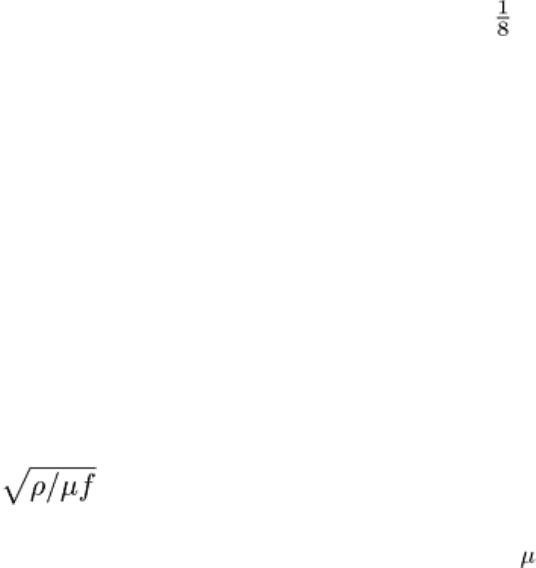
Fig. 9 Impedance-plane diagram showing curves for electrical conductivity and lift-off.
100 kHz.
Although troublesome in many applications, lift-off can also be useful. For example, with the lift-off effect, eddy current
instruments are excellent for measuring the thickness of nonconductive coatings, such as paint and anodized coatings, on
metals.
Fill Factor
In an encircling coil, a condition comparable to lift-off is known as fill factor. It is a measure of how well the part being
inspected fills the coil. As with lift-off, changes in fill factor resulting from such factors as variations in outside diameter
must be controlled because small changes can give large indications. The lift-off curves shown in Fig. 9 are very similar
to those for changes in fill factor. For a given lift-off or fill factor, the conductivity curve will shift to a new position, as
indicated in Fig. 9. Fill factor can sometimes be used as a rapid method for checking variations in outside diameter
measurements in rods and bars.
For an internal, or bobbin-type, coil, the fill factor measures how well the inspection coil fills the inside of the tubing
being inspected. Variations in the inside diameter of the part must be controlled because small changes in the diameter
can give large indications.
Edge Effect
When an inspection coil approaches the end or edge of a part being inspected, the eddy currents are distorted because they
are unable to flow beyond the edge of a part. The distortion of eddy currents results in an indication known as edge effect.
Because the magnitude of the effect is very large, it limits inspection near edges. Unlike lift-off, little can be done to
eliminate edge effect. A reduction in coil size will lessen the effect somewhat, but there are practical limits that dictate the
sizes of coils for given applications. In general, it is not advisable to inspect any closer than 3.2 mm ( in.) from the edge
of a part, depending on variables such as coil size and test frequency.
Skin Effect
In addition to the geometric relationship that exists between the inspection coil and the part being inspected, the thickness
and shape of the part itself will affect eddy current response. Eddy currents are not uniformly distributed throughout a part
being inspected; rather, they are densest at the surface immediately beneath the coil and become progressively less dense
with increasing distance below the surface--a phenomenon known as the skin effect. At some distance below the surface
of a thick part there will be essentially no currents flowing.
Figure 10 shows how the eddy current varies as a function of depth below the surface. The depth at which the density of
the eddy current is reduced to a level about 37% of the density at the surface is defined as the standard depth of
penetration. This depth depends on the electrical conductivity and magnetic permeability of the material and on the
frequency of the magnetizing current. Depth of penetration decreases with increases in conductivity, permeability, or
inspection frequency. The standard depth of penetration can be calculated from:
S = 1980
(Eq 1)
where S is the standard depth of penetration (in inches), ρ is the resistivity (in ohm-centimeters), is the magnetic
permeability (1 for nonmagnetic materials), and f is the inspection frequency (in hertz). Resistivity, it should be noted, is
the reciprocal of conductivity. The standard depth of penetration, as a function of inspection frequency, is shown for
several metals at various electrical conductivities in Fig. 11.