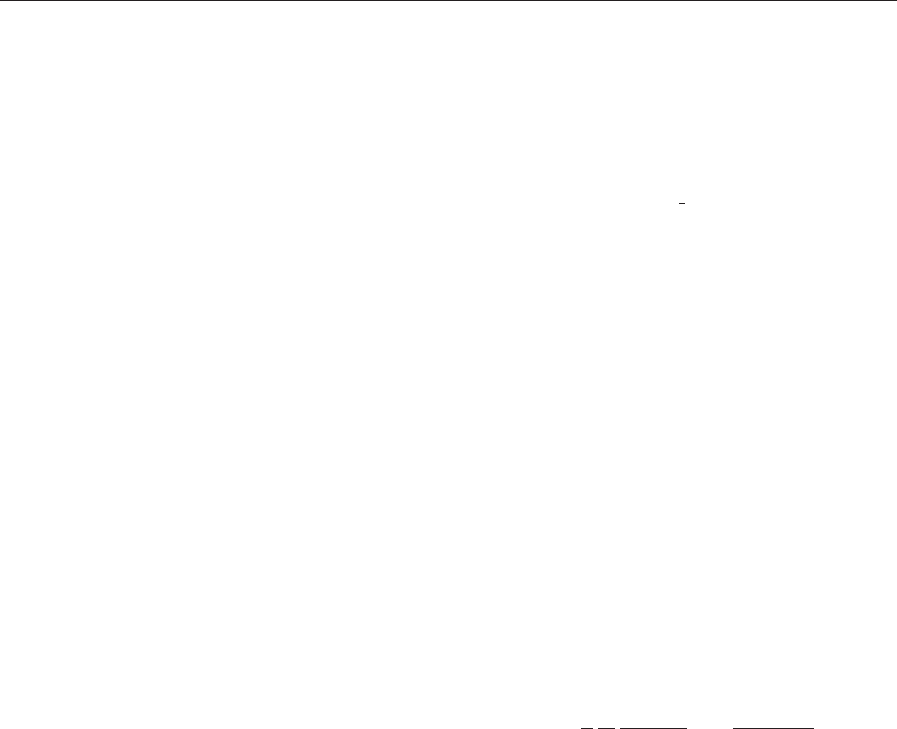
micropumps, and ultrasonic motors (Quandt 2000).
The development of the corresponding room temper-
ature giant magnetostrictive thin film materials is
based on rare earth–transition metal alloys. In gener-
al, the rare earth iron-based alloys offer the best
chance of developing giant magnetostriction at room
temperature or above, since the highly aspherical 4f
orbitals of the rare earths remain in an oriented state,
owing to the strong coupling between the rare earth
and the iron moments, resulting in this large room-
temperature magnetostriction.
An important task in developing giant magnetos-
trictive materials has been optimization of magneto-
striction to magnetic anisotropy ratio, in order to
attain large strains at moderate magnetic fields. In
bulk materials it was achieved by using cubic com-
pounds—the rare earth–Fe
2
Laves phases—in which
the second order anisotropy constant vanishes, also
by Tb–Dy alloying in order to compensate the fourth
order anisotropy constant (Clark 1980). In the case of
thin films, amorphous (Tb,Dy)
x
(Fe,Co)
1x
films
(Duc et al. 1996) or especially novel TbFe/FeCo
multilayers (Quandt and Ludwig 1999) represent the
most promising approaches to combine soft magnetic
and giant magnetostrictive properties.
Special attention has to be paid to the sign of the
magnetostriction. While terbium-based materials ex-
hibit positive magnetostriction, which means that this
material expands in the direction of the external field,
samarium-based materials behave in the opposite
way, thus allowing an easy design of magnetostrictive
bimorphs, which enables the realization of stress- or
temperature-compensated bending actuators while
further enhancing the overall effect.
The fabrication of giant magnetostrictive thin films
was originally realized only by PVD techniques, the
most prominently used being magnetron sputtering
(Quandt 2000) with either mosaic-type or composite
targets as well as multitarget arrangements. Other
PVD techniques include electron beam evaporation,
laser ablation and ion beam sputtering. The amor-
phous films are generally deposited onto unheated or
cooled substrates, while for crystalline films heated
substrates for a single-step process are used as an al-
ternative to a post-deposition crystallization treatment.
For applications, the orientation of the magnetic
easy axis and of the domains in the demagnetized
state is of special importance, because maximum
magnetostriction is only obtained by 90 1 rotations of
the magnetic domains while 180 1 rotations do not
result in any magnetostrictive strain. Considering
that magnetostrictive thin film actuators are in gen-
eral driven by a single magnetic field, the direction of
which is fixed in relation to the actuator and in-plane
in order to avoid large demagnetization losses, the
optimized demagnetized state should consist of do-
mains with an in-plane easy axis being oriented per-
pendicular to the driving field direction. This initial
state can be obtained by a post-deposition annealing
process under an in-plane magnetic field which is
oriented under 90 1 towards the driving field direction
(Ludwig and Quandt 2000).
Another possibility to influence the direction of the
magnetic easy axis of a magnetostrictive film is di-
rectly related to the film’s stress. Considering the
minimum of the magnetoelastic energy for an iso-
tropic ferromagnet
E
me
¼
3
2
sl
s
cos
2
a
the orientation of the magnetic easy axis (a: angle
between the directions of the magnetization and of
the application of the stress) depends on the sign of
the film stress s for a material with a given saturation
magnetostriction l
s
. This equation implies an in-
plane magnetic easy axis for a positive product sl
s
,
while a negative product results in a perpendicular
anisotropy. Therefore, in the case of positive magne-
tostrictive-like terbium-based or FeCo films, tensile
stress is required for in-plane anisotropy, whereas
negative magnetostrictive samarium-based films
should be deposited with compressive stress to result
in the same anisotropy. As the sign and the magni-
tude of the film’s stress can be controlled by the fab-
rication conditions, the thermal expansion coefficient
of the substrate, or by stress annealing, an in-plane
magnetic easy axis can be adjusted, in general, for all
thin film materials.
The in-plane magnetoelastic coupling coefficient b
or the magnetostriction l can be measured by the
common cantilevered substrate technique using the
formula of du Tre
´
molet de Lachesserie and Peuzin,
resulting in:
b ¼
a
L
h
2
s
h
f
E
s
6ð1 þ n
s
Þ
; l ¼
bð1 þ n
f
Þ
E
f
where a is the deflection angle of the cantilever as a
function of applied field, L is the free length of the
cantilever, E
s
and n
s
are the Young’s modulus and
Poisson’s ratio for the substrate, and h
s
, h
f
are the
thicknesses of the substrate and film, respectively.
In the following sections, amorphous, nanocrys-
talline and multilayered state-of-the-art giant mag-
netostrictive materials in thin film form with positive
and negative magnetostriction and applications of
these materials are discussed.
1. Amorphous Films
Use of amorphous materials is an important
approach to lowering macroscopic anisotropy. In
amorphous magnetic rare earth–iron alloys, the con-
tribution of the rare earth–iron interaction results in
the formation of a sperimagnetic structure with an
ordering temperature above room temperature. In
the case of positive magnetostrictive materials, TbFe
thin films have been fabricated in a wide composition
1254
Thin Films: Giant Magnetostrictive