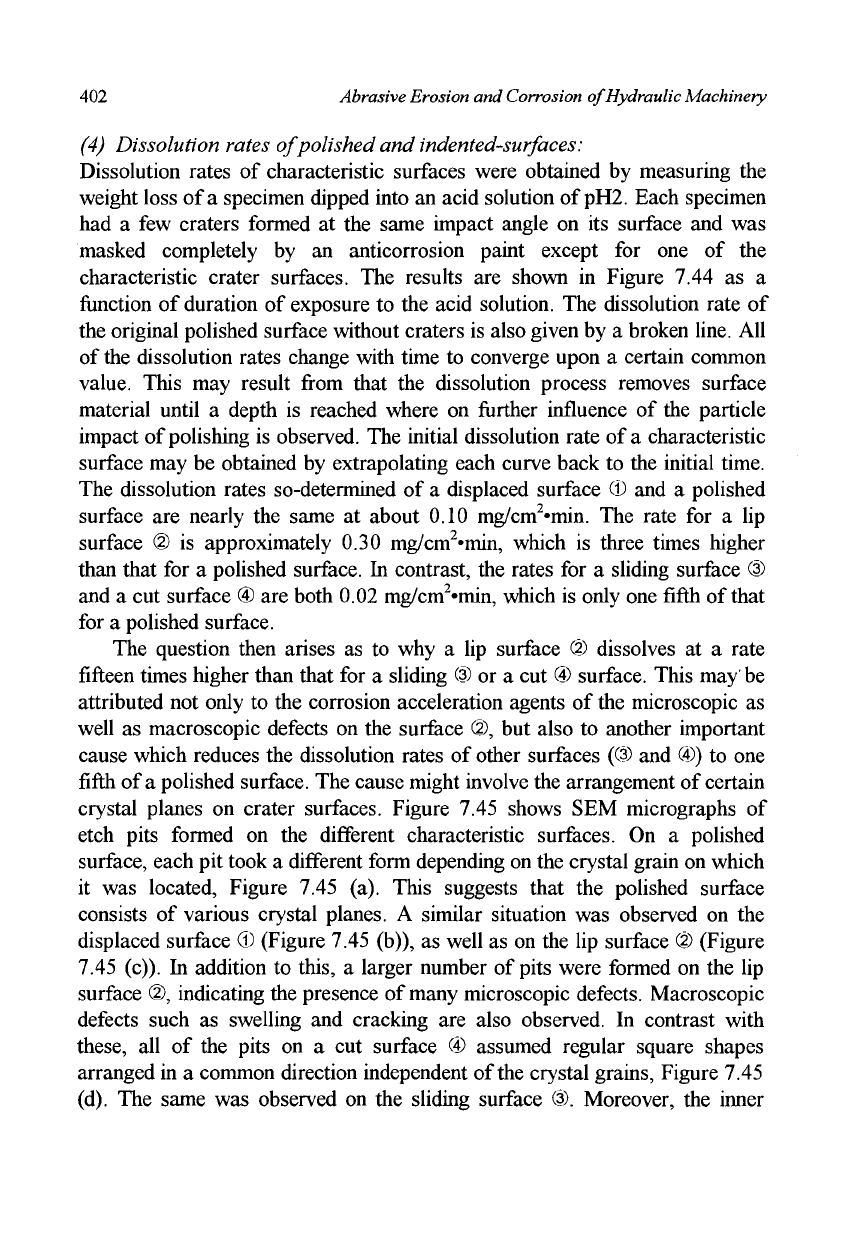
402
Abrasive Erosion and Corrosion of Hydraulic Machinery
(4) Dissolution rates of polished and indented-surfaces:
Dissolution rates of characteristic surfaces were obtained by measuring the
weight loss of a specimen dipped into an acid solution of
pH2.
Each specimen
had a few craters formed at the same impact angle on its surface and was
masked completely by an anticorrosion paint except for one of the
characteristic crater surfaces. The results are shown in Figure 7.44 as a
function of duration of exposure to the acid solution. The dissolution rate of
the original polished surface without craters is also given by a broken line. All
of the dissolution rates change with time to converge upon a certain common
value. This may result from that the dissolution process removes surface
material until a depth is reached where on further influence of the particle
impact of polishing is observed. The initial dissolution rate of a characteristic
surface may be obtained by extrapolating each curve back to the initial time.
The dissolution rates so-determined of a displaced surface
CD
and a polished
surface are nearly the same at about 0.10 mg/cm
2
*min. The rate for a lip
surface @ is approximately 0.30 mg/cm
2
«min, which is three times higher
than that for a polished surface. In contrast, the rates for a sliding surface ®
and a cut surface © are both 0.02 mg/cm
2,
min, which is only one fifth of that
for a polished surface.
The question then arises as to why a lip surface (?) dissolves at a rate
fifteen times higher than that for a sliding ® or a cut © surface. This may be
attributed not only to the corrosion acceleration agents of the microscopic as
well as macroscopic defects on the surface <S), but also to another important
cause which reduces the dissolution rates of other surfaces (® and ©) to one
fifth of a polished surface. The cause might involve the arrangement of certain
crystal planes on crater surfaces. Figure 7.45 shows SEM micrographs of
etch pits formed on the different characteristic surfaces. On a polished
surface, each pit took a different form depending on the crystal grain on which
it was located, Figure 7.45 (a). This suggests that the polished surface
consists of various crystal planes. A similar situation was observed on the
displaced surface © (Figure 7.45 (b)), as well as on the lip surface ® (Figure
7.45 (c)). In addition to this, a larger number of pits were formed on the lip
surface @, indicating the presence of many microscopic defects. Macroscopic
defects such as swelling and cracking are also observed. In contrast with
these, all of the pits on a cut surface © assumed regular square shapes
arranged in a common direction independent of the crystal grains, Figure 7.45
(d).
The same was observed on the sliding surface ®. Moreover, the inner