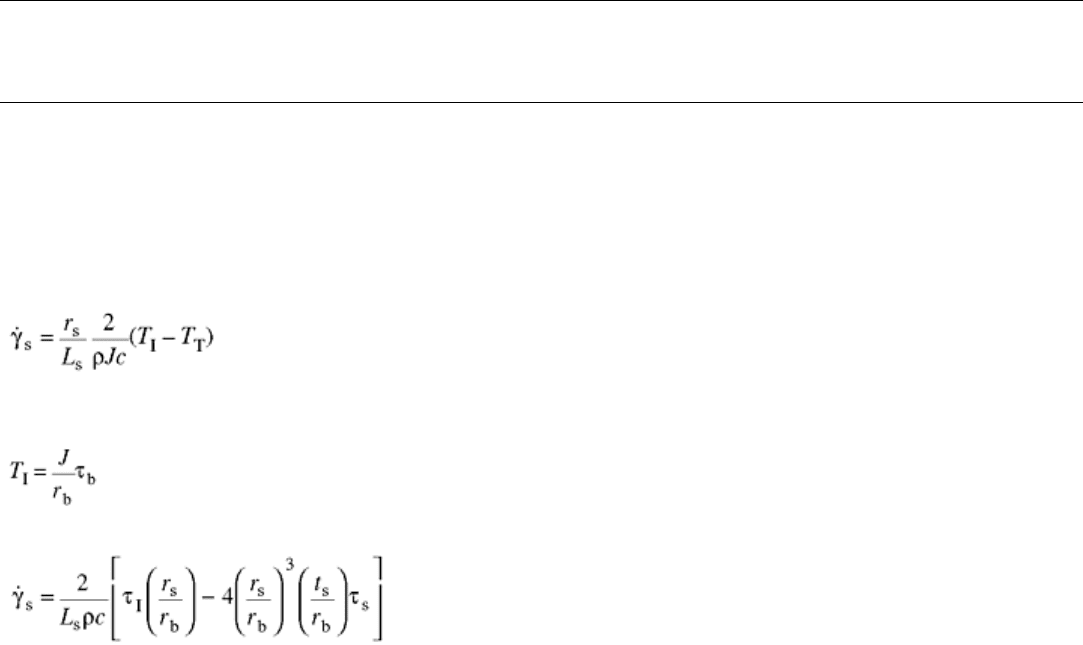
Torsional Kolsky Bar Testing
Amos Gilat, The Ohio State University
Application Areas
Limitations on Strain Rate. The practical upper limit on the strain rate that can be achieved in tests with the
torsional Kolsky bar is about 10
4
s
-1
. This can be observed by combining Eq 4 and 5 to write the strain rate as a
function of the reflected torque, and substituting T
I
- T
T
for -T
R
, which gives:
(Eq 13)
where T
I
is the incident torque and T
T
is the transmitted torque. For a solid circular cylinder, the incident torque
is related to the shear stress in the incident bar (τ
b
) by:
(Eq 14)
Using Eq 11 and 14, the strain rate in the specimen can be obtained as:
(Eq 15)
Where τ
I
is the incident shear stress. From Eq 15, it is evident that the maximum strain rate is attained when the
quantity on the right side is maximized. One means is to make the specimen shorter, that is, to decrease L
s
.
However, with very short specimens, the end effects can become important; that is, the strain in the specimen
may never be uniform.
Because the second term in Eq 15 generally is small, another method of increasing the strain rate is to increase
the ratio r
s
/r
b
by decreasing the radius of the bar, or by increasing the mean radius of the specimen. The limiting
ratio of r
s
/r
b
that can be used is 1 because r
s
cannot be greater than r
b
without a significant change in the
impedance.
Yet another method of increasing the strain rate is to select a bar material with a high yield stress in order to
maximize τ
I
in Eq 15. This would appear to have an advantage because a much greater torque can be stored in
the bar. However, two other factors affect the selection of the bar material. First, the mass density, ρ, of the bar
material has to be considered. For example, the mass density of steel is about three times that of aluminum.
Thus, unless the steel has a yield stress that is more than three times that of aluminum, there will be no increase
in strain rate when using a steel bar. With this regard, a material with a high ratio of yield stress to density, such
as a titanium alloy, will theoretically maximize the strain rate. Secondly, the ability to clamp a high torque has
to be considered. As discussed earlier, it is difficult, if not impossible, to clamp a torque such that the shear
stress in the bar approaches the yield stress. High clamping pressures may also produce an axial pulse upon the
release of the clamp.
It is evident from Eq 15 that an increase in the diameter of the Kolsky bar will not increase strain rate
significantly. Increased diameter alters only the second term in Eq 15, which is considerably smaller than the
first term. From Eq 14, it is evident that, although optimum bar dimensions and material exist to achieve a
maximum strain rate, there is a physical limit of strain rate of about 10
4
s
-1
that is attainable.
The practical lower limit on strain rate in the Kolsky bar is about 10
2
s
-1
because a lower strain rate cannot be
held constant throughout the test. A constant value of strain rate requires that the magnitude of the reflected
pulse be held constant, and this in turn requires that the input pulse be considerably larger than that of the
transmitted pulse. Depending on the rate of work hardening of the specimen material, this imposes a lower limit
on the strain rate that can be attained with the Kolsky bar.
In practice, it is easiest to design a torsional Kolsky bar to reach a strain rate of about 10
3
s
-1
. This value is
easily doubled by shortening the specimen, or can be reduced by imposing less torque. Tests outside the range
of 500 to 2000 s
-1
require special consideration.