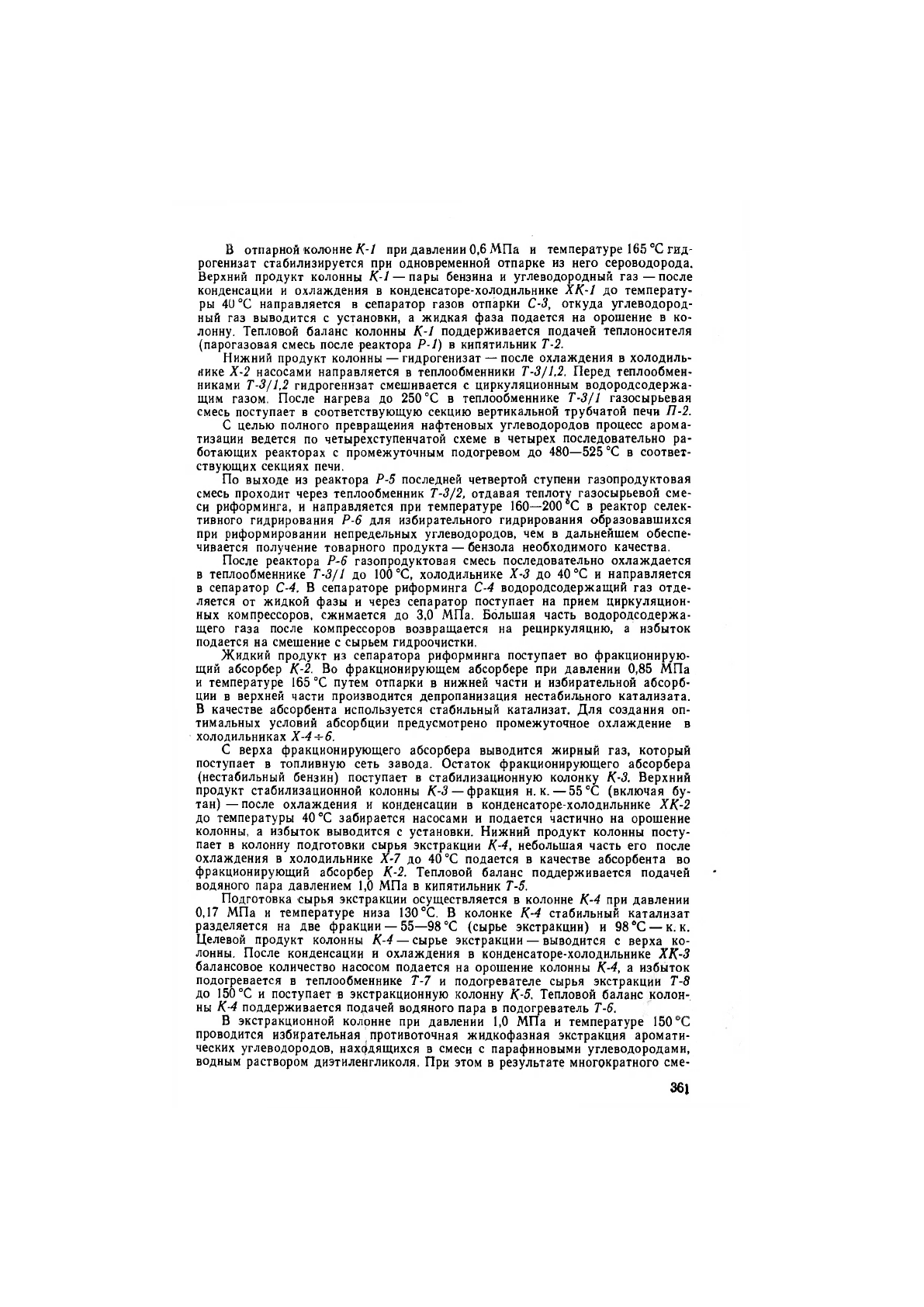
В отпарной колонне К-1 при давлении 0,6 МПа и температуре 165 °С гид-
рогенизат стабилизируется при одновременной отпарке из него сероводорода.
Верхний продукт колонны К-1 — пары бензина и углеводородный газ—после
конденсации и охлаждения в конденсаторе-холодильнике ХК-1 до температу-
ры 40 °С направляется в сепаратор газов отпарки С-3, откуда углеводород-
ный газ выводится с установки, а жидкая фаза подается на орошение в ко-
лонну. Тепловой баланс колонны К-1 поддерживается подачей теплоносителя
(парогазовая смесь после реактора Р-1) в кипятильник Т-2.
Нижний продукт колонны — гидрогенизат — после охлаждения в холодиль-
нике Х-2 насосами направляется в теплообменники Т-3/1.2. Перед теплообмен-
никами Т-3/1,2 гидрогенизат смешивается с циркуляционным водородсодержа-
щим газом. После нагрева до 250 °С в теплообменнике Т-3/1 газосырьевая
смесь поступает в соответствующую секцию вертикальной трубчатой печи П-2.
С целью полного превращения нафтеновых углеводородов процесс арома-
тизации ведется по четырехступенчатой схеме в четырех последовательно ра-
ботающих реакторах с промежуточным подогревом до 480—525 °С в соответ-
ствующих секциях печи.
По выходе из реактора Р-5 последней четвертой ступени газопродуктовая
смесь проходит через теплообменник Т-3/2, отдавая теплоту газосырьевой сме-
си риформинга, и направляется при температуре 160—200 С в реактор селек-
тивного гидрирования Р-6 для избирательного гидрирования образовавшихся
при риформировании непредельных углеводородов, чем в дальнейшем обеспе-
чивается получение товарного продукта — бензола необходимого качества.
После реактора Р-6 газопродуктовая смесь последовательно охлаждается
в теплообменнике Т-3/1 до 100 °С, холодильнике Х-3 до 40°С и направляется
в сепаратор С-4. В сепараторе риформинга С-4 водородсодержащий газ отде-
ляется от жидкой фазы и через сепаратор поступает на прием циркуляцион-
ных компрессоров, сжимается до 3,0 МПа. Большая часть водородсодержа-
щего газа после компрессоров возвращается на рециркуляцию, а избыток
подается на смешение с сырьем гидроочистки.
Жидкий продукт из сепаратора риформинга поступает во фракционирую-
щий абсорбер К-2. Во фракционирующем абсорбере при давлении 0,85 МПа
и температуре 165 °С путем отпарки в нижней части и избирательной абсорб-
ции в верхней части производится депропанизация нестабильного катализата.
В качестве абсорбента используется стабильный катализат. Для создания оп-
тимальных условий абсорбции предусмотрено промежуточное охлаждение в
холодильниках Х-4 + 6.
С верха фракционирующего абсорбера выводится жирный газ, который
поступает в топливную сеть завода. Остаток фракционирующего абсорбера
(нестабильный бензин) поступает в стабилизационную колонку К-3. Верхний
продукт стабилизационной колонны К-3 — фракция н. к. — 55 °С (включая бу-
тан) — после охлаждения и конденсации в конденсаторе-холодильнике ХК-2
до температуры 40 °С забирается насосами и подается частично на орошение
колонны, а избыток выводится с установки. Нижний продукт колонны посту-
пает в колонну подготовки сырья экстракции К-4, небольшая часть его после
охлаждения в холодильнике Х-7 до 40 °С подается в качестве абсорбента во
фракционирующий абсорбер К-2. Тепловой баланс поддерживается подачей
водяного пара давлением 1,0 МПа в кипятильник Т-5.
Подготовка сырья экстракции осуществляется в колонне К-4 при давлении
0,17 МПа и температуре низа 130 °С. В колонке К-4 стабильный катализат
разделяется на две фракции — 55—98 °С (сырье экстракции) и 98 °С — к. к.
Целевой продукт колонны К-4 — сырье экстракции — выводится с верха ко-
лонны. После конденсации и охлаждения в конденсаторе-холодильнике ХК-3
балансовое количество насосом подается на орошение колонны К-4, а избыток
подогревается в теплообменнике Т-7 и подогревателе сырья экстракции Т-8
до 150 °С и поступает в экстракционную колонну К-5. Тепловой баланс колон-
ны К-4 поддерживается подачей водяного пара в подогреватель Т-6.
В экстракционной колонне при давлении 1,0 МПа и температуре 150
проводится избирательная противоточная жидкофазная экстракция аромати-
ческих углеводородов, находящихся в смеси с парафиновыми углеводородами,
водным раствором диэтиленгликоля. При этом в результате многократного сме-
361