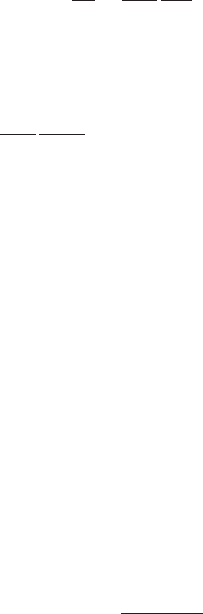
dŁ
dt
¼
k
rC
p
d
2
Ł
dx
2
(7:59)
Adopting a finite-element approach, Equation (7.59) can be written
Ł(x, t þ ˜ t) ¼ Ł(x, t) þ
k
rC
p
˜t
(˜x)
2
[Ł(x þ ˜x, t) þ Ł(x ˜x, t) 2Ł(x , t)] (7:60)
Substituting values of k ¼ 36 W=m per 8K, C
p
¼ 502 J=kg per 8K and r ¼
7085 kg=m
3
for Grade 450 spheroidal graphite cast iron yields a value for the
thermal diffusivity Æ ¼ k=(rC
p
)of1:01 3 10
5
m
2
=s. If the time increment, ˜t,is
selected at 0.025 s and the element thickness is taken as 1.005 mm, then Equation
(7.60) simplifies to
Ł(x, t þ ˜t) ¼ 0:25[Ł(x þ ˜x, t) þ Ł(x ˜x, t) þ 2Ł(x, t)] (7:61)
This equation can be used to calculate the temperature distribution across the brake
disc, starting with a uniform distribution and imposing suitable increments at the
braking surfaces at the boundaries. The behaviour at the boundaries is simpler to
follow through if they are treated as planes of symmetry like the disc mid-plane,
with imagined discs flanking the real one. The temperature increment at the
boundary at each time step, which is added to that calculated from Equation (7.61),
is given by
˜Ł
0
¼
2Tø(t)˜t
rC
p
S
(7:62)
where T is the braking torque (assumed constant), ø(t) is the disc rotational speed
at time t, and S is the area swept out by the brake pad (or pads) on one side of the
disc. For a disc diameter D and pad width w, S is (D w)w. The factor 2 is
required because heat is assumed to flow into the imagined disc as well as into the
real one. Hence the initial temperature build up can be calculated as illustrated in
Table 7.6, taking an arbitrary value of ˜Ł
0
of 408C. (The gradual reduction in ˜Ł
0
over time due to deceleration is ignored here for simplicity.)
The brake-disc surface temperature rise is found to be a minimum when the ratio
of the braking torque to the maximum aerodynamic torque is about 1.6. As the ratio
is reduced below this value, the exte nded stopping time results in more ene rgy
being abstracted from the wind, so temperatur es begin to rise rapidly. On the other
hand, the maximum brake temperature is relatively insensitive to increases in the
ratio above 1.6. The variation in maximum brake-disc surface temperature with
braking torque is illustrated for the emergency braking of a stall-regulated machine
following an overspeed in Figure 7.35, where the continuous line gives the surface
temperature rise calculated by the finite-element method outlined above. It tran-
spires that the maximum temperature rise can be estimated quite accurately by the
following empirical formula
446 COMPONENT DESIGN