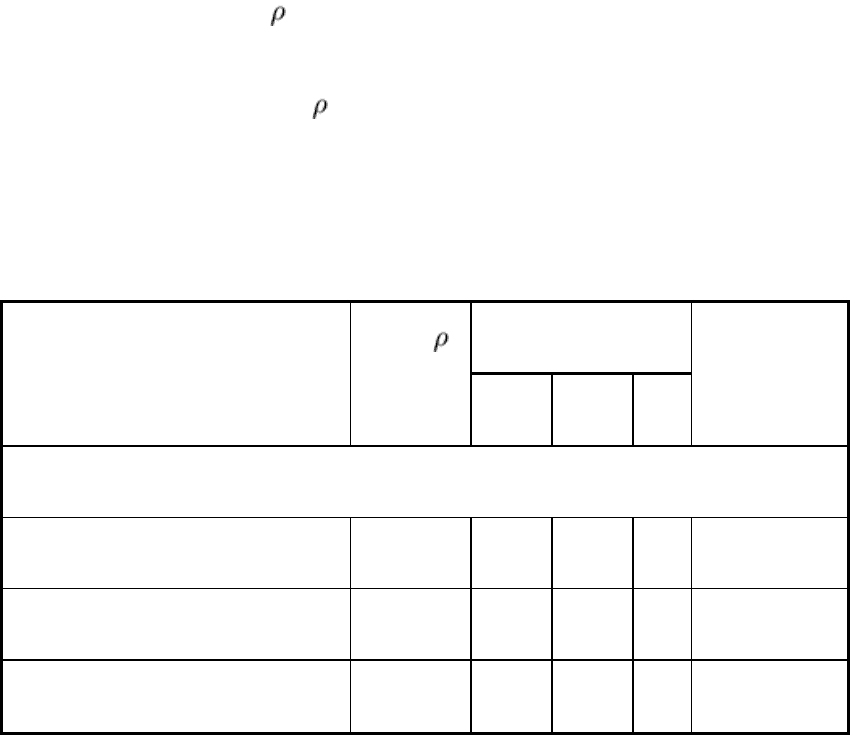
Sensitivity, or the ability of an ultrasonic inspection system to detect a very small discontinuity, is generally increased by
using relatively high frequencies (short wavelengths). Resolution, or the ability of the system to give simultaneous,
separate indications from discontinuities that are close together both in depth below the front surface of the testpiece and
in lateral position, is directly proportional to frequency band-width and inversely related to pulse length. Resolution
generally improves with an increase of frequency.
Penetration, or the maximum depth (range) in a material from which useful indications can be detected, is reduced by the
use of high frequencies. This effect is most pronounced in the inspection of metal that has coarse grain structure or minute
inhomogeneities, because of the resultant scattering of the ultrasonic waves; it is of little consequence in the inspection of
fine-grain, homogeneous metal.
Beam spread, or the divergence of an ultrasonic beam from the central axis of the beam, is also affected by frequency. As
frequency decreases, the shape of an ultrasonic beam increasingly departs from the ideal of zero beam spread. This
characteristic is so pronounced as to be observed at almost all frequencies used in inspection. Other factors, such as the
transducer (search unit) diameter and the use of focusing equipment, also affect beam spread; these are discussed in
greater detail in the sections "Beam Spreading" and "Acoustic Lenses" in this article. Sensitivity, resolution, penetration,
and beam spread are largely determined by the selection of the transducer and are only slightly modified by changes in
other test variables.
Acoustic Impedance. When ultrasonic waves traveling through one medium impinge on the boundary of a second
medium, a portion of the incident acoustic energy is reflected back from the boundary while the remaining energy is
transmitted into the second medium. The characteristic that determines the amount of reflection is the acoustic impedance
of the two materials on either side of the boundary. If the impedances of the two materials are equal, there will be no
reflection; if the impedances differ greatly (as between a metal and air, for example), there will be virtually complete
reflection. This characteristic is used in the ultrasonic inspection of metals to calculate the amounts of energy reflected
and transmitted at impedance discontinuities and to aid in the selection of suitable materials for the effective transfer of
acoustic energy between components in ultrasonic inspection systems.
The acoustic impedance for a longitudinal wave, Z
l
, given in grams per square centimeter-second, is defined as the
product of material density, , given in grams per cubic centimeter, and longitudinal wave velocity, V
l
, given in
centimeters per second:
Z
l
= V
l
(Eq 2)
The acoustic properties of several metals and nonmetals are listed in Table 1. The acoustic properties of metals and alloys
are influenced by variations in structure and metallurgical condition. Therefore, for a given testpiece the properties may
differ somewhat from the values listed in Table 1.
Table 1 Acoustic properties of several metals and nonmetals
Sonic velocities, 10
5
cm/s
Material
Density ( ),
g/cm
3
V
l
(a)
V
t
(b)
V
s
(c)
Acoustic
impedance (Z
1
)
(d)
,
10
6
g/cm
2
· s
Ferrous metals
Carbon steel, annealed 7.85 5.94 3.24 3.0
4.66
Alloy steel
Annealed
7.86 5.95 3.26 3.0
4.68