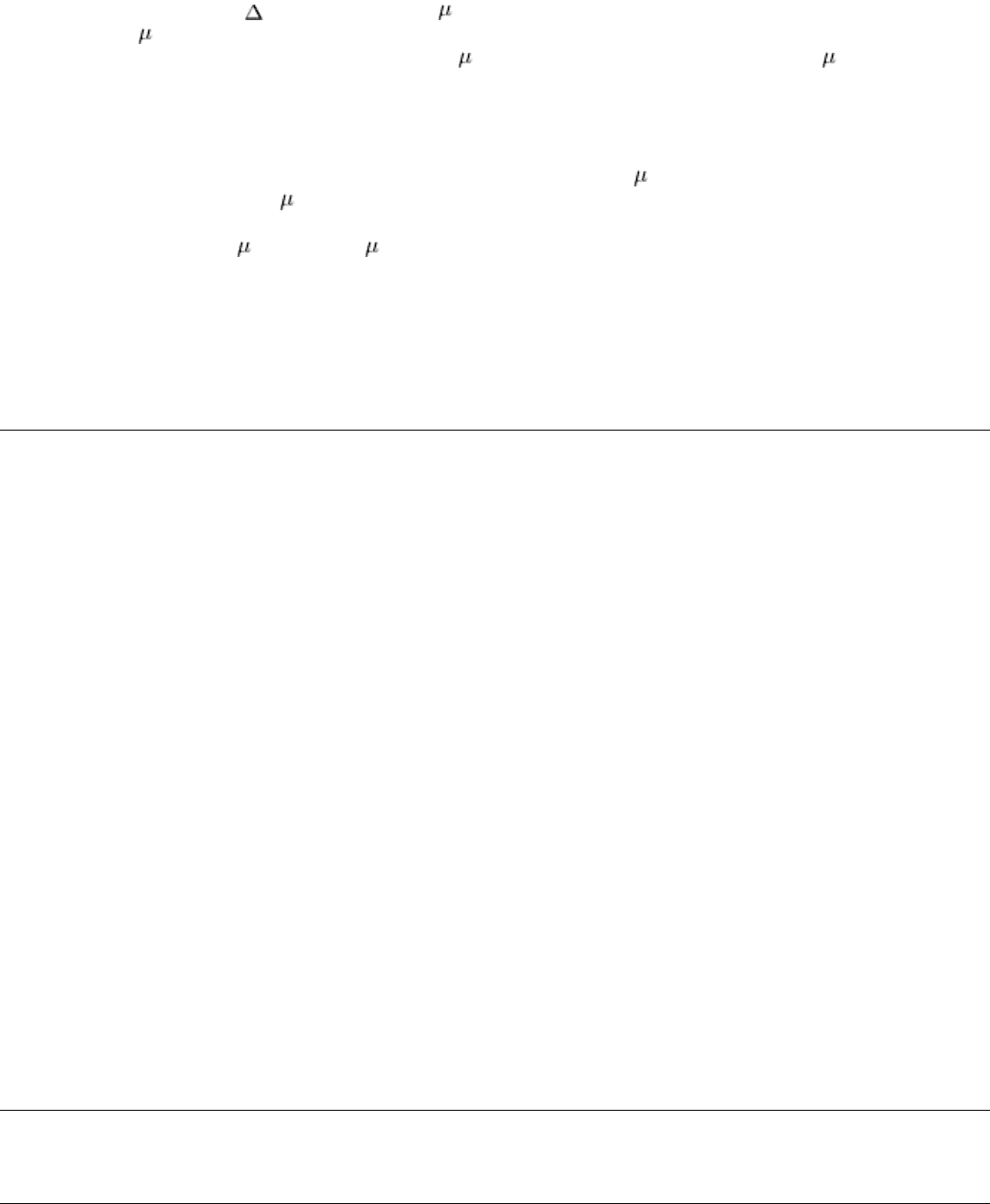
The flaws used are straight artificial grooves, cutting the samples across their entire length. The parameter investigated is
the frequency of the resonance peak. The results for aluminum and stainless steel are comparable. The differences
between scalar analysis of the aluminum and the Armco iron were significant.
The lift-off effect is basically different for the aluminum and the Armco iron but the same for the aluminum and the
stainless steel. For a lift-off, h, of more than 300 m (0.012 in.), the frequency remains stable for aluminum, while
from 300 to 100 m (0.012 to 0.004 in.), the frequency increases from 4014 to 4024 MHz. For Armco iron, the frequency
increases almost exponentially from 3800 MHz at 600 m (0.024 in.) lift-off to 4300 MHz at 100 m (0.004 in.). The
frequency variation in iron is due to the variation of the space between the magnetic and the metal. In the nonmagnetic
metals, the frequency variation is due to the eddy currents in the metal.
In the configurations illustrated in Fig. 39 and 40, the sensitivity of the frequency measurement is 100 kHz, mostly
limited by instabilities. The graph of frequency shift caused by a 100 × 100 m (0.004 × 0.004 in.) flaw in each of the
three metals with a lift-off of 100 m (0.004 in.) is smallest for aluminum, medium for the stainless steel, and largest for
the Armco iron. The values of frequency shift are 4 MHz for aluminum, 12 MHz for stainless steel, and 27 MHz for
Armco iron. Flaws of 10 × 5 m (400 × 200 in.) were lost in the background for all three materials.
The experiments confirmed that FMR probes have better sensitivity to flaws for ferromagnetic materials than for
nonmagnetic metals. On nonmagnetic metals, the frequency shift is due to eddy currents, while in ferromagnetic metals,
the frequency shift is caused by a modification of the bias field by the flaw. Because a frequency shift of 0.1 MHz can be
measured, a field variation of 0.05% can be detected.
References cited in this section
34.
B.A. Auld, F. Muennemann, and D.K. Winslow, "Observation of Fatigue-
Crack Closure Effects with the
Ferromagnetic-
Resonance Probes," G.L. Report 3233, E.L. Ginzton Laboratory, Stanford University, March
1981
35.
B.A. Auld, et al., Surface Flaw Detection With Ferromagnetic Resonance Probes, in Proceedings o
DARPA/AFML Review of Progress in Quantitative NDE
(La Jolla, CA), Defense Advanced Research
Projects Agency, July 1980
36.
B.A. Auld, New Methods of Detection and Characterization of Surface Flaws, in
DARPA/AFML Review of Progress in Quantitative NDE
(Cornell University), Defense Advanced Research
Projects Agency, June 1977
37.
B.A. Auld, et al., Surface Flaw Detection With Ferromagnetic Resonance Probes, in
DARPA/AFML Review of Progress in Quantitative NDE (La Jolla, CA),
Defense Advanced Research
Projects Agency, July 1978
38.
B.A. Auld, et al., Surface Flaw Detection With Ferromagnetic Resonance Probes, in
DARPA/AFML Review of Progress in Quantitative NDE
(La Jolla, CA), Defense Advanced Research
Projects Agency, July 1979
39.
B.A. Auld and D.K. Winslow, Microwave Eddy Current Experiments With Ferromagnetic Probes, in
Current Characterization of Material and Structures,
STP 722, G. Birnbaum and G. Free, Ed., American
Society for Testing and Materials, 1981, p 348-366
40.
A.F. Harvey, Properties and Applications of Gyromagnetic Media, in Microwave Engineering,
Press, 1963, p 352-358
41.
S. Segaline, et al.,
Application of Ferromagnetic Resonance Probes to the Characterization of Flaws in
Metals, J. Nondestr. Eval., Vol 4 (No. 2), 1984, p 51-58
Microwave Inspection
William L. Rollwitz, Southwest Research Institute