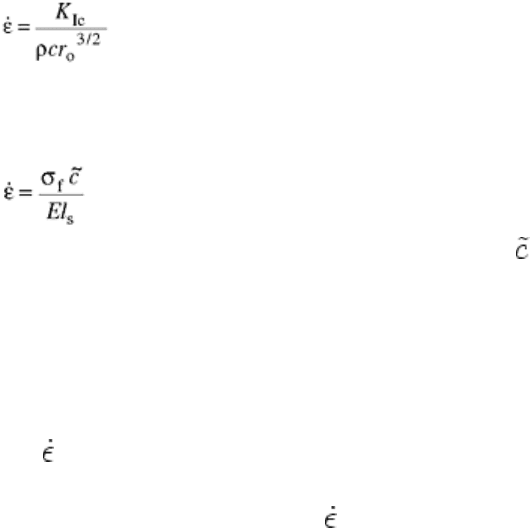
Mechanisms of Brittle Failure Under High-Strain-Rate Loading. It has been well established that processing-
induced microstructural inhomogeneities, such as inclusions, grain boundary impurities, second phases, triple
junctions, and pores are mainly responsible for the nucleation of microcracks that lead to fracture in ceramics
(Ref 14, 16, 17). However, the difference in the characteristics of crack growth from these inhomogeneities is
mainly responsible for the rate-sensitive nature of fracture strength in brittle materials. At low strain rates,
typically below 100/s, both sintered and hot-pressed ceramics, in general, do not exhibit rate-sensitive failure
strength. This behavior has been attributed to unstable crack growth from inhomogeneities and their
instantaneous coalescence, which inhibits any subcritical crack growth.
At high strain rates, beyond a critical strain rate, both sintered and hot-pressed ceramics exhibit a high rate-
sensitive fracture stress due to inertia-dominated crack growth (Ref 14, 15, 17); that is, as the loading rate
increases, the time available for a crack to initiate and grow reduces. The inertia associated with the crack-
growth acceleration will inhibit early fracture initiation while the applied stress continues to rise rapidly, thus
elevating the compressive failure strength under dynamic loads. The critical strain rate at which transition from
the rate-insensitive (unstable) to rate-sensitive (inertia dominated) crack growth in microcracking solids has
been found to depend on material properties. Grady and Lipkin (Ref 18) proposed the following relationship for
the transitional strain rate:
(Eq 18)
where K
Ic
is the fracture toughness, ρ is material density, c is wave velocity, and r
o
is the average initial
microcrack size, which is typically assumed to be the same as the grain size in ceramics. Ravichandran and
Subhash (Ref 17) proposed this equation:
(Eq 19)
where σ
f
is the quasi-static compressive strength and is the characteristic crack velocity which is taken as the
speed at which inertia effects become significant, that is, when the crack velocity reaches approximately 0.2 of
shear wave velocity. Equation 19 is a modified version of the equation proposed by Lankford (Ref 14) where
the length is replaced by radius of the specimen and by shear wave speed. Both Eq 18 and 19 predict the
transitional strain rate to be between 1200 and 1500/s.
In the inertia-dominated (high-strain-rate) regime, the relationship between the compressive fracture strength,
σ
f
, and strain rate at fracture for a variety of brittle ceramics has been found to follow a relationship (Ref 18):
σ
f
α
1/3
(Eq 20)
A micromechanical damage model for brittle materials developed by Ravichandran and Subhash (Ref 17)
shows a similar relationship, σ
f
α
n
, where n ranges from ¼ to ⅓. The value of n depends on the relationship
describing the dynamic fracture toughness as a function of crack speed. Although the relationship discussed
previously has been found to reasonably represent the failure behavior of coarse-grained ceramics, recent
experimental results on fine-grained, high-purity ceramics revealed a complete absence of such a transitional
strain rate (Ref 19, 20). In these ceramics, the uniaxial compressive fracture strength increased linearly with
strain rate in the range between 10
-3
and 10
5
/s. This behavior has been attributed to fine grain size, significant
reduction in the process induced flaws, and elimination of inhomogeneities during processing, all of which
resulted in enhanced dislocation activity and microshear banding similar to those observed in ductile metals.
Damage Evolution. One of the major characteristics of crack growth during uniaxial compressive loading of
brittle materials is that crack growth occurs in a direction parallel to the loading axis. On a plane perpendicular
to the loading axis, the cracks can be randomly oriented, thereby making the specimen transversely isotropic.
The problem of tensile crack growth from preexisting microcracks has been analyzed in detail (Ref 21, 22).
Under uniaxial compressive loading, tensile cracks nucleate from the preexisting flaws in the direction of
maximum tensile stress. The major difference in crack growth under static and dynamic loading is that in static
loading, a single crack typically dominates the fracture behavior. This is because once the stress required for
crack initiation is reached, the weakest crack starts to grow first, and the stored elastic energy continues to
provide the necessary driving force for unstable crack growth to continue and cause eventual failure of the
specimen. Here the rate of loading is extremely slow compared to the crack growth rate, and, hence, once crack
growth is initiated it cannot be controlled. In the case of dynamic loading, the inertia associated with the crack
tip opening delays the crack growth while the applied stress rises much more rapidly beyond that required for