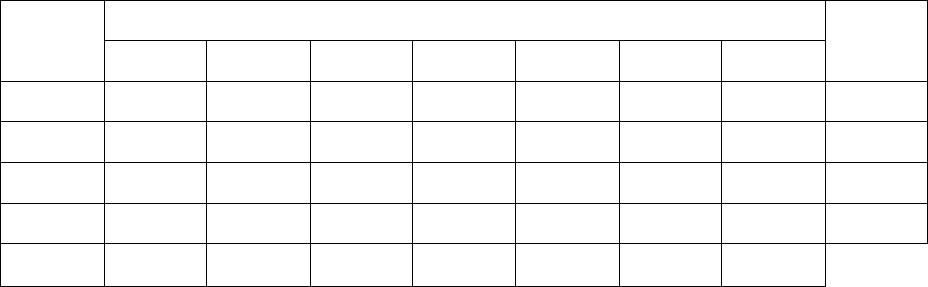
87
Следует отметить, что попытки получить аналогичным образом решения для трех
станков и более не увенчались успехом, за исключением отдельных частных случаев. При
переходе к общему случаю сложность задачи резко возрастает, что объясняется ее комби-
наторной природой, обуславливающей
n
m )!( вариантов, где m − число деталей, n − число
станков. При этом функция резко возрастает, так, например, 10!=3628800, а 11!=39916800.
Тем не менее, анализ алгоритма Джонсона позволил сформулировать ряд практиче-
ских рекомендаций (правил), которые можно распространить и на случай, когда число
станков превышает 2. В частности, при составлении расписания обработки деталей следу-
ет [17]:
1) обрабатывать раньше те детали, у которых время обработки на первом станке
минимально;
2) обрабатывать раньше те детали, у которых время обработки на последнем стан-
ке максимально;
3) обрабатывать раньше те детали, для которых «узкое место» (т.е. станок, на ко-
тором обработка данной детали занимает наибольшее время) находится дальше
от начала процесса обработки;
4) пропускать вперед детали, для которых общая продолжительность обработки на
всех станках максимальна.
Пример 6.5. В мебельном цехе деревообрабатывающего комбината изготавливают-
ся футляры для настенных и настольных часов, которые имеют следующие семь пронуме-
рованных деталей (m=7): 1 − вертикальный брусок двери; 2, 3 и 4 − нижний, средний и
верхний бруски дверки; 5 − нижняя доска; 6 − штанга; 7 − планка. Перечисленные детали
должны пройти последовательную обработку на следующих четырех (также пронумеро-
ванных) станках (n=4): 1 − рейсмусовом; 2 − фуговальном; 3 − торцовочном; 4 − фрезер-
ном. В табл. 6.5 приведена длительность обработки (в минутах) каждой детали на каждом
из станков.
Таблица 6.5. Длительность обработки деталей на станках
Длительность обработки детали №, мин. №
станка
1 2 3 4 5 6 7
Σ, мин.
1 9 4 5 6 3 2 1 30
2 5 2 8 12 4 1 1 33
3 7 6 10 8 1 2 3 37
4 6 3 4 5 2 3 4 27
Σ, мин.
27 15 27 31 10 8 9
В соответствии с рассмотренными выше правилами можно рекомендовать сле-
дующие варианты запуска деталей в обработку (табл. 6.6). В случае, когда рассматривае-
мое правило не позволяет определить очередность обработки каких-либо двух деталей,
требуется обращение к одному из предыдущих правил.
Для определения общей длительности обработки деталей для каждой из последова-
тельностей можно построить диаграмму Ганта. В результате оказывается, что наимень-
шую длительность обработки (56 мин.) дает правило №1, следующее по длительности (57
мин.) − правило №3.
Нижняя (т.е. минимальная) оценка для общей длительности обработки всех деталей
может быть получена путем сравнения суммарной длительности обработки деталей на
каждом из станков (последняя графа табл. 6.5). Очевидно, что полная длительность обра-