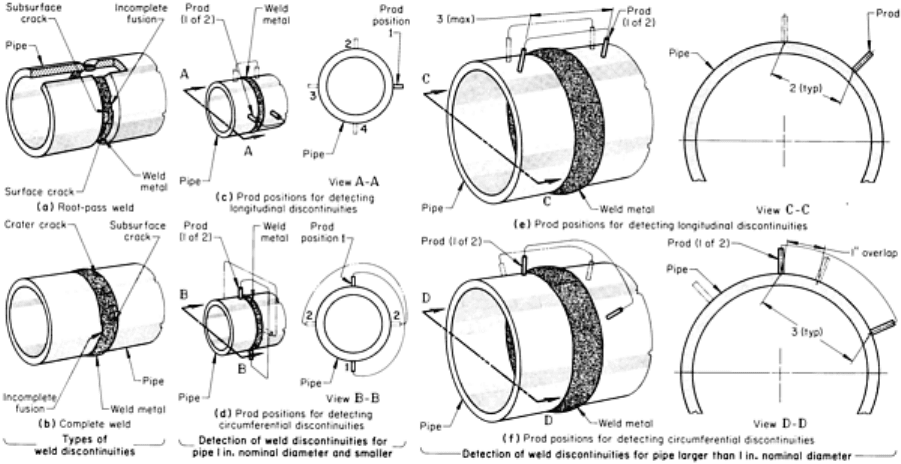
Welds in Carbon Steel Pipe. Magnetic particle inspection using the prod technique is a reliable method of detecting
discontinuities in consumable-insert root welds and final welds in carbon steel pipe up to 75 mm (3 in.) in nominal
diameter. (For larger-diameter pipe, less time-consuming magnetic particle techniques can be used.) The types of
discontinuities found in root welds are shown in Fig. 39(a), and those found in final welds are shown in Fig. 39(b).
Fig. 39 Magnetic particle inspection for detection of discontinuities in consumable-
insert root welds and final
welds in carbon steel pipe. Dimensions given in inches
Placement of the prods is important to ensure reliable inspection of the welds. Circular magnetization, used to check for
longitudinal discontinuities, is accomplished by placing the prods at 90° intervals (four prod placements) around the pipe,
as shown in Fig. 39(c). For pipes larger than 25 mm (1 in.) in nominal diameter, prods should be spaced around the pipe
at approximately 50 mm (2 in.) intervals, as shown in Fig. 39(e). Circumferentially oriented discontinuities are revealed
by placing the prods as shown in Fig. 39(d). The prods are placed adjacent to and on opposite sides of the weld bead to
ensure flux flow across the weld metal. If the circumferential distance between the prods is greater than 75 mm (3 in.)
when positioned as shown in Fig. 39(d), the prods should be positioned as shown in Fig. 39(f). To ensure proper
magnetization, the areas inspected should overlap approximately 25 mm (1 in.). Magnetic particles are applied to the weld
area while the current is on because of the low retentivity of carbon steel.
A buildup of magnetic particles in the fusion-line crevice of the weld is indicative of either a subsurface discontinuity or a
nonrelevant indication because of the abrupt change in material thickness and/or the crevicelike depression between the
weld metal and the base metal. However, a true indication, as from incomplete fusion between the weld metal and the
base metal, would be a sharply defined particle pattern. This pattern would be difficult if not impossible to remove by
blowing with a hand-held powder blower while the magnetizing current is being applied. If the indication at the fusion
zone can be blown away with a hand-held powder blower, the indication is nonrelevant. The current used is
approximately 3.9 A/mm (100 A/in.) of prod spacing.
Hollow cylinders closed at one end, such as drawn shells or forged fluid-power cylinders, can be magnetized
circumferentially for the inspection of longitudinal discontinuities using a head shot end-to-end. However, this technique
does not provide sensitivity for discontinuities on the inside surface.
As shown in Fig. 40, a central conductor can be used in such a manner that the closed end of the cylinder completes the
current path. Also, the open end of the cylinder is accessible for the application of a wet-particle bath to the inside
surface, which can then be inspected directly. For thin-wall cylinders, discontinuities on the inside surface produce
subsurface-type indications on the outside surface. The central-conductor method for magnetization is advantageous when
the inside diameter is too small to permit direct internal viewing.