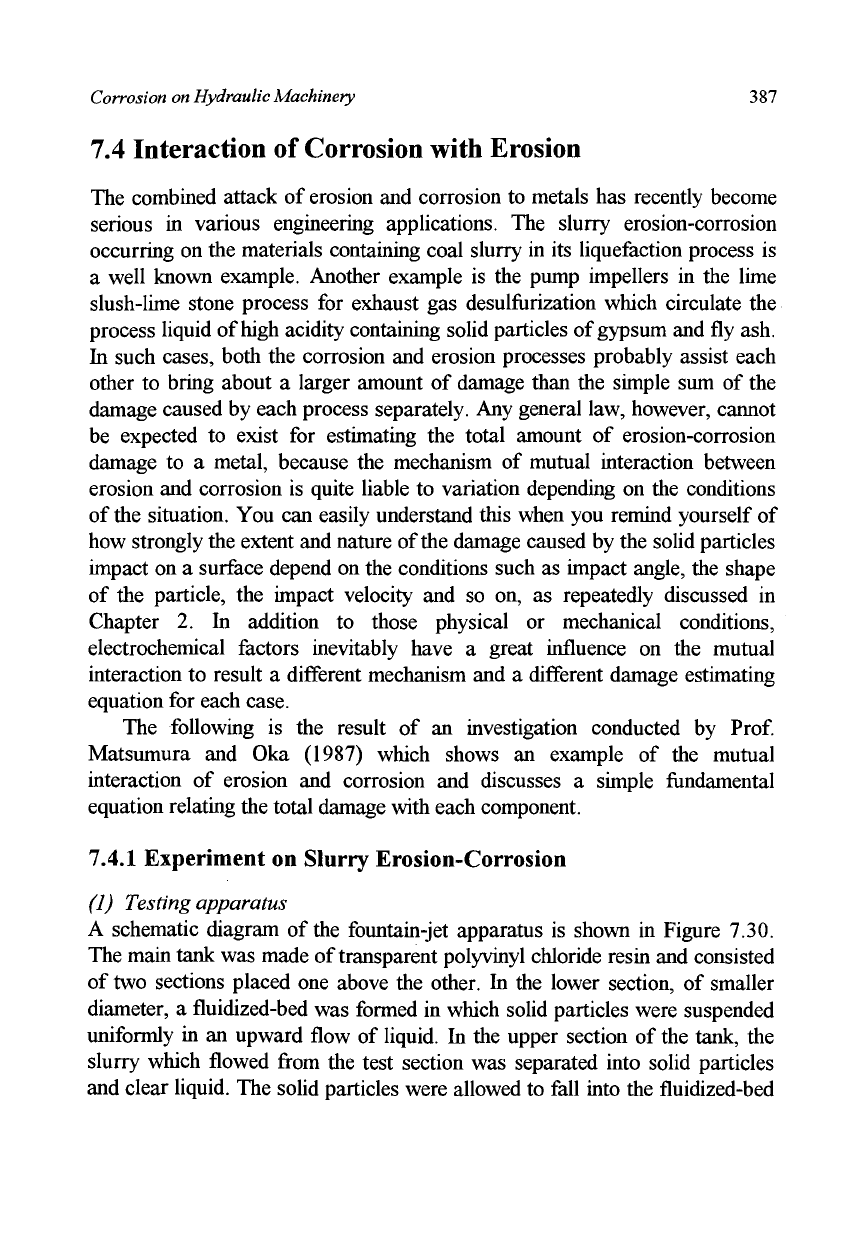
Corrosion on Hydraulic Machinery
387
7.4 Interaction of Corrosion with Erosion
The combined attack of erosion and corrosion to metals has recently become
serious in various engineering applications. The slurry erosion-corrosion
occurring on the materials containing coal slurry in its liquefaction process is
a well known example. Another example is the pump impellers in the lime
slush-lime stone process for exhaust gas desulfurization which circulate the
process liquid of high acidity containing solid particles of gypsum and fly ash.
In such cases, both the corrosion and erosion processes probably assist each
other to bring about a larger amount of damage than the simple sum of the
damage caused by each process separately. Any general law, however, cannot
be expected to exist for estimating the total amount of erosion-corrosion
damage to a metal, because the mechanism of mutual interaction between
erosion and corrosion is quite liable to variation depending on the conditions
of the situation. You can easily understand this when you remind yourself of
how strongly the extent and nature of the damage caused by the solid particles
impact on a surface depend on the conditions such as impact angle, the shape
of the particle, the impact velocity and so on, as repeatedly discussed in
Chapter 2. In addition to those physical or mechanical conditions,
electrochemical factors inevitably have a great influence on the mutual
interaction to result a different mechanism and a different damage estimating
equation for each case.
The following is the result of an investigation conducted by
Prof.
Matsumura and Oka (1987) which shows an example of the mutual
interaction of erosion and corrosion and discusses a simple fundamental
equation relating the total damage with each component.
7.4.1 Experiment on Slurry Erosion-Corrosion
(1) Testing apparatus
A schematic diagram of the fountain-jet apparatus is shown in Figure 7.30.
The main tank was made of transparent polyvinyl chloride resin and consisted
of two sections placed one above the other. In the lower section, of smaller
diameter, a fluidized-bed was formed in which solid particles were suspended
uniformly in an upward flow of liquid. In the upper section of the tank, the
slurry which flowed from the test section was separated into solid particles
and clear liquid. The solid particles were allowed to fall into the fluidized-bed