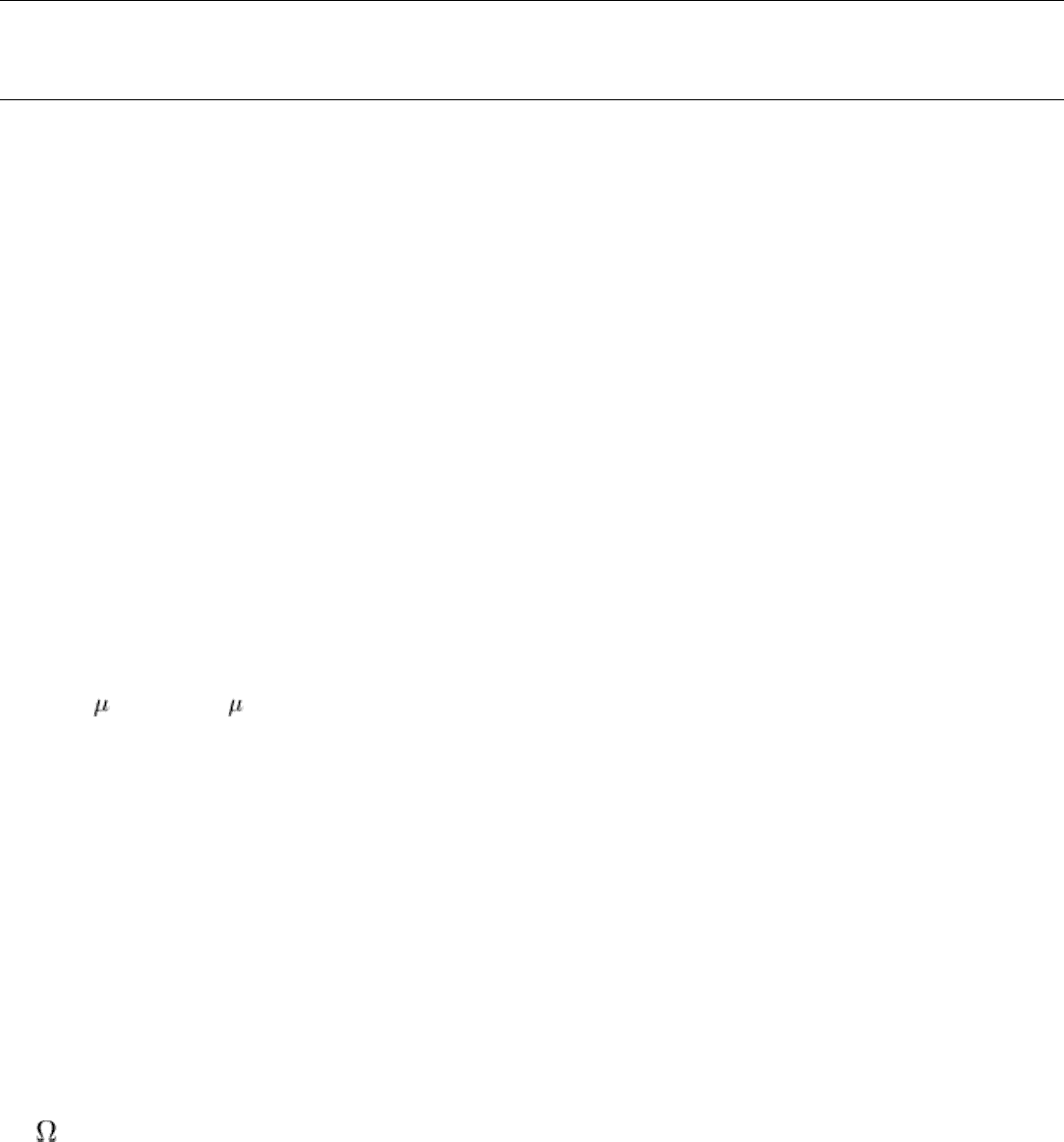
macroscopic level. The direction of glass fibers can be readily determined. The direction of the fibers in paper can also be
detected with linearly polarized microwaves and antenna rotation.
Fiber-matrix composites have also been measured for directionality. One instance was a multiple-ply composite having a
fiberglass-resin matrix and unidirectional boron filaments. The boron filaments, approximately 0.13 mm (0.005 in.) in
diameter, contained a tungsten-fiber center (0.013 mm, or 0.0005 in., in diameter) onto which the boron had been
deposited. Being electrically conductive, the overall composite acted on the microwaves very much like a diffraction
grating. Alignment shifts of only a few degrees were detected easily by monitoring either the reflected or the transmitted
microwave component. When the boron filaments were perpendicular with respect to the polarization of the microwave
beam (electric field vector), a maximum amount of energy was transmitted (or a minimum amount of energy reflected).
When the boron filaments and the polarization were parallel, the reverse was true. By continuously rotating the sample, a
sinusoidal pattern of filament direction versus signal amplitude was obtained.
Microwave Inspection
William L. Rollwitz, Southwest Research Institute
Stress-Corrosion Microwave Measurements
Materials such as aluminum, magnesium, and titanium are subject to stress-corrosion cracking or fatigue when they are
under stress in a corrosion-producing environment. Cracks and fatigue can appear at stress values much less than the
normal yield in a corroded material. Early fatigue may occur at less than rated load in a structure that has corroded
materials. For reliable structures that may be constructed from corroded materials or from materials corroded after
construction, it is necessary to have a method for detecting corrosion-prone and corroded areas of materials.
Several mechanisms have been suggested to explain stress-corrosion cracking and fatigue (Ref 20). Three of them are
electromechanical, mechanical, and surface energy. Similarities among these mechanisms suggest an approach to the
detection of corroded or corrosion-prone areas of the above materials.
All of these theories suggest that corrosion and the subsequent cracking begin at crystal lattice imperfections. The
imperfections considered are dislocations, vacancies, and impurities. It was assumed that if the existence of these
imperfections could be detected by a nondestructive method, then that method could be used to evaluate the stress-
corrosion susceptibility of materials and structures so as to eliminate corrosion-prone or corroded materials.
The correlation between electrical resistivity and dislocation density has been discussed by many authors (Ref 21, 22, 23,
24). It has also been found that the concentration of impurities varies the electrical resistivity of a material. It is further
mentioned that there is a difference in the surface resistivity between dislocations caused by vacancies and impurities.
Surface resistivity can be measured with high-frequency electromagnetic waves because they penetrate to a depth of only
10 to 0.1 m (400 to 4 in.) or less into the surface and because the wave reflected from the surface has its phase
changed from that of the incident wave by the action of the surface impedance, which includes the resistance of the
material. Any protective coating such as paint or oxides on the surface of the metal will allow most of the energy in the
electromagnetic wave to pass through them and to be reflected from the conductive surface, if the frequency used is in the
microwave region or below. However, the higher the frequency, the greater will be the magnitude of the change in the
surface impedance caused by imperfections. Therefore, although frequencies from microwaves through the ultraviolet can
be used, less interferences from surface coatings coupled with a relatively high sensitivity will be found in the microwave
region from 1 to 100 GHz.
Therefore, a measurement of the microwave surface impedance by means of a comparison of the reflected wave with the
incident wave should yield a measure of the imperfection density. A microwave system for measuring the surface
impedance of a metal can be adapted and calibrated for the determination of the corrosion-prone areas in materials.
Measurements of resistivity have been made on many metals and alloys, including aluminum, showing the resistivity to
be dependent on the dislocation density (Ref 21, 22, 23, 24). Also, a difference in resistivity of dislocations related to
vacancies and impurities has been measured (Ref 21, 22, 23, 24). The imperfection densities have been determined with
an electron microscope, and good agreement has been obtained between the experimental and theoretical values for the
resistivity of dislocations (Ref 21, 22, 23, 24). For aluminum, the average dislocation resistance was found to be 7 × 10
-19
D · · cm
3
, where D is the dislocation density of D · cm
-2
(Ref 21, 22, 23, 24). The vacancy resistivity was also found to