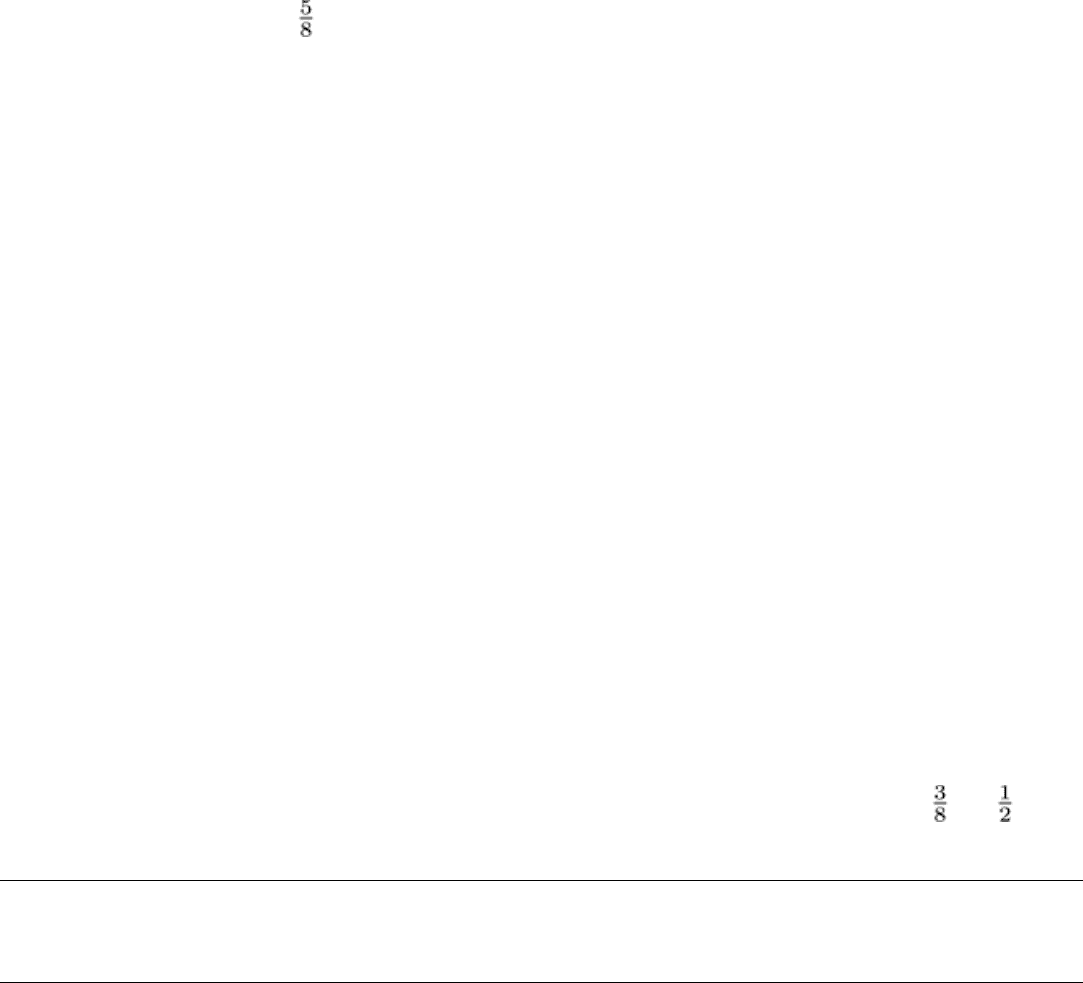
Inspection is accomplished by eddy currents that are induced in the bar from a small probe coil, which also serves as the
detector coil. When a surface discontinuity is encountered, the eddy currents are forced to flow beneath the discontinuity
to complete their path. This increases the length of the path of the eddy currents and thus increases the electrical
resistance to the flow of eddy currents in the bar. The change in resistance is proportional to the depth of the
discontinuity. The probe coil detects the change in resistance, and this is interpreted by the instrument in terms of the
depth of the discontinuity.
The probe coil is about 16 mm ( in.) in diameter. It is encapsulated and mounted in a stainless steel housing between
two carbide wear shoes. The probe coil is flexibly supported and mechanically biased to ride against the surface of the
bar. The bars are rotated and propelled longitudinally. This combination of rotary and longitudinal motion causes the
probe (detector) coil to trace on the bar a helical path with a pitch of approximately 75 mm (3 in.). The rolling process by
which bars are produced greatly elongates the natural discontinuities so that they are usually several inches in length. The
75 mm (3 in.) pitch of the helical scan has been found to be more than adequate to detect almost all discontinuities.
A nominal helical scanning speed of 30 m/min (100 sfm) has provided good results. Where higher inspection rates are
desired, multiple-probe-coil machines are used. Such machines have been built with as many as six probe coils.
The locations of discontinuities are marked exactly on the bar by a small, high-speed rotary milling device mounted
downstream of the probe. The milling cutter is brought into momentary contact with the bar precisely one revolution after
the discontinuity has passed the probe coil. This provides a shallow mark exactly on the discontinuity. Because the mark
is a bright milled spot, it is easy to see and will not smear or rub off.
These machines are completely automatic and, after setup, require no attention other than crane service for loading the
feed table and for unloading the cradles after the bars have been inspected. The instrumentation is provided with two
separate alarm controls that can be set as required. For example, one alarm might be set to register all discontinuities over
0.25 mm (0.010 in.) in depth. The second alarm might be set to register all discontinuities over 1.52 mm (0.060 in.) in
depth.
When a bar is being inspected, the outputs from the two alarms are fed into a discontinuity analyzer (computer). This
device can be set to respond to a wide variety of conditions, depending on requirements. For example, a bar that produced
no response from either alarm would always be rated as prime. However, if it is acceptable for a specified percentage of
discontinuities over 0.25 mm (0.010 in.) but less than 1.52 mm (0.060 in.) to be in the material, the discontinuity analyzer
can be set to classify as prime whatever length of discontinuity is permissible. Perhaps a few very short discontinuities
over 1.52 mm (0.060 in.) can be accepted either as prime or as salvageable. If so, the analyzer is set to meet either of these
requirements. The combination of two alarms at different, but adjustable, levels and the versatility of the discontinuity
analyzer provide great flexibility in meeting specific material requirements. Inspection efficiency is also improved
because the inspection can be adjusted to give a product that meets requirements but is not overgraded. This minimizes
costs and scrap losses. These machines have been built to inspect round bars from 9.5 to 114 mm ( to 4 in.) in
diameter and from 1.5 to 15 m (5 to 50 ft) in length.
Eddy Current Inspection
Revised by the ASM Committee on Eddy Current Inspection
*
Inspection of Welds in Welded Tubing and Pipe
Longitudinal welds in welded tubing and pipe can be inspected for discontinuities using eddy current techniques with an
external encircling primary energizing coil and a probe-type differential detector coil. The probe-type detector coil is
located at the longitudinal center in the inner periphery of the primary coil and is arranged so that it inspects the outside
surface of the longitudinal weld.
The inspection, as shown in Fig. 39, is performed by passing the tube or pipe longitudinally through the primary
energizing coil, causing the probe-type detector coil to traverse the longitudinal weld from end to end. The primary coil is
energized with alternating current at a frequency that is suitable for the part being inspected (typically 1 kHz for
ferromagnetic products) and induces the eddy currents in the tube or pipe.