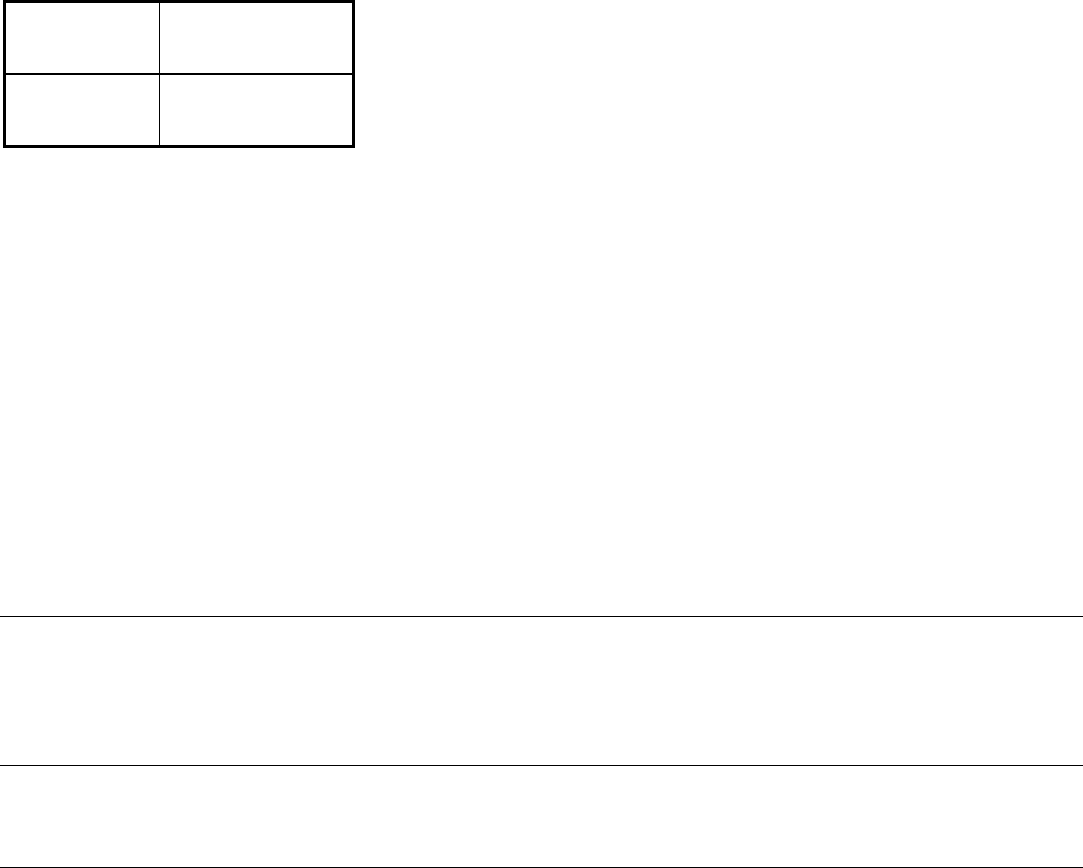
Y
170-260
J 220-325
Source: Ref 1
Although the general nature of microwaves has been known since the time of Maxwell, not until World War II did
microwave generators and receivers useful for the inspection of material become available. One of the first important uses
of microwaves was for radar. Their first use in nondestructive evaluation (NDE) was for components such as waveguides,
attenuators, cavities, antennas, and antenna covers (radomes). The interaction of microwave electromagnetic energy with
a material involves the effect of the material on the electric and magnetic fields that constitute the electromagnetic wave,
that is, the interaction of the electric and magnetic fields with the conductivity, permittivity, and permeability of the
material. Microwaves behave much like light waves in that they travel in straight lines until they are reflected, refracted,
diffracted, or scattered. Because microwaves have wavelengths that are 10
4
to 10
5
times longer than those of light waves,
microwaves penetrate deeply into materials, with the depth of penetration dependent on the conductivity, permittivity, and
permeability of the materials. Microwaves are also reflected from any internal boundaries and interact with the molecules
that constitute the material. For example, it was found that the best source for the thickness and voids in radomes was the
microwaves generated within the radomes. Both continuous and pulsed incident waves were used in these tests, and either
reflected or transmitted waves were measured.
Reference
1.
Electromagnetic Testing, Vol 4, 2nd ed., Nondestructive Testing Handbook,
Nondestructive Testing, 1986
Microwave Inspection
William L. Rollwitz, Southwest Research Institute
Microwave Inspection Applications
The use of microwaves for evaluating material properties and discontinuities in materials other than radomes began with
the evaluation of the concentration of moisture in dielectric materials. Microwaves of an appropriate wavelength were
found to be strongly absorbed and scattered by water molecules. When the dry host material is essentially transparent to
the microwaves, the moisture measurement is readily made.
Next, the thickness of thin metallic coatings on nonmetallic substrates and of dielectric slabs was measured. In this case,
incident and reflected waves were allowed to combine to form a standing wave. Measurements were then made on the
standing wave because it provided a scale sensitive to the material thickness.
The measurement of thickness was followed by the determination of voids, delaminations, macroporosity, inclusions, and
other flaws in plastic or ceramic materials. Microwave techniques were also used to detect flaws in bonded honeycomb
structures and in fiber-wound and laminar composite materials. For most measurements, the reflected wave was found to
be most useful, and the use of frequency modulation provided the necessary depth sensitivity. Success in these
measurements also indicated that microwave techniques could give information related to changes in chemical or
molecular structure that affect the dielectric constant and dissipation of energy at microwave frequencies. Some of the
properties measured include polymerization, oxidation, esterification, distillation, and vulcanization.
Advantages. In comparison with ultrasonic inspection and x-ray radiographic inspection, the advantages of inspection
with microwaves are as follows: