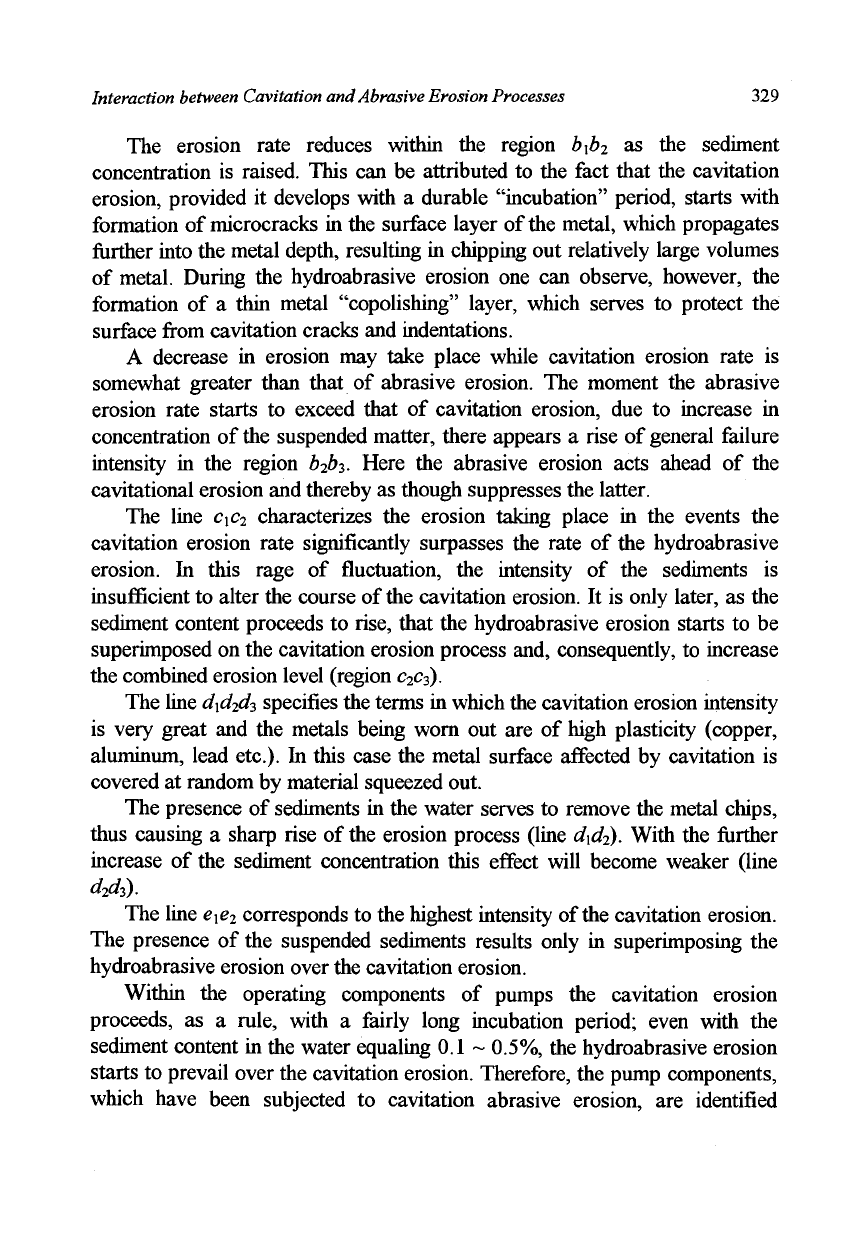
Interaction between Cavitation and Abrasive Erosion Processes
329
The erosion rate reduces within the region b\b
2
as the sediment
concentration is raised. This can be attributed to the fact that the cavitation
erosion, provided it develops with a durable "incubation" period, starts with
formation of microcracks in the surface layer of
the
metal, which propagates
further into the metal depth, resulting in chipping out relatively large volumes
of metal. During the hydroabrasive erosion one can observe, however, the
formation of a thin metal "copolishing" layer, which serves to protect the
surface from cavitation cracks and indentations.
A decrease in erosion may take place while cavitation erosion rate is
somewhat greater than that of abrasive erosion. The moment the abrasive
erosion rate starts to exceed that of cavitation erosion, due to increase in
concentration of the suspended matter, there appears a rise of general failure
intensity in the region
b
2
b-$.
Here the abrasive erosion acts ahead of the
cavitational erosion and thereby as though suppresses the latter.
The line c\c
2
characterizes the erosion taking place in the events the
cavitation erosion rate significantly surpasses the rate of the hydroabrasive
erosion. In this rage of fluctuation, the intensity of the sediments is
insufficient to alter the course of the cavitation erosion. It is only later, as the
sediment content proceeds to rise, that the hydroabrasive erosion starts to be
superimposed on the cavitation erosion process and, consequently, to increase
the combined erosion level (region c
2
c
3
).
The line
d
{
d
2
d3
specifies the terms in which the cavitation erosion intensity
is very great and the metals being worn out are of high plasticity (copper,
aluminum, lead etc.). In this case the metal surface affected by cavitation is
covered at random by material squeezed out.
The presence of sediments in the water serves to remove the metal chips,
thus causing a sharp rise of the erosion process (line
d\d
2
).
With the further
increase of the sediment concentration this effect will become weaker (line
d
2
d
i
).
The line e\e
2
corresponds to the highest intensity of the cavitation erosion.
The presence of the suspended sediments results only in superimposing the
hydroabrasive erosion over the cavitation erosion.
Within the operating components of pumps the cavitation erosion
proceeds, as a rule, with a fairly long incubation period; even with the
sediment content in the water equaling 0.1 ~ 0.5%, the hydroabrasive erosion
starts to prevail over the cavitation erosion. Therefore, the pump components,
which have been subjected to cavitation abrasive erosion, are identified