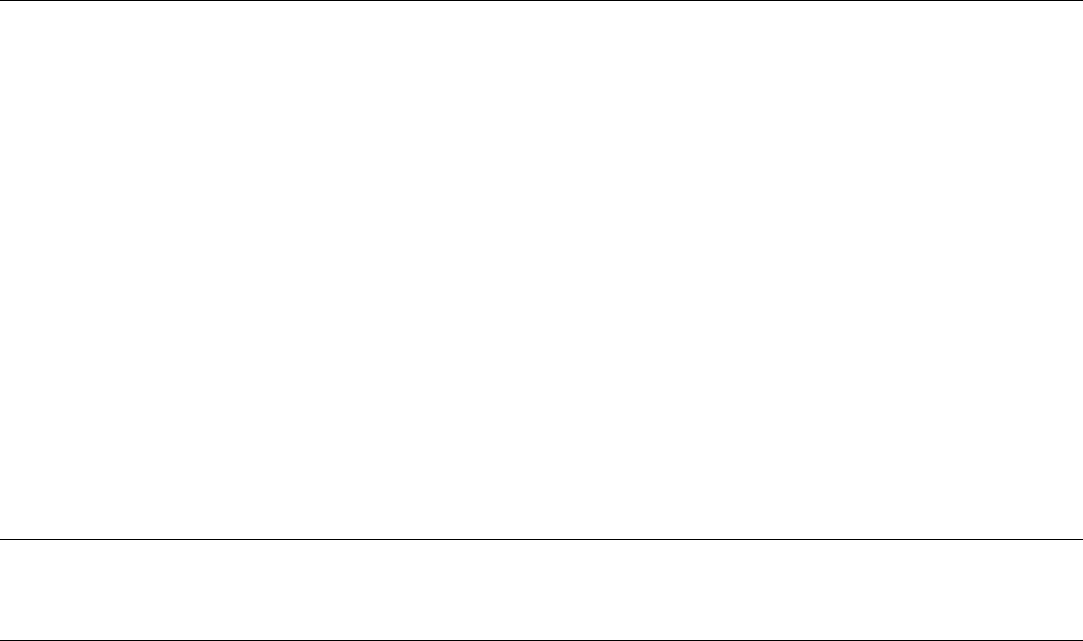
where K is the calibration constant for the material. When the parallel and perpendicular amplitudes are equal, the stress
is zero whatever the amplitudes are. When the parallel/perpendicular ratio is greater than one, the stress value is positive
and is tension; when the ratio is less than one, the stress is negative or compression.
The calibration constant, K, is obtained from Fig. 29 by the following procedure: (a) draw a calibration line through the
origin at an angle for which an applied stress can be assigned to the intersection of the parallel/perpendicular ratio for the
applied stress and (b), calculate the value of the constant K by inserting the applied stress and the angle into Eq 19.
Before this procedure could be used with the data in Fig. 29, the usable applied stress curve had to be chosen. One of the
applied stress curves from sample No. 7 was chosen because its amplitude was the closest to the residual stress data, and
because its curve shape was close to that obtained from the throw. The calibration proceeded as described. The line at 50°
was chosen for the first calibration value because it intersected the lowest amplitude (dashed curve) for the data from
sample 7 at nearly the value of applied stress level B (closed circle) (55 MPa, or 8 ksi). The 45° line passes through the
No. 7 stress curve (dashed) nearly at level C (open triangle), or where an estimated value of 160 MPa (23.5 ksi) had been
applied. Therefore, the line at an angle of 50° represents a differential applied stress relative to the 45° line of 160 - 55 =
105 MPa (23.5 - 8 = 15.5 ksi). When several values are taken from several lines both above and below the 45° line, the
average value for a line 5° above or below 45° is 100 MPa (15 ksi). Therefore, if both the value of tan
-1
50° and the stress
equal to 100 MPa (15 ksi) are inserted into Eq 19, the value of K is found to be 20 MPa/degree (3 ksi/degree). This
implies that for every degree of offset from the 45° line, points along the line at that offset resulting from signal amplitude
measurements will have the same value of residual stress.
When the value of K is used, calibration lines can be drawn through zero at useful angles relative to the 45° line. Using
these calibration lines and marks, the values of the residual stresses for points on the crankshaft throw were determined.
Residual stress values as high as 600 MPa (87 ksi) tension and 90 MPa (13 ksi) compression were determined.
References cited in this section
3. W.L. Rollwitz, "Magnetoabsorption," Final Report, Research Project No. 712-
Institute, 1958
4. W.L. Rollwitz and A.W. Whitney, "Special Te
chniques for Measuring Material Properties," Technical
Report ASD-TDR-64-123, USAF Contract No. AF-33(657)-10326, Air Force Materials Laboratory, 1964
5.
W.L. Rollwitz and J.P. Classen, "Magnetoabsorption Techniques for Measuring Material Properties,"
Technical Report AFML-TR-65-17, USAF Contract No. AF-33(657)-
10326, Air Force Materials
Laboratory, 1965
6.
W.L. Rollwitz and J.P. Classen, "Magnetoabsorption Techniques for Measuring Material Properties,"
Technical Report AFML-TR-66-76 (Part I), USAF Contract No. AF-33(657)-
10326, Air Force Materials
Laboratory, 1966
7.
W.L. Rollwitz, "Magnetoabsorption Techniques for Measuring Material Properties. Part II. Measurements
of Residual and Applied Stress." Technical Report AFML-TR-66-76 (Part II), USAF Contract No. AF-
33(615)-5068, Air Force Materials Laboratory, 1968
11.
W.L. Rollwitz, "Preliminary Magnetoabsorption Measurements of Stress in a Crankshaft Throw," Summary
Report on Project 15-2438, Southwest Research Institute, 1970
Magabsorption NDE
William L. Rollwitz, Southwest Research Institute
References
1. W.E. Bell, Magnetoabsorption,
Vol 2, Proceedings of the Conference on Magnetism and Magnetic
Materials, American Institute of Physics, 1956, p 305
2. R.M. Bozorth, Magnetism and Electrical Properties, in Ferromagnetism, D. Van Nostrand, 1951, p 745-
768