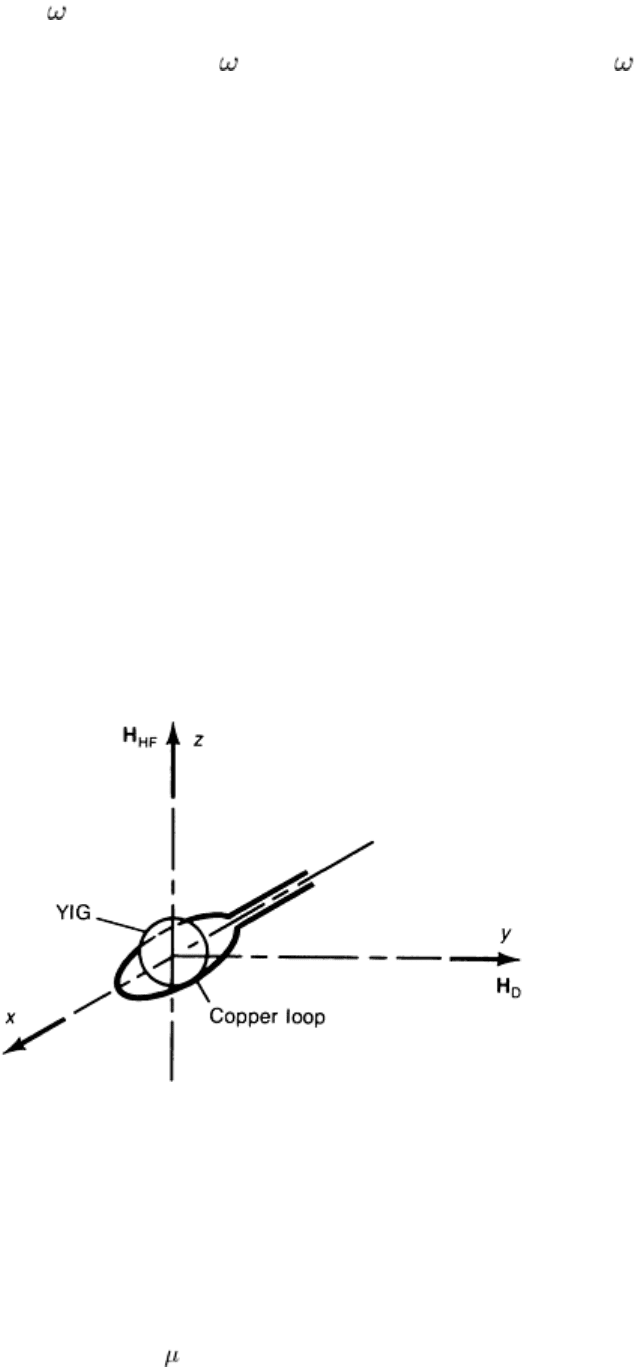
(m
RF
V
s
), where V
s
is the volume of the sphere. The dipole moment, because of the cross product between H
DC
and m
RF
, is
precessing about H
DC
at a frequency , according to the right-hand rule, in a plane perpendicular to H
DC
, as shown in Fig.
36. The precession is at the frequency of the drive current, I, applied to the coupling coil. The dipole moment m
RF
obtains
its maximum amplitude when the precession frequency
0
(Eq 14) equals the precession frequency . The time-varying
magnetic fields are created outside of the sphere by this rotating dipole moment. These outside time-varying magnetic
fields interact with a flaw in the material and produce a flaw-detecting signal in the same way that the time-alternating
magnetic fields do from low-frequency (conventional) eddy current probes.
In practice, the YIG sphere is mounted in a depression on a piece of microwave circuit board with a loop etched on the
board. Wire leads connect the end of the loop to a semirigid coaxial transmission line. A small samarium-cobalt magnet in
a brass holder supplies the bias field. The placement of the magnet can be adjusted to change the field orientation and the
resonant frequency. This eddy current probe, because of its small size, gives excellent spatial resolution, discrimination
against edge effects, and accessibility to restricted corners.
The high sensitivity and spatial resolution of the FMR eddy current probe have been experimentally verified (Ref 34, 39).
In one case, the FMR probe was found to be 40 times more sensitive to an open slot than a commercial 100-kHz probe.
The correlation between the flaw signature, detected by the FMR probe, and the width of the opening of a stressed fatigue
crack has also been demonstrated.
Another group of researchers has applied the FMR probe to aluminum, type 316 stainless steel, Armco iron, and XC-38
(Ref 41). They used the YIG and gallium-doped yttrium iron garnet (GaYIG). The main difference between this garnet
and the previous garnet is that the saturation magnetization is fixed at 0.075 T (750 G) for YIG, while that of the GaYIG
varies with the amount of gallium. The resonator principle that was used is given in Fig. 38. The characterization of the
spectrum line is done by measuring the reflection coefficient of the YIG resonator in Fig. 38. A microwave signal is
applied onto the garnet by means of the copper loop. In the absence of resonance, the wave is reflected. As the resonance
is approached, the incident wave is absorbed by the garnet, and the reflected wave is highly attenuated. The reflection
coefficient is characterized either by a scaler analysis or by a vector analysis.
Fig. 38 Schematic of YIG resonator principle. H
D
, continuous magnetic field; H
HF
, microwave magnetic field.
Source: Ref 41
In air (uncoupled to a sample), the resonant frequency is proportional to the applied bias field H
D
in Fig. 38. The
proportionality constant is 2.8 MHz/Oe. The resonance lines for YIG are located above 3 GHz. For GaYIG, the resonance
frequency can go down to less than 1 GHz.
The garnets used have diameters of 375 or 500 m (0.015 or 0.020 in.). The only garnets used were the YIG, which
required a bias magnetic field between 80 and 160 kA · m
-1
(1000 and 2000 Oe). The microwave loop is made on a
printed circuit. Experience with microwave oscillators has shown that this loop should have a diameter of about 1.5 times
that of the garnet and that the copper width should be 0.1 mm 0.004 in.).