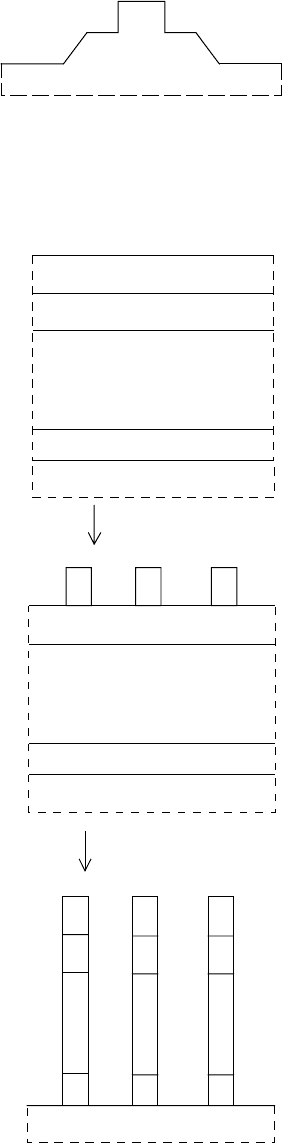
Dry etching of GaAs and related alloys
to produce the desired angled structures. The type of profile that
results from a two-step etch using first a straight-wall photores-
ist and then a reflowed photoresist is shown in FIGURE 5.14.
The angled wall of the second mesa allows good metal contacts to
be made from the top of the angle-walled mesa to bond pads on
the lower etched surface.
FIGURE 5.14 Angled-wall
double mesa structure from
two-step etch with first
straight-wall resist and then
reflowed resist.
To avoid thermal problems for longer etches, one or more
cool-down steps may be included during the etch process. With
source gases that require plasma dissociation to produce appre-
ciable etching, this can simply involve stopping the plasma
discharge while the gases continue to flow for a few minutes.
A good starting time for determining what is required for adequate
cooling is about 5 min. The final etch depth and profile will be
largely determined by the time the plasma is on. For gases that
can do appreciable etching without plasma activation, such a cool-
down step might allow an undesirable amount of isotropic etching,
resulting in degraded profiles.
The required thickness of a resist, especially a metal resist, will
be defined largely by its sputtering rate. Metal resists or multilayer
photoresist/dielectric resist stacks are used in processes such as
RIBE for deep, narrow features where conventional photoresist
cannot withstand the prolonged high-energy etching required.
One solution to the problem of excessively rapid photoresist
erosion is the use of PR/dielectric stacks as trilevel or quadlevel
resists. A quadlevel resist that works well for RIBE andICP etching
is shown in FIGURE 5.15. An organic liftoff layer, such as poly-
methylglutarimide (PMGI), is applied to the substrate. The main
PR mask layer is then applied to the PMGI and extensively baked
(60 min at 190
◦
C followed by 60 min at 250
◦
C). A half micro-
metre of a dielectric such as Si
x
N
y
is applied to this hard-baked
PR. Another PR layer that is used for patterning the dielectric is
applied on top of the stack.
substrate
lift-off layer
hard-baked resist
dielectric
imaging resist
substrate
photolithography
substrate
lift-off layer
hard-baked resist
dielectric
oxygen plasma
(a)
(b)
(c)
FIGURE 5.15 Quad-level mask.
The desired pattern is photolithographically defined in the top
PR layer. This pattern is then etched into the Si
x
N
y
using an SF
6
/O
2
RIE process. The pattern is then transferred into the hard-baked PR
and liftoff layer using an ECR or ICP etch with O
2
and Ar. Fol-
lowing the completion of etching the III–V substrate (typically by
RIBE), what remains of the resist stack can be removed by soaking
in a solvent that releases the liftoff layer from the surface.
Nickel is often a good choice for a metal resist due to its
relatively high resistance to sputtering and its tendency not to
redeposit on the wafer surface when it is sputtered. Redepos-
ition of sputtered material, either resist or low-volatility III–V
products, can produce micromasking. The result is very rough
etching, producing a “grassy” surface that often looks black or
“burned” upon inspection.
173