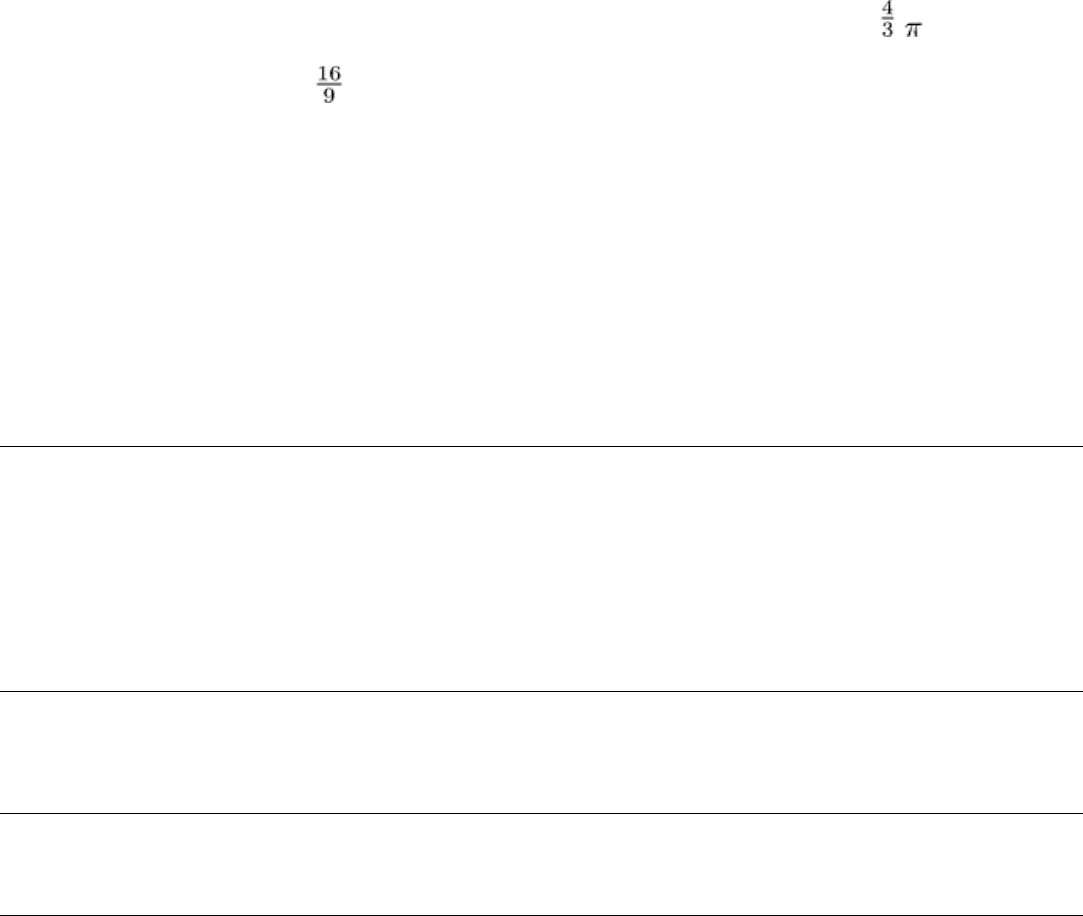
where SOF is the shape and orientation factor of the flaw. If there is only one coil, then A
1
= A
2
, and the mutual
impedance becomes the self-impedance of the coil.
In general, the SOF is a complex function of the shape and orientation of the flaw relative to the eddy current fields.
However, there are two special cases of interest for which the SOF is relatively simple: the sphere and the circular disk, or
penny flaw. For the spherical void, the shape and orientation factor SOF is 1, and the volume is ( ) a
3
, where a is the
radius of the sphere. For a circular disk oriented with the circle perpendicular to the eddy current field direction, the
product of the volume and SOF is ( )a
3
. The same theory can also be applied to surface counterparts of these two flaws:
the hemisphere and the half disk, or half penny flaw. In both of these cases, the product of the volume of SOF is half that
of their subsurface counterparts, because of the volume being halved.
The other part of Burrows's formula requires determination of the magnitudes of the magnetic vector potentials, A
1
and
A
2
. Formulas for calculating the magnetic vector potential fields of coils in proximity to conductors are given in Ref 3.
These formulas are in the form of definite integrals, which can be evaluated by computer for the geometry of interest.
There have been numerous extensions to the Burrows formulation of the impedance change formula that relax the
restriction that the flaw size be small compared to the skin depth and extend the range of flaw shapes for which the SOF
can be calculated. However, the solution remains in the basic form given by Burrows, which shows the dependence of the
impedance change on the square of the field strength and the effective volume and orientation of the flaw.
References cited in this section
1.
M.L. Burrows, "A Theory of Eddy Current Flaw Detection," University Microfilms, Inc., 1964
2.
C.V. Dodd, W.E. Deeds, and W.G. Spoeri, Optimizing Defect Detection in Eddy Current Testing,
Eval., March 1971, p 59-63
3.
C.V. Dodd and W.E. Deeds, Analytical Solutions to Eddy-Current Probe-Coil Problems, J. Appl. Phys.,
39 (No. 6), May 1968, p 2829-2838
Note cited in this section
** This section was prepared by Thomas Kincaid, Boston University.
Eddy Current Inspection
Revised by the ASM Committee on Eddy Current Inspection
*
Inspection Frequencies
The inspection frequencies used in eddy current inspection range from about 200 Hz to 6 MHz or more. Inspections of
nonmagnetic materials are usually performed at a few kilohertz. In general, the lower frequencies, which start at about 1
kHz, are used for inspecting magnetic materials. However, the actual frequency used in any specific eddy current
inspection will depend on the thickness of the material being inspected, the desired depth of penetration, the degree of
sensitivity or resolution required, and the purpose of the inspection.
Selection of inspection frequency is normally a compromise. For example, penetration should be sufficient to reach any
subsurface flaws that must be detected. Although penetration is greater at lower frequencies, it does not follow that as low
a frequency as possible should be used. Unfortunately, as the frequency is lowered, the sensitivity to flaws decreases
somewhat, and the speed of inspection can be curtailed. Normally, therefore, an inspection frequency as high as possible
that is still compatible with the penetration depth required is selected. The choice is relatively simple when detecting
surface flaws only, in which case frequencies up to several megahertz can be used. When detecting flaws at some