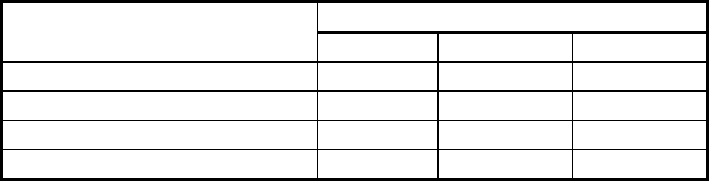
two sets of test specimens can be obtained during one test. Using reference materials mixed in with the other
specimens will also provide information on whether the jaw crusher is performing within specified limits. An
advantage in using the nonstandard method is that it allows the specimen materials to be matched according to
their hardness so that the wear rates from both sets of materials will be similar in magnitude. Doing this
eliminates the possibility of a softer material wearing at an accelerated rate, skewing the ratio with respect to
the reference material. Another advantage of the jaw crusher is that the abrasive used for the test can be exactly
matched to the field application. Table 7 gives some representative data for different ore types.
Table 7 Jaw crusher wear data for ferrous alloys using different ores
Volume loss, mm
3
/kg
Alloy and
designation
Quartzite
Limestone
Granite
Stainless steel, type 304 27.7 ± 4.9
6.3 ± 0.1
6.3 ± 1.0
Low-alloy steel, ASTM A 514
23.9 ± 3.3
6.1 ± 1.0
6.9 ± 0.5
Low-alloy steel, REM 500 11.3 ± 1.5
1.2 ± 0.0(2)
0.8 ± 0.0(3)
Low-alloy steel, AISI 4340 13.8 ± 1.4
1.5 ± 0.2 0.9 ± 0.1
Erosion Testing
Solid particle erosion is the loss of material from repeated impacts by small, solid particles. Erosion by solid
particles using gas jets is a standard ASTM test method, G 76 (Ref 50), which provides specific guidelines on
erosion testing. This test is briefly discussed here because it is another example of an impact-abrasion process.
When referring to solid particle erosion, it is implied that the erosive particle size is relatively small (tens to
hundreds of micrometers), and particle velocities are relatively high (i.e., >1 m/s but usually in the range of ten
to several hundred m/s).
Material removal via erosion is a complicated process, dependent upon the incident angle of impact. For
example, at incident angles approaching 90°, material is lost in a sequential process of platelet formation and
detachment. In this process, material is extruded from the impact crater in the form of a lip or platelet through
plastic deformation. These lips or platelets are subsequently deformed by further impacts, leading eventually to
detachment as a wear flake. At impact angles of less than 20°, the abrasive particles form shallow craters and
grooves as they impact and move across the surface. Material removal is via a process of plastic deformation,
extrusion, microplowing, and microcutting, where any extruded material from an impact or plowed groove is
subsequently detached as a result of further particle impact (Ref 51, 52).
As in scratch testing, erosion testing using either single or multiple particles of controlled size and mass (e.g., 1
mm, or .04 in., diameter WC-Co spheres) provides information on the micromechanics of damage and mass
loss mechanisms in homogeneous and complex materials. The degree of damage from single impacts can be
determined using surface profilometry measurements and scanning electron microscopy. In multiple impact
solid particle erosion using controlled particles, mass loss is determined by weighing. For the interested reader,
the following references describe the procedure used in single- and multiple-impact particle erosion and the
methods used to measure damage (Ref 53, 54). These tests require consistent specimen preparation of the
samples in order to obtain representative mass loss measurements and to assess damage.
Contrasted with the controlled erosion tests just described are those tests that are related directly to applications
such as erosion in coal combustion power plants and gas turbines in coal-fired combined cycle power
generation (Ref 55, 56, 57). In these cases, the effects of environment, especially temperature and atmosphere,
complicate the analysis process.
Impact Abrasion Wear Testing
Bond (Ref 58) developed a laboratory scale test to accurately simulate the wear conditions that exist in the
impact crushing of ores (both soft and hard) by impact hammers and blow bars. The rationale for the
development of the test apparatus was to be able to predict the wear, and hence the energy consumption, that
occurred in the crushing and grinding of ore (Ref 59, 60). However, this test is applicable to any wear process
in which impact occurs during the abrasion process. Impact-abrasion testing can be performed in an impeller-