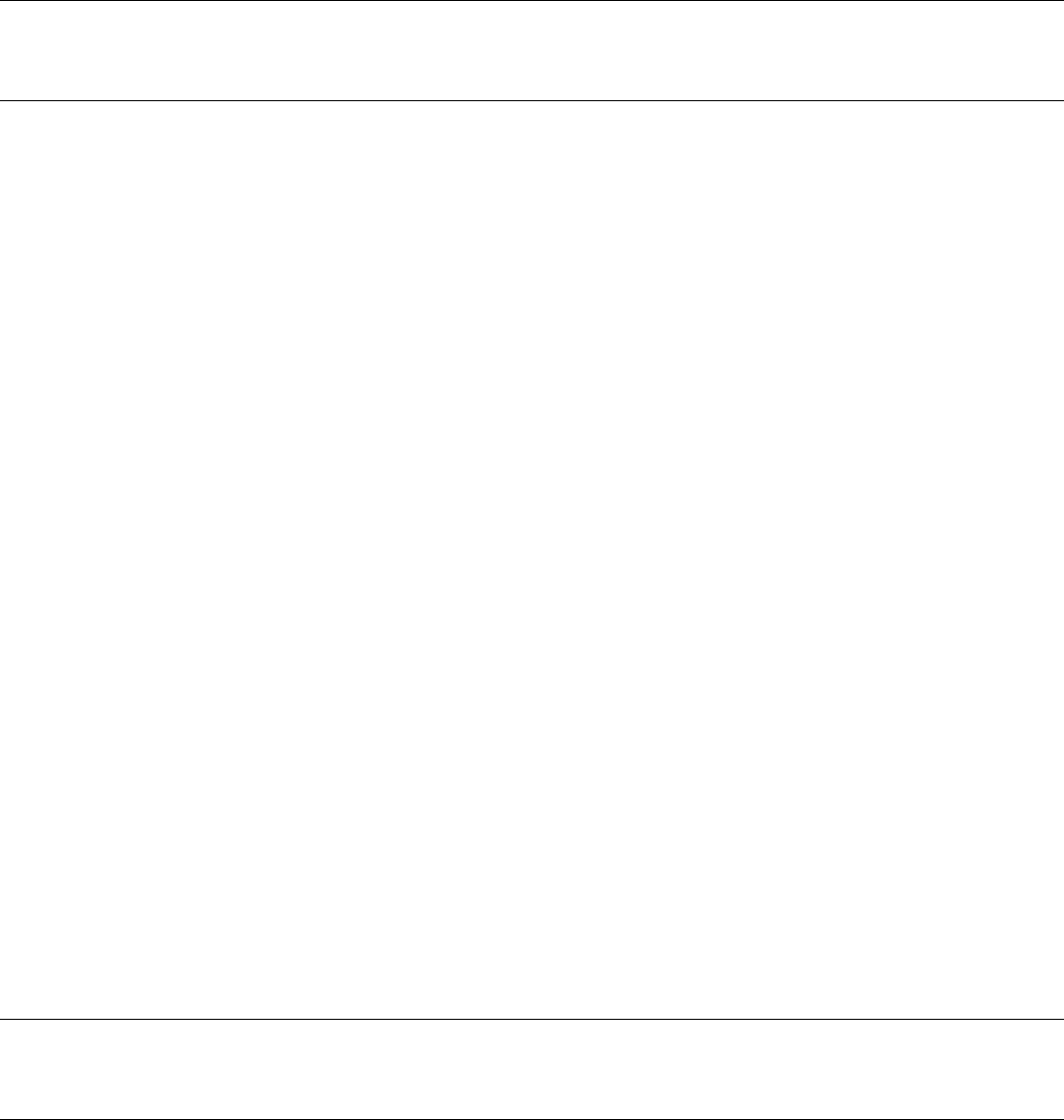
in regions where magnetic particles have been attracted by changes in magnetic permeability. The magnetic particles are
made of ferromagnetic iron oxide (Fe
3
O
4
) and are similar to those used for conventional magnetic particle inspection.
Magnetically printed patterns are made visible by first spraying the surface of the testpiece with a white plastic coating.
The coating provides a contrasting background and a surface on which the particles print. After a print has been obtained
and the particles have been removed, the patterns can be fixed by spraying with a clear plastic coating. Because the two
coatings are of the same composition, a single film is formed, within which the printed pattern is sandwiched. When dry,
the coating can be stripped from the surface of the testpiece and used as a permanent record.
Magnetic Particle Inspection
Revised by Art Lindgren, Magnaflux Corporation
Procedure
The testpiece should be cleaned so that it is free of dirt, moisture, oil, paint, scale, and other materials that can obscure a
discontinuity or flaw. The white plastic coating is sprayed onto the test surface in an amount to establish a white
background to offset the color of the test surface. The coating should be free of puddles, runs, and signs of orange peel.
The coating is dried before application of the magnetizing current and particles.
With the magnetizing current on and properly adjusted, the testpiece and magnetic printer are placed adjacent to each
other, and dry printing particles are dusted on the test surface with a powder bulb applicator. The testpiece and printer can
be moved relative to each other to obtain uniform printing. When a suitable print has formed, usually after 6 to 12 s, the
magnetizing current is turned off. The excess magnetic printing particles can be removed with a gentle air blast or gentle
tapping.
If a suitable print has not been obtained, the print can be erased with a damp sponge, and the application of magnetizing
current and printing particles repeated. If a permanent record is needed, the printed surface is sprayed with two coats of
clear plastic. To assist in removing the coating, a piece of pressure-sensitive clear plastic tape can be applied to the
printed surface after the clear plastic coating has dried to the touch. Copies of magnetic printings can be made by
conventional photographic contact printing methods, using the magnetic printed record as a negative. A transparency for
projection purposes can be made by magnetic printing on the clear coating instead of the white coating. White or clear
nitrocellulose lacquer can be used in place of the strippable coatings when a permanent, nonstrippable magnetic print is
required.
On some occasions, the magnetic printing particles group together in certain areas of the part surface, reducing the
printing capabilities of the particles. When an aluminum alloy plate, such as 2024, is placed beneath the magnetizing coil
(with the coil between the aluminum alloy plate and the testpiece), the particles remain in constant dispersion, thus
preventing grouping.
A similar inspection method (U.S. Patent 3,826,917) uses a coating, preferably an organic coating, containing
fluorescent material and nonfluorescent particles, preferably suspended in a liquid medium. Magnetic-flux lines are
established substantially perpendicular to the suspected discontinuities in the surface of the testpiece. The particles
agglomerate and form indications on the coating adjacent to the discontinuities. The testpiece is inspected under ultra-
violet light to locate and reveal the surface discontinuities. If a permanent record is needed, a clear strippable plastic
coating is applied over the magnetic indications of imperfections, and the resulting coating is stripped from the surface.
Magnetic Particle Inspection
Revised by Art Lindgren, Magnaflux Corporation
Applications