushless dc motors.
This terminology comes about both because of the similarity,
when combined with a variable-frequency, variable-voltage drive system, of their
speed-torque characteristics to those of dc motors and because of the fact that one
can view these motors as inside-out dc motors, with their field winding on the rotor
and with their armature electronically commutated by the shaft-position sensor and
by switches connected to the armature windings.
5.9 SUMMARY
Under steady-state operating conditions, the physical picture of the operation of a
polyphase synchronous machine is simply seen in terms of the interaction of two
magnetic fields as discussed in Section 4.7.2. Polyphase currents on the stator produce
a rotating magnetic flux wave while dc currents on the rotor produce a flux wave which
is stationary with respect to the rotor. Constant torque is produced only when the rotor
rotates in synchronism with the stator flux wave. Under these conditions, there is a
constant angular displacement between the rotor and stator flux waves and the result
is a torque which is proportional to the sine of the displacement angle.
We have seen that a simple set of tests can be used to determine the signifi-
cant parameters of a synchronous machine including the synchronous reactance Xs
or Xd. Two such tests are an open-circuit test, in which the machine terminal volt-
age is measured as a function of field current, and a short-circuit test, in which the
armature is short-circuited and the short-circuit armature current is measured as a
function of field current. These test methods are a variation of a testing technique
applicable not only to synchronous machines but also to any electrical system whose
behavior can be approximated by a linear equivalent circuit to which Thevenin's