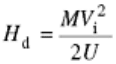
where the load is directly measured, these methods warrant measurement of incident velocity, V
i
, of the
indenter for determining the dynamic hardness, H
d
, as per the following equation (Ref 15, 16):
(Eq 1)
where M is the mass of the indenter and U is the unrelaxed volume of the indentation imprint on the specimen.
This relationship assumes that the ratio of decrease in indentation volume due to the elastic recovery to
unrelaxed volume is the same as the ratio of rebound velocity to incident velocity of a spherical ball. Another
assumption is that the resistance to indentation is constant throughout the deformation, but this assumption has
been questioned by several authors (Ref 16, 17). Moreover, it is difficult to control the loading duration in this
approach because it depends on the frictional properties and coefficient of restitution (which itself varies with
indenter velocity) between the specimen and the indenter. The loading duration and the strain rate during the
deformation are estimated (not directly measured) based on the energy absorbed to create the crater and the
rebound height of the indenter. Therefore, these rebound methods do not parallel the simplicity of the static
indentation test method where the indentation load and the contact time are directly measured to determine the
static indentation hardness.
Commercial devices, such as Equotip hardness testers, based on rebound techniques also have emerged in the
market (Ref 18). In this method, the hardness of a material is not determined, but a numerical measure called an
“Equotip hardness number,” which is proportional to the ratio of rebound velocity to impact velocity, is used to
represent the hardness. However, this number has not been correlated to the established hardness measures such
as Rockwell, Brinell, or Vickers hardness numbers.
Pendulum Method. Nobre and others (Ref 16) used a pendulum machine to investigate the surface resistance of
a ductile steel to impact by hard ceramic balls. The pendulum is equipped with a piezoelectric transducer that
enables the history of impact as well as the velocity of pendulum before and after the impact to be obtained.
Obviously, the impact force or indentation load can be controlled by the amplitude of displacement from the
mean position where the specimen is situated. Similar to the rebound method, the duration of contact with the
specimen cannot be controlled in this technique because it depends on the resistance offered by the specimen
material, which is a function of the geometry and materials properties. Therefore, assumptions similar to those
in the rebound technique also should be made in this method to determine the dynamic hardness, and all these
factors render this technique different from the method for static hardness determination.
The basic disadvantage of these methods is that neither the indentation load nor the duration of the indentation
are precisely controlled a priori. This makes the determination of dynamic hardness nontrivial compared with
the static hardness testing where the hardness is determined by a simple relationship based on the measured
load and the size of the indentation imprint. Therefore, a technique that parallels the method for static
indentation hardness determination, where the indentation load and the size of indentation are directly
measured, can be of significant practical value for comparison of the static and dynamic hardness
measurements and for determination of strain-rate-sensitive properties of materials.
References cited in this section
1. D. Tabor, A Simple Theory of Static and Dynamic Hardness, Proc. R. Soc. (London), Vol 192A, 1948,
p 247–274
13. D.B. Marshall, A.G. Evans, and Z. Nisenholz, Measurement of Dynamic Hardness by Controlled Sharp-
Projectile Impact, J. Am. Ceram. Soc., Vol 66 (No. 8), 1983, p 580–585
14. G. Sundararajan and P.G. Shewmon, The Use of Dynamic Impact Experiments in the Determination of
the Strain Rate Sensitivity of Metals and Alloys, Acta Metall., Vol 31, 1983, p 101–109
15. Y. Tirupataiah and G. Sundararajan, A Dynamic Indentation Technique for the Characterization of the
High Strain Rate Plastic Flow Behavior of Ductile Metals and Alloys, J. Mech. Phys. Solids, Vol 39,
1991, p 243–271